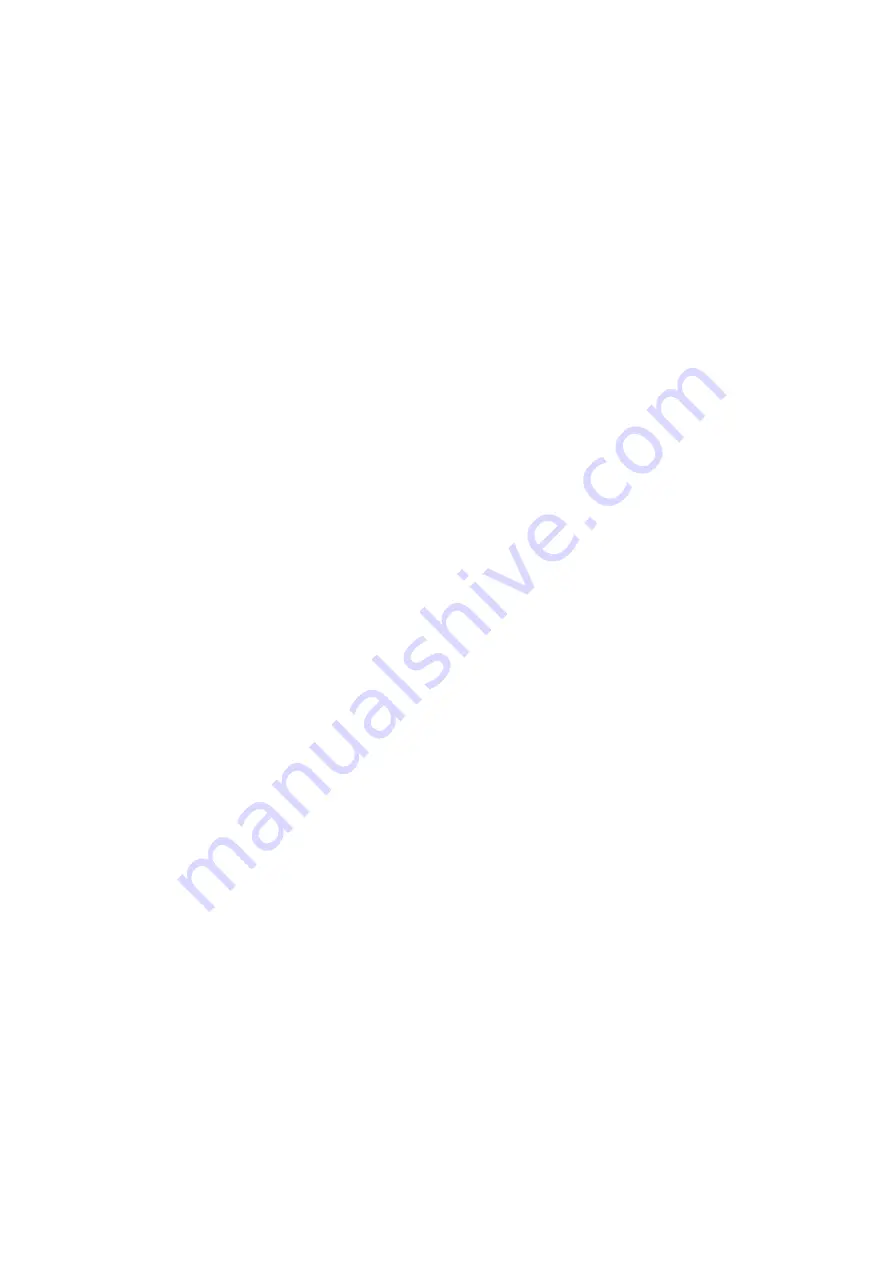
ProTec Polymer Processing GmbH
Foerdergeraet_FG201-FG206_BA_1v0_2018_en
44
b) External fill level indicator in the container for additive material
Only in combination with a dosing flap/dosing turnout. As empty
-
indicator it registered the
sinking of the material level and then restricts the suctioning of the additive material.
c) External fill level indicator in series with the proximity switch in the storage tank of the
processing machine. The conveying is thus first started when the discharge flap is closed and
the fill level indicator shows "empty".
7.2
2K- turnout and suction valve
Refer to separate operating instructions
7.3
Other connection options
7.3.1
External fault indicator
(lamp, alarm)
7.3.2 External START/STOP switch
Contact the service department of ProTec Polymer Processing GmbH for other options.