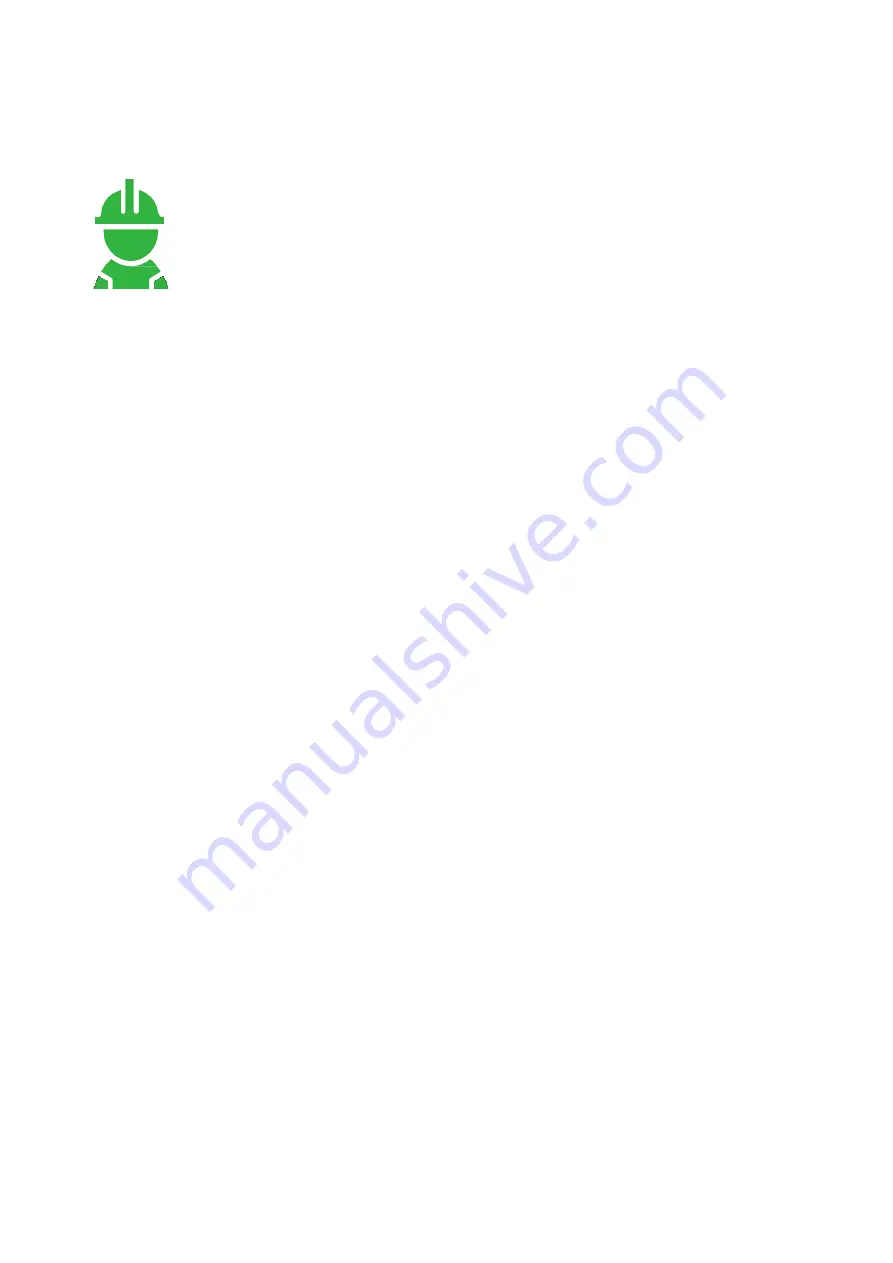
73
GENERAL STARTUP INSTRUCTIONS
Evacuation
To avoid inclusion of air or moisture in the refrigerant circuit, be sure to
execute vacuum drying of the entire circuit before charging refrigerant by
using a vacuum pump. Execute evacuation after securely carrying out a
pressure test.
> When performing vacuum drying, make sure that valve EC1 and
EC3 are fully open as well as the pressure balancing solenoid valves
Cx-VM11; please refer to chapter “Manual mode for evacuation
procedure”.
Dehydration of circuits
This operation must be carried out with all valves open (including solenoid valves) with
connection to a vacuum pump:
– of the low pressure side
– of the high pressure side
The quality of drying should not be judged by the speed at which the level of vacuum is
reached but on the effective time it is held (24 hours at 0.7 mbar is a good standard).
The total increase in pressure after that period should not be more than 2.6 mbar. The
residual moisture in the system should be less than 10 ppm.
When the installation is under vacuum, an insulation check of the motor should not be
carried out nor should the compressors be started before at least 1 bar of fluid pressure is
reintroduced.
This is to prevent motor winding damage.
Leak test
- The entire circuit must be pressurized with a neutral gas (Nitrogen U) supplemented
with a tracer gas (non-liquid and non-coloring) at a minimum pressure equal to 1.1
times the PS according to EN 378-2
- Proceed to systematic and careful leakage detection with a detector according to EN
14624 on the machine. After these tests, the gas will be blown out.
- Caution: During the operation not to exceed the PS of the circuits, which can lead
to the discharge of the safety devices and in particular of the BP and HP valves of
the compressors (category II)
Oil level control
- The oil levels must not be higher than the manufacturer's recommendations: mid
height of the sight glass during maximum operation for SH compressors.