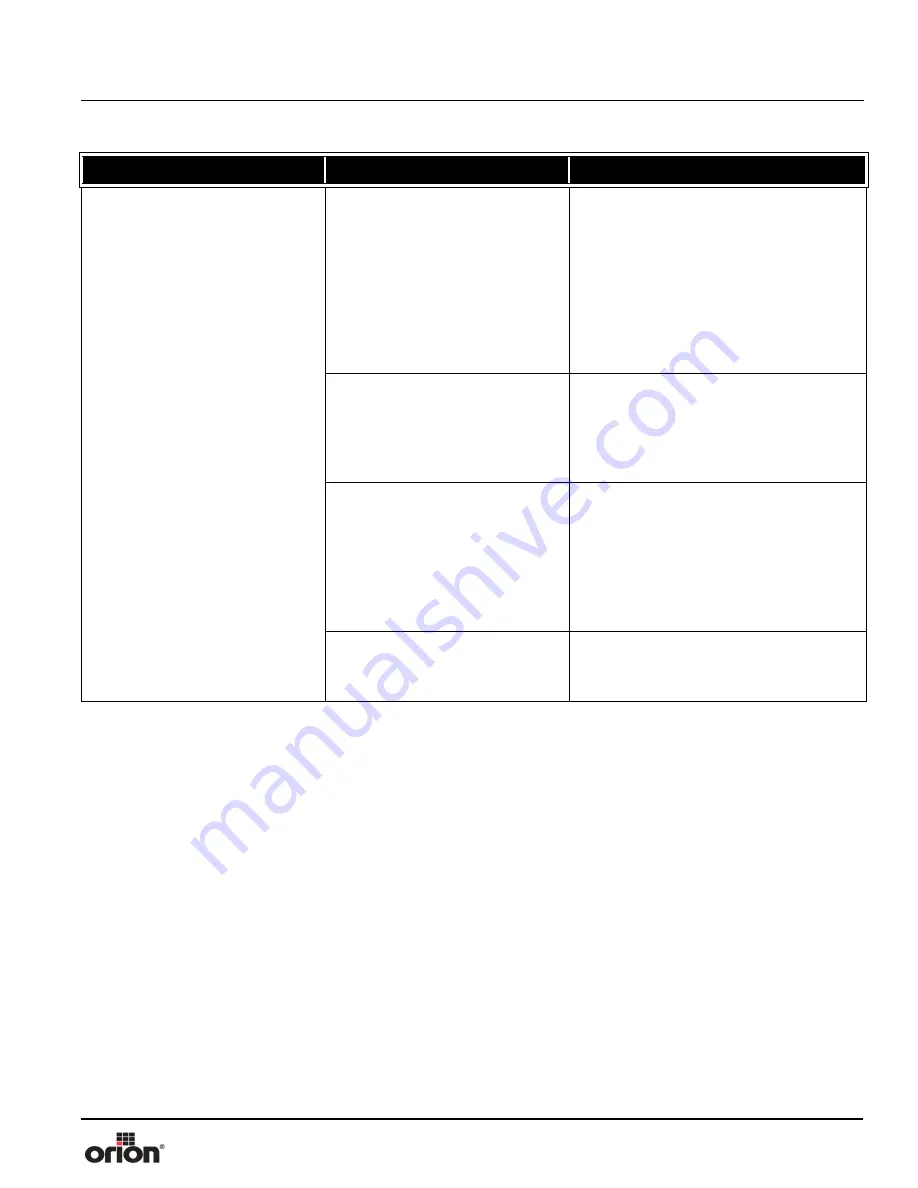
Orion
Machine Manual
Revision 3.0
CTS Flex Stretchwrapper
25 July 2016
Troubleshooting
Page 4-17
Film Cutter Not Cutting Film
Load not positioned properly.
Look for underhung loads, or loads that
are not centered on the table or in the
proper wrap zone (RT only). The rear side
of the load must be in line with the pallet
stop for the clamp, brush and cutter to
work properly.
Re-center the load to the proper position
on the table (or wrap zone on RT
machines).
Brush extend timer at the touch-
screen is incorrect for the applica-
tion.
Look for the arm to activate smoothly, but
at the wrong time.
Observe the factory preset value on the
settings screen. Re-adjust the brush extend
timer as needed.
Cutter wire is loose.
Check for wavy or bent cutter wire. The
wire expands as it is heated. If the wire is
not straight and under tension, then it will
not be in the correct position to cut prop-
erly.
If wire is loose or bent, repair or replace
the wire.
Blown Fuse.
Locate hot wire control fuse. Remove fuse
and check continuity.
Bad Fuse? Replace with correct type.
Table 4-1. Troubleshooting Chart (Continued)
PROBLEM
POSSIBLE CAUSE
SOLUTION
Summary of Contents for Orion CTS Flex Stretchwrapper
Page 114: ...Machine Manual Orion CTS Flex Stretchwrapper Revision 3 0 Maintenance 25 July 2016 Page 5 10...
Page 118: ......
Page 119: ......
Page 120: ......
Page 121: ......
Page 122: ......
Page 123: ......
Page 124: ......
Page 125: ......
Page 126: ......
Page 127: ......
Page 128: ......
Page 129: ...DC OK Adjust 24V 2 5A L N 100 240V 1 5A 50 60Hz G R...
Page 130: ......
Page 131: ......