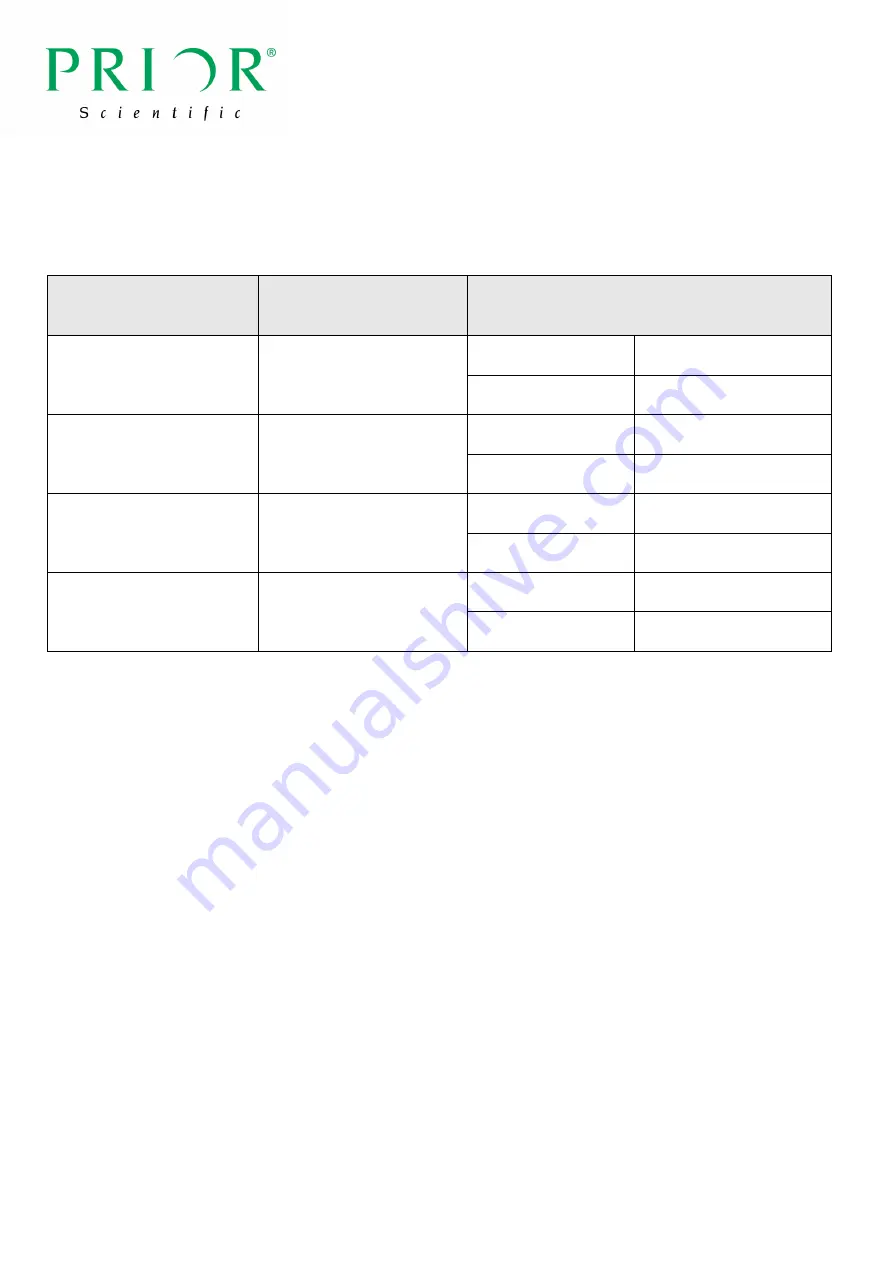
25
Enter 100 into the step size box in the Z-position field in the GUI. Click ‘step up’ and check the direction
the objective moves relative to the sample. If movement is too small to be visible, increase this value
up in 100-unit steps until the movement can be seen. Depending on the direction of movement,
change settings in the PID or mode submenus.
The table below is a guide to expected settings but
please note that the settings actually required may be different.
Nanopositioning system
type
Initial Objective
Movement
Suggested settings
Objective positioner
Away from sample
PID
Positive
Mode
Inverted
Objective positioner
Towards sample
PID
Negative
Mode
Non-inverted
Z-stage
Sample moves away
from objective
PID
Positive
Mode
Inverted
Z-stage
Sample moves towards
from objective
PID
Negative
Mode
Non-inverted
The aim of this procedure is to configure your system such that clicking ‘step up’ causes the distance
between the sample and objective to increase.
Section 6: Autofocus Parameter Setup
6.1 Installation Review
Sections 3, 4 and 5 are only required during the initial system setup and should only be performed
once per installation. This concludes the configuration of the PureFocus850 with the microscope. The
following sections guide the user through setting parameters specific to their samples and objectives,
and therefore these parameters may require adjustment if the samples and objectives used with the
PureFocus850 change.
Complete the following autofocus parameter setup first using the PF209 setup slide in order to ensure
user familiarity with the various controls. Once the offset value has been saved and PureFocus850
servo has been successfully activated using the setup slide, review and adjust the parameters in line
with your samples by repeating the procedure. The below table shows which element of the setup
slide is best used as a starting point for various sample types.