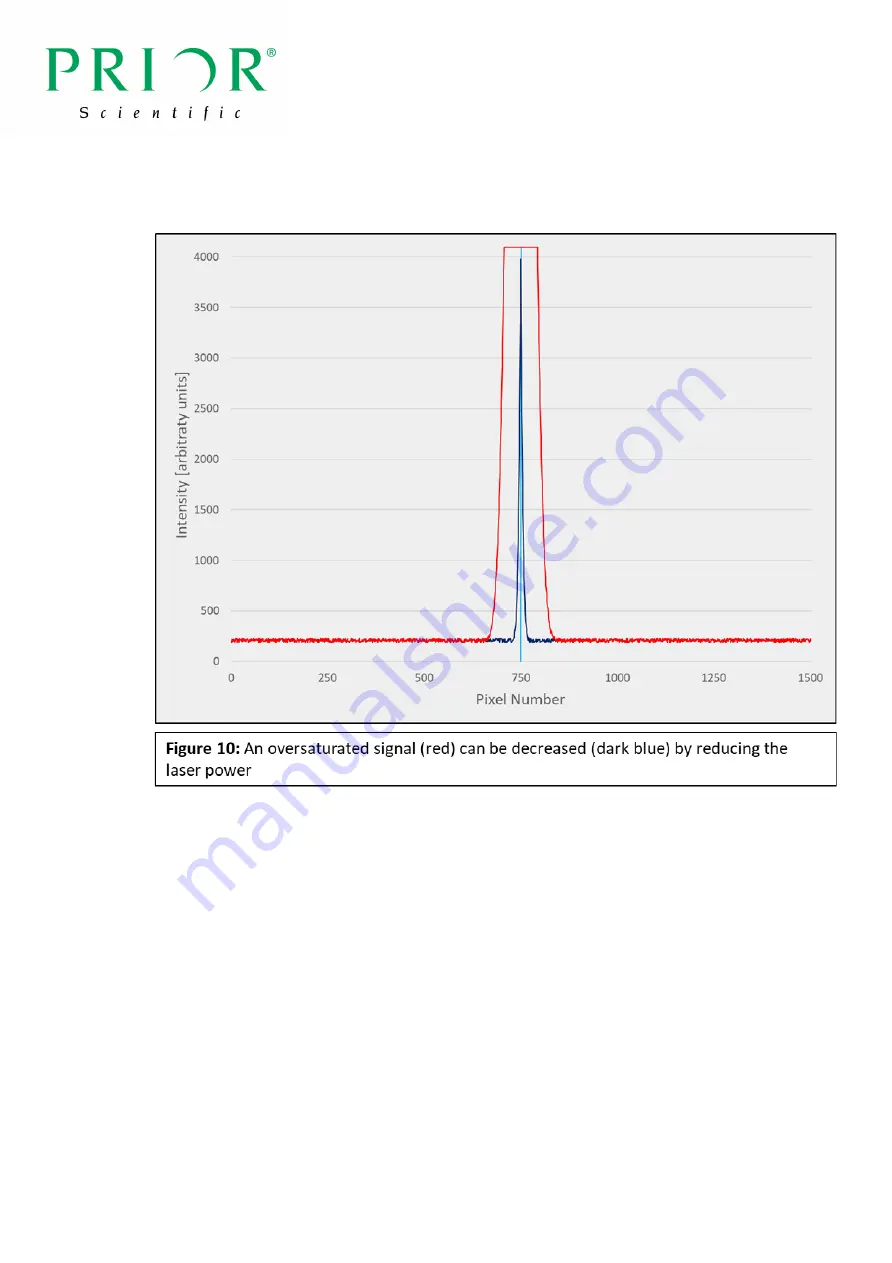
19
before continuing. If necessary, adjust the 45
o
further to maximise the size of the peak.
After maximising the size of the peak, if the peak crosses the top of the graph reduce
the laser power until the top of the peak is visible (Fig. 10).
Make this peak as sharp as possible by rotating the digipot. It is optimal for the peak to fill
almost the entire y-axis of the graph. See section 4.3.3 for full details.
Click the Auto Set Centre button, and click ‘Yes’ in the following pop-up box. This will set the
centre of the PureFocus850 sensor, which is used to positively verify whether the sample is in
focus.
Check that a peak is visible with each of the other objectives, before returning to the highest
magnification objective.