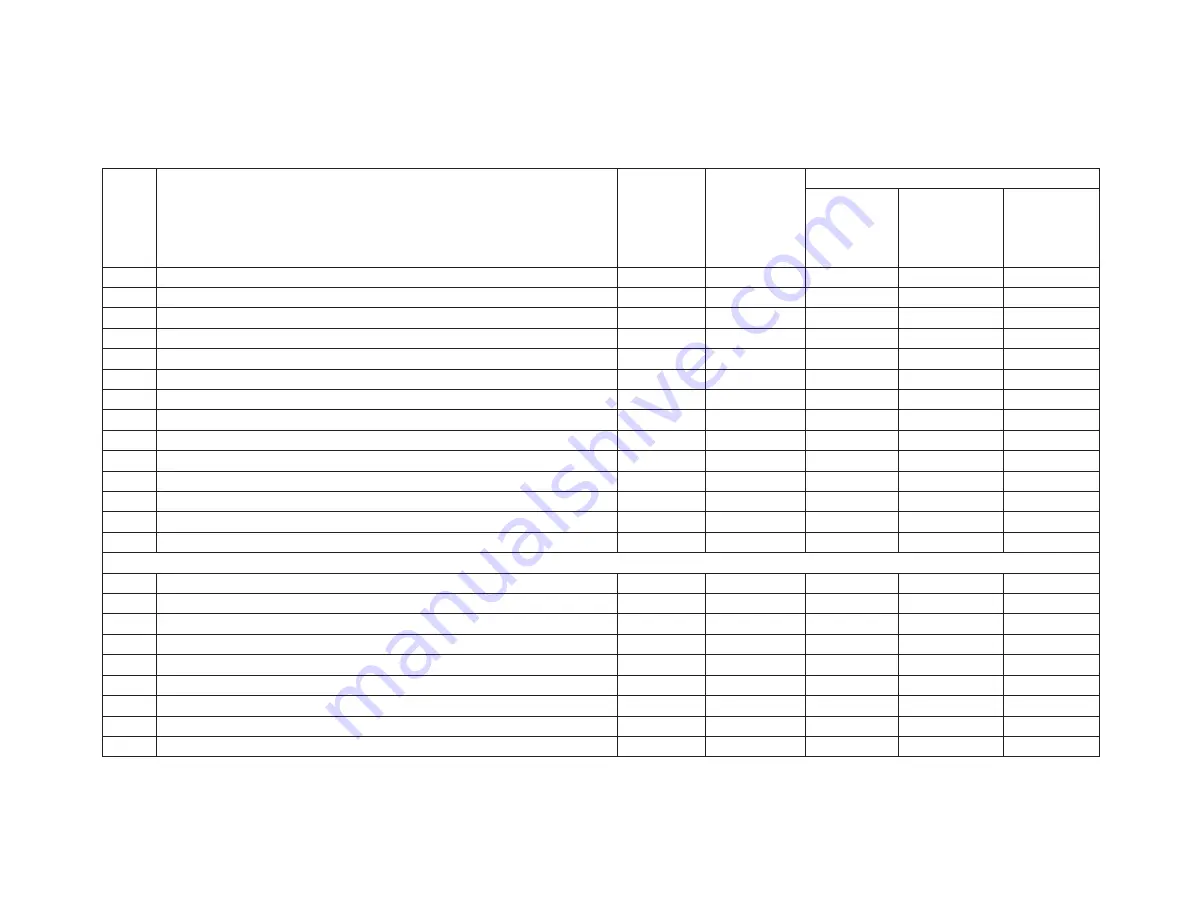
A6. MAINTENANCE
116
8.
ENGINE
First
Service
at
50hrs
Every
Quarter
Additional Every
300hr
Intervals
or Every
Year
500hr
Intervals
or Every
Year
1000hr
Intervals
or Every
2 Year
A.
Hoses and Fittings
CK
CK
B.
Leaks
CK
CK
C.
Mounting Secure
CK
CK
D.
Electrical Connections
CK
CK
E.
Radiator Mounts and Hoses
CK
CK
F.
Alternator V Belt
CK/A
CK/A
CH
G.
Coolant Level and Condition
CK/A
CK/A
CH
H.
Coolant Hoses
CK
CK
CK/CH
I.
Air Filter
CK
CK
CH
J.
Fuel Filter Cartridge
CH
CK
CH
K.
Water Removal From Fuel Filter Cartridge
CK/A
CK/A
L.
Engine Oil
CH
CK/A
CH
M.
Muffler Mount and Condition
CK
CK
N.
Replace Engine Oil Filter Cartridge
CH
CK
CH
9.
TRANSPORT
A.
Chains and Hammer Locks
CK
CK
B.
Chain Anchor Points & Tie Downs (Dump Bed)
CK
CK
C.
Pins and Locks
CK
CK
D.
Lights
CK
CK
E.
Reflective Tape
CK
CK
F.
Mounting Kit
CK
CK
G.
Transport Angle
CK
Summary of Contents for Truck Mounted Forklift
Page 2: ...25 1 16758 7 216...
Page 30: ...A2 INTRODUCTION 22 Safety Decals continued Part Number 517 230 0003...
Page 31: ...A2 INTRODUCTION 23 Safety Decals continued Part Number 517 130 0003...
Page 33: ...A2 INTRODUCTION 25 Safety Decals continued Part Number 517 100 0086 Part Number 517 100 0141...
Page 35: ...A2 INTRODUCTION 27 Safety Decals continued Part N o USA018 Part N o 517 230 0008...
Page 37: ...A2 INTRODUCTION 29 Safety Decals continued Part N umber ENG019 Part N umber 517 999 0254...
Page 41: ...A2 INTRODUCTION 33 Safety Decals continued...
Page 44: ...A2 INTRODUCTION 36 Instruments and Controls continued...
Page 127: ...A6 MAINTENANCE 119 Grease Point Chart continued...
Page 129: ...A6 MAINTENANCE 121 Grease Point Chart continued FEM 2 Fork Carriage Grease Points...
Page 130: ...A6 MAINTENANCE 122 Grease Point Chart continued FEM 3 Fork Carriage Grease Points...
Page 131: ...A6 MAINTENANCE 123 Grease Point Chart continued Chain Rollers Grease Points...
Page 132: ...A6 MAINTENANCE 124 Grease Point Chart continued Mast Section Grease Points...
Page 133: ...A6 MAINTENANCE 125 Grease Point Chart continued Tilt Cylinder Grease Points...
Page 134: ...A6 MAINTENANCE 126 Grease Point Chart continued Side Shift Cylinder Grease Points...
Page 135: ...A6 MAINTENANCE 127 Grease Point Chart continued Mast Carriage Grease Points...
Page 136: ...A6 MAINTENANCE 128 Grease Point Chart continued Side Shift Bushing Grease Points...
Page 137: ...A6 MAINTENANCE 129 Grease Point Chart continued Lift Cylinder Grease Points...
Page 154: ......
Page 160: ...1752 8 7 21 3 172 5 3 6DIHW HFDOV FRQWLQXHG 3DUW 1R...
Page 161: ...1752 8 7 21 3 172 5 3 6DIHW HFDOV FRQWLQXHG...
Page 164: ...1752 8 7 21 3 172 5 3 GUDXOLF HYHUV FRQWLQXHG...
Page 173: ...0 17 1 1 3 172 5 3 UHDVH 3RLQWV FRQWLQXHG...
Page 174: ...0 17 1 1 3 172 5 3 UHDVH 3RLQWV FRQWLQXHG LIW OLQGHU UHDVH 3RLQWV...
Page 175: ...0 17 1 1 3 172 5 3 UHDVH 3RLQWV FRQWLQXHG 0DVW 2XWHU 6HFWLRQ UHDVH 3RLQWV WHP WHP WHP WHP...
Page 176: ...0 17 1 1 3 172 5 3 UHDVH 3RLQWV FRQWLQXHG 0DVW QQHU 6HFWLRQ UHDVH 3RLQWV...
Page 177: ...0 17 1 1 3 172 5 3 UHDVH 3RLQWV FRQWLQXHG 3DQWRJUDSK 0DVW 6HFWLRQ UHDVH 3RLQWV WHP WHP WHP WHP...
Page 178: ...0 17 1 1 3 172 5 3 UHDVH 3RLQWV FRQWLQXHG 3DQWRJUDSK UP 0LGGOH 6HFWLRQ UHDVH 3RLQWV...
Page 179: ...0 17 1 1 3 172 5 3 UHDVH 3RLQWV FRQWLQXHG 3DQWRJUDSK UP 5HDU 6HFWLRQ UHDVH 3RLQWV...
Page 180: ...0 17 1 1 3 172 5 3 UHDVH 3RLQWV FRQWLQXHG 3DQWRJUDSK UP URQW 6HFWLRQ UHDVH 3RLQWV...
Page 181: ...0 17 1 1 3 172 5 3 UHDVH 3RLQWV FRQWLQXHG 3DQWRJUDSK OLQGHU UHDVH 3RLQWV WHP...
Page 182: ......
Page 184: ......
Page 185: ...Machine Model Serial Number Capacity Customer Name Customer Address Date DEALER S STAMP...
Page 190: ...C2 RECORD OF DAMAGE 182 Date Name Brief Details of Damage or Accident Job No Reported to...
Page 192: ...C4 Notes 184...