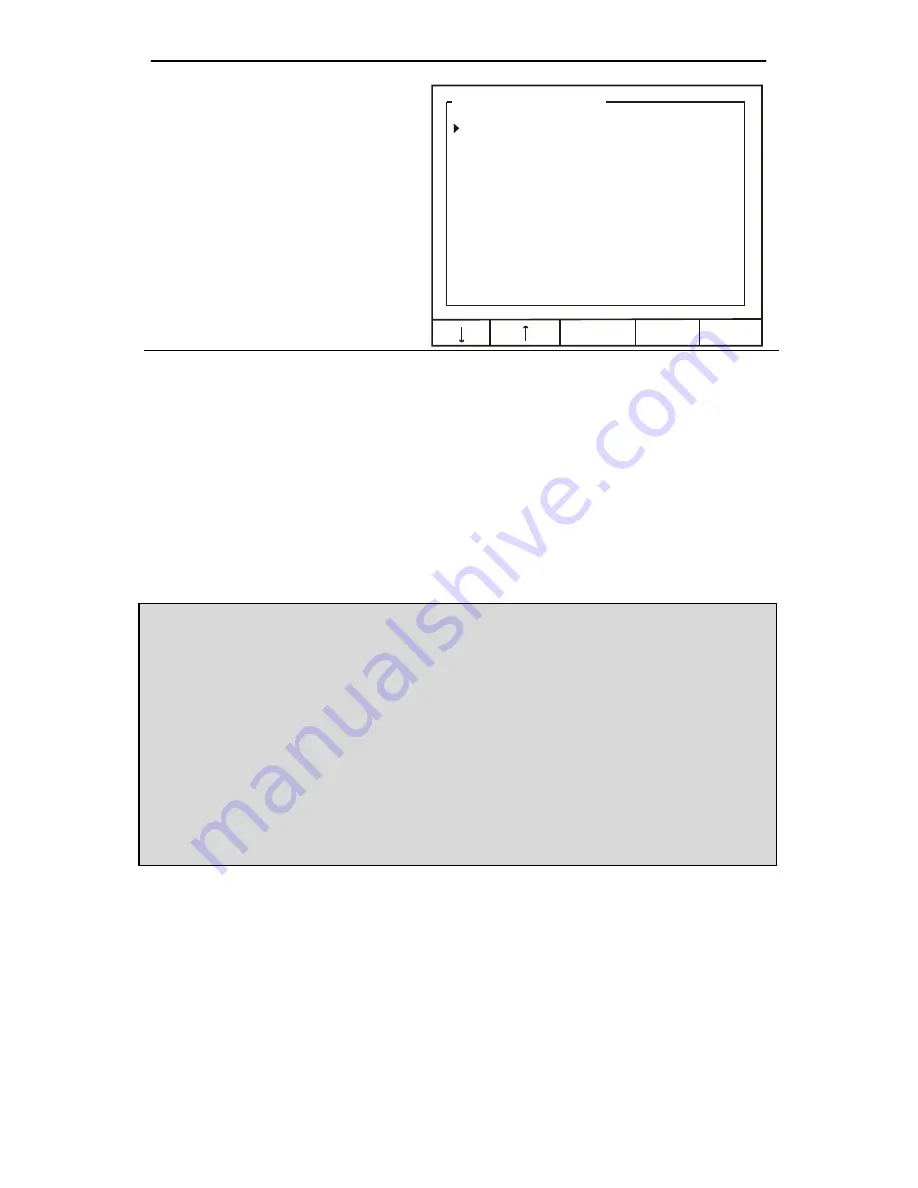
ConsoliDator Multi-Channel Controller
Instruction Manual
37
Lead-Lag Override Function
Lead-Lag mode supports an
override function, which allows up to
five linked relays to turn on if
programmed points are reached.
Override set points also operate in
sequence. They are not assigned to
particular relays.
Use
OVER
key in Lead-Lag menu
to access override menu.
Lead-Lag Override: 1
Over Type: Override 1 & 2 ON
Set Pt. #1: 170.0 GAL
Set Pt. #2: 180.0 GAL
EDIT
EXIT
Over Type
Choose number relays to override main relay (Up to 4 additional
set points for a maximum of 5 relays operating at once.)
Set Pt. #1 (#2, #3, #4)
Specify each process set point for the override relays to
activate.
Example:
[LEAD-LAG: HIGH] is used to link relays #1, #2, and #3. In the Alarm Menu,
High Value
is set at 160.0
GAL and
Low Value
is set at 8.0 GAL. In the Override Menu,
Over Type
is set to [Override 1 & 2 ON.]
Set Pt. #1
is set to 170.0 GAL and
Set Pt. #2
is set to 180.0 GAL.
When the input reaches 160.0 GAL, the first relay in the sequence (Relay #1) turns on. When 170.0 GAL
is reached, the next relay (Relay #2) turns on. If at this point the input decreases and drops below 8.00
GAL, both relays will turn OFF simultaneously. If instead, the input reaches 180.0 GAL, the third relay
will turn ON and all three will remain ON until 8.0 GAL has been reached.
Note: In most override applications the number of relays linked should equal the total number of set
points. However, linking additional relays is allowed. In the example, if 5 relays were linked and the total
set points remained at 3, it would only be possible for 3 of the 5 to be on at once, but all 5 would
sequence.