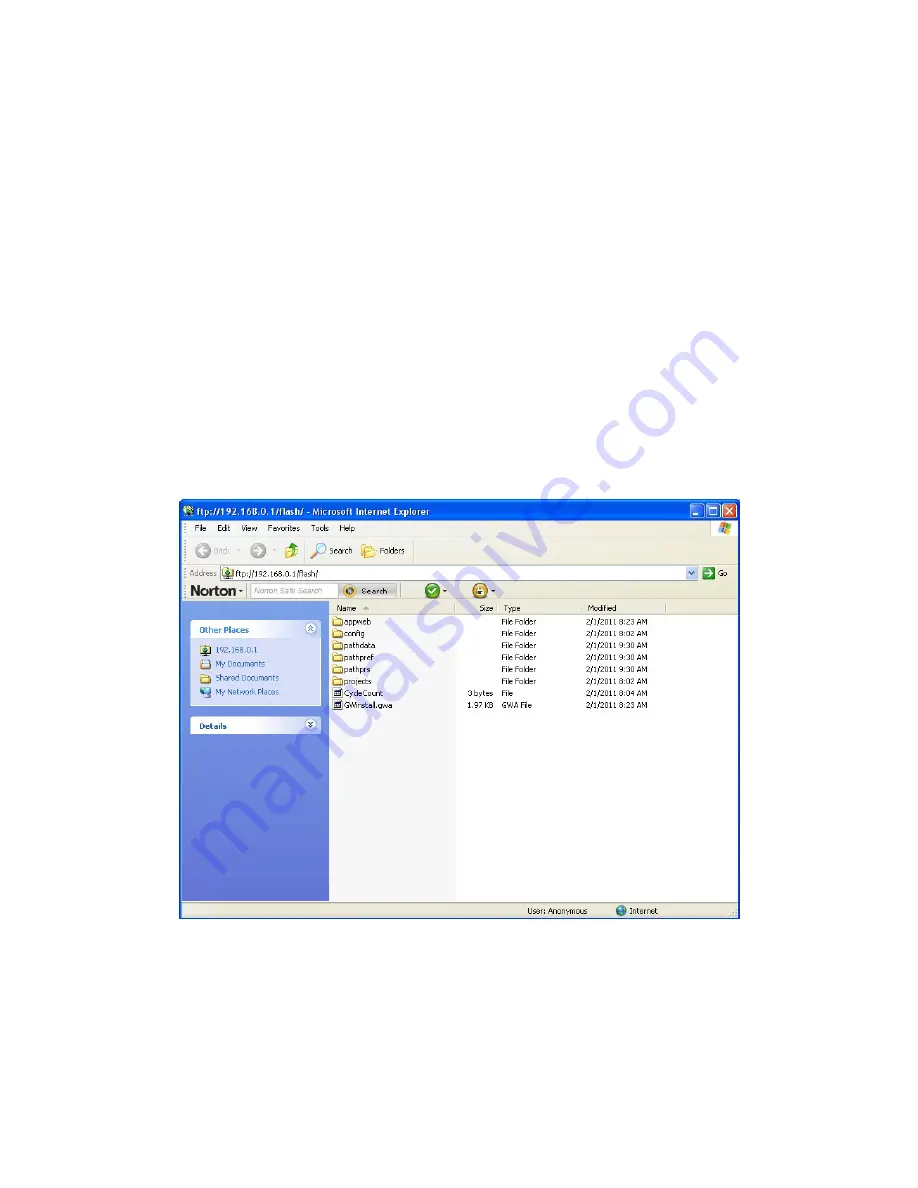
79
If an application is running, the “System Running” panel will display in green. In order to run diagnostics,
you must stop the application from running. Click “Stop Application” and then “Perform Operation”. This
will stop the application from running. You should click the “Disable Power” button to be sure motor
power is off. If you need to load a new project (for example CAL_PP) you will need to click on “Unload”
and then “Perform Operation” before you can load the new project into RAM.
You may now perform the procedures below.
Loading a Project (Program) or Updating PAC Files
If CAL_PP or a different program needs to be loaded into the controller from an external computer, this
may be done using the Web Interface.
1. In the Web Based Operator Interface, select “Utilities/Backup and Restore
2. Click on Start File Manager. It may be necessary to hold down the Control Key to allow the pop-
up. An ftp directory pop-up will come up. In the “Page” menu in Windows Internet Explorer select
“Open ftp site in Windows Explorer”. Another window will open showing several folders, including
“Config” and “Projects”.
3. To load a Project, Open the “Projects” folder and paste the Project folder into this area. There
may be several other projects (programs) loaded into this folder, which is stored in flash ram in
the controller. A project folder is a software folder than may have several files inside it. You must
load the entire folder, not just the files inside.
4. To load or update PAC files, open the “Config” folder and paste a backup copy of the PAC files
into the “Config” folder. These files will all have a
.pac
extension. The robot must be re-booted
after new PAC files are installed for them to take effect.
Summary of Contents for PF3400
Page 8: ......
Page 32: ...PreciseFlex_Robot 24 Appendix B TUV Verification of PF400 Collision Forces...
Page 33: ...Introduction to the Hardware 25...
Page 34: ...PreciseFlex_Robot 26...
Page 35: ...Introduction to the Hardware 27...
Page 37: ...Introduction to the Hardware 29 Appendix C Table A2 from ISO TS 15066 2016...
Page 38: ...PreciseFlex_Robot 30 Table A2 Continued...
Page 41: ...Introduction to the Hardware 33 PF400 500gm Safety Circuits PF3400 3kg Safety Circuits...
Page 45: ...Installation Information 37...
Page 46: ...PreciseFlex_Robot 38...
Page 47: ...Installation Information 39...
Page 48: ...PreciseFlex_Robot 40...
Page 54: ...PreciseFlex_Robot 46 Schematic System Overview...
Page 55: ...Hardware Reference 47 Schematic FFC Boards Revision B PF400...
Page 56: ...PreciseFlex_Robot 48...
Page 57: ...Hardware Reference 49 Schematic FFC Boards Revision C PF400...
Page 58: ...PreciseFlex_Robot 50 Schematic FFC Boards 3kg PF400...
Page 59: ...Hardware Reference 51...
Page 60: ...PreciseFlex_Robot 52 Schematic Safety System Overview PF400 CAT3...
Page 61: ...Hardware Reference 53...
Page 62: ...PreciseFlex_Robot 54 Controller Power Amplifier Connectors Control Board Connectors...
Page 63: ...Hardware Reference 55 Gripper and Linear Axis Controller Connectors...
Page 64: ...PreciseFlex_Robot 56...
Page 65: ...Hardware Reference 57...
Page 66: ...PreciseFlex_Robot 58 Schematic Slip Ring for 60N Gripper...
Page 67: ...Hardware Reference 59...
Page 68: ...PreciseFlex_Robot 60...
Page 69: ...Hardware Reference 61...
Page 70: ...PreciseFlex_Robot 62...
Page 71: ...Hardware Reference 63...
Page 72: ...PreciseFlex_Robot 64...
Page 73: ...Hardware Reference 65 Motor 60N Gripper...
Page 74: ...PreciseFlex_Robot 66...
Page 106: ...PreciseFlex_Robot 98 b The CALPP application takes about 1 minute to run...
Page 124: ...PreciseFlex_Robot 116 Wiring for 60N Gripper with Battery Pigtail Wiring for Pneumatic Gripper...
Page 125: ...117 Wiring for Vacuum Gripper Wiring for Vacuum Pallet Gripper...