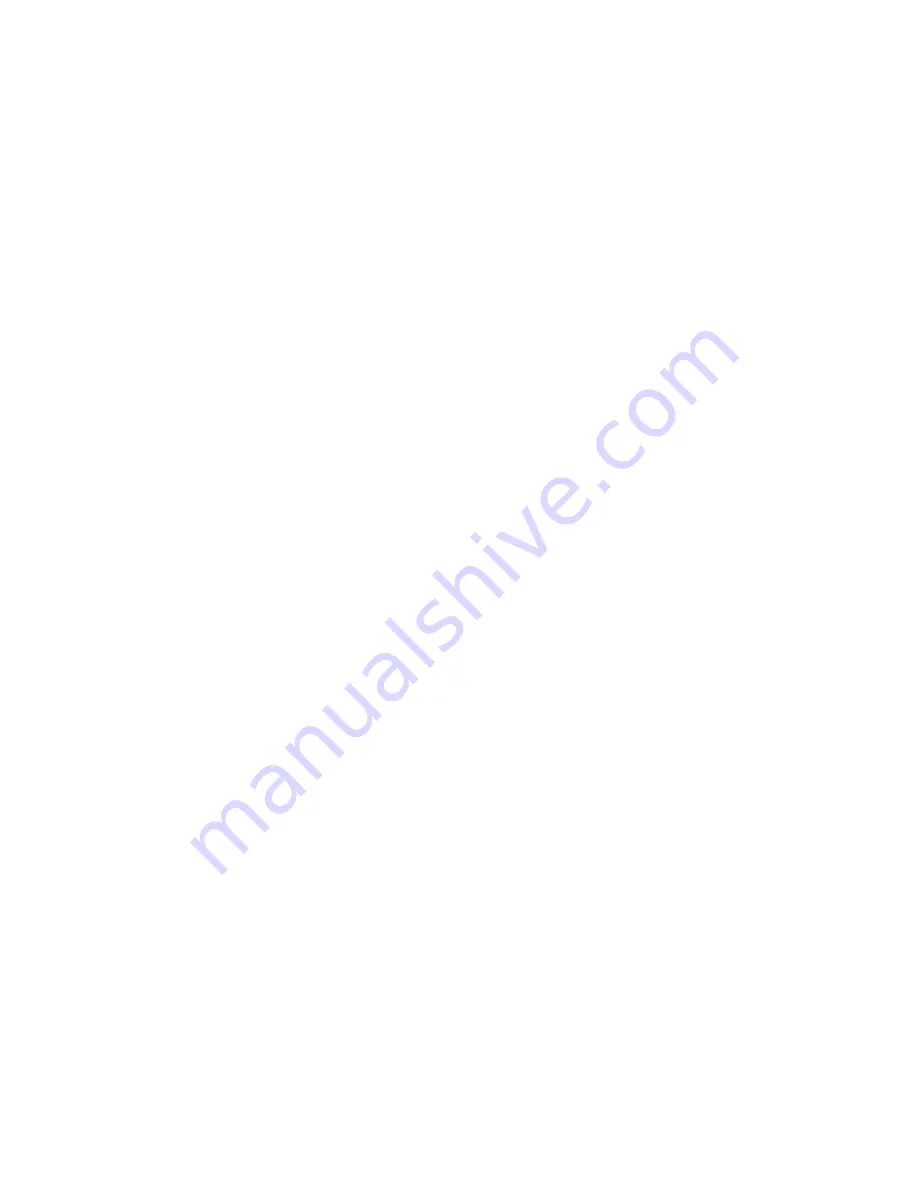
PreciseFlex_Robot
2
two significant upgrades have been released.
Revision B
, designated by Serial Numbers F0B-wwww-xy-zzzzz, was released in 2014, and improved
the high-speed, continuous duty performance of the robot. The main changes in this revision were a
wider timing belt in J2 (12mm replaced 9mm), changing to all steel drive pulleys from aluminum to
improve the bond strength of the drive pulleys to the motor shaft, and changing the slip ring in the wrist for
improved reliability.
Revision C
, designated by Serial Numbers F0C-wwww-xy-zzzzz, was released in the fall of 2016, and
improved the resistance of the robot to high-speed crashes by adding clamp rings and beveled retaining
rings to the J2, J3, and J4 bearings, so that these bearings cannot come loose in a high-speed crash. In
addition, improved support for pneumatic grippers and control of solenoid valves in the outer link is
provided, and some longer life cam followers for the J2 timing belt are installed. In January 2017, a
longer life Ethernet cable is expected to be released which should last for the life of the robot running
continuous duty for at least 3 years.
PF3400: 3kg Version
In 2017 a heavier payload version of the PF400 was released. This version, which appears very similar
to the standard versions, is designated by Serial Numbers FO2, and has a rated payload of 3kg grams
without a gripper. In this version, the torque for J1 remains the same, however the torque for J2 is
increased 100%, and the torques for J3 and J4 are both increased 65%. J2 and J4 have larger motors
and J2 has a 20mm wide timing belt versus 12mm wide to handle the increased torque. The Z linear
bearing width has been increased from 24mm to 42mm to support the heavier payload. These units have
the same top speeds as the standard versions. However, with the full 3kg payloads, the accelerations
are somewhat slower than the standard version with the servo gripper and 500 gram payload. If these
units are used with payloads less than 3kg, accelerations greater than 100% may be commanded to
increase the accelerations to values equal or greater than the standard version robot. The 3kg payload
includes the gripper. For example, the optional 60N Electric Gripper weighs 1kg, so with this gripper the
workpiece payload is 2kg.
Note that for the PF3400 3kg version, it is very important to set the correct value for the payload in the
Dynamic Feed Forward parameter 16071 (or use the GPL “Robot.Payload” property). 100% equals 3kg
for the gripper and payload mass. For lighter masses, this value should be reduced. Setting the payload
correctly is important both for optimal dynamic performance of the robot and also for proper gravity
compensation, including “free” mode. Also, it is important to set the correct offset distance in value 5 of
parameter 16068, in mm, for the distance of the center of mass of the gripper and payload from the J4
axis of rotation. For example, if the center of a 2kg mass is 100mm from the center of rotation of axis 4
(the wrist), this value should be set to 100mm, for the Dynamic Feed Forward calculations to compute the
correct feed forward motor torques and achieve optimal performance. For pick and place applications,
the property “robot.payload” can be written by the application program to change the payload. Note that
when setting the payload and gripper payload offset parameters in the database, these values must be
entered, saved to flash, and the controller must be re-booted for them to take effect.
In addition, the 3kg version has 8 inputs and 8 outputs available at the base connector panel in a 25 pin
Dsubminiature connector and has 4 digital outputs and up to 4 digital inputs available in the outer link
when the pneumatic version is ordered.
The 3kg version is nominally quoted and shipped with a standard ISO flange, and a single solenoid valve
mounted in the outer link for users to add pneumatic or vacuum grippers of their design. Optionally, an
additional solenoid can be ordered, or a 60N squeeze, 40mm travel electric gripper can be ordered, or a
dual 23N squeeze, 60mm electric gripper can be ordered. See the “system dimensions” section for
reference dimensions on these options.
Summary of Contents for PF3400
Page 8: ......
Page 32: ...PreciseFlex_Robot 24 Appendix B TUV Verification of PF400 Collision Forces...
Page 33: ...Introduction to the Hardware 25...
Page 34: ...PreciseFlex_Robot 26...
Page 35: ...Introduction to the Hardware 27...
Page 37: ...Introduction to the Hardware 29 Appendix C Table A2 from ISO TS 15066 2016...
Page 38: ...PreciseFlex_Robot 30 Table A2 Continued...
Page 41: ...Introduction to the Hardware 33 PF400 500gm Safety Circuits PF3400 3kg Safety Circuits...
Page 45: ...Installation Information 37...
Page 46: ...PreciseFlex_Robot 38...
Page 47: ...Installation Information 39...
Page 48: ...PreciseFlex_Robot 40...
Page 54: ...PreciseFlex_Robot 46 Schematic System Overview...
Page 55: ...Hardware Reference 47 Schematic FFC Boards Revision B PF400...
Page 56: ...PreciseFlex_Robot 48...
Page 57: ...Hardware Reference 49 Schematic FFC Boards Revision C PF400...
Page 58: ...PreciseFlex_Robot 50 Schematic FFC Boards 3kg PF400...
Page 59: ...Hardware Reference 51...
Page 60: ...PreciseFlex_Robot 52 Schematic Safety System Overview PF400 CAT3...
Page 61: ...Hardware Reference 53...
Page 62: ...PreciseFlex_Robot 54 Controller Power Amplifier Connectors Control Board Connectors...
Page 63: ...Hardware Reference 55 Gripper and Linear Axis Controller Connectors...
Page 64: ...PreciseFlex_Robot 56...
Page 65: ...Hardware Reference 57...
Page 66: ...PreciseFlex_Robot 58 Schematic Slip Ring for 60N Gripper...
Page 67: ...Hardware Reference 59...
Page 68: ...PreciseFlex_Robot 60...
Page 69: ...Hardware Reference 61...
Page 70: ...PreciseFlex_Robot 62...
Page 71: ...Hardware Reference 63...
Page 72: ...PreciseFlex_Robot 64...
Page 73: ...Hardware Reference 65 Motor 60N Gripper...
Page 74: ...PreciseFlex_Robot 66...
Page 106: ...PreciseFlex_Robot 98 b The CALPP application takes about 1 minute to run...
Page 124: ...PreciseFlex_Robot 116 Wiring for 60N Gripper with Battery Pigtail Wiring for Pneumatic Gripper...
Page 125: ...117 Wiring for Vacuum Gripper Wiring for Vacuum Pallet Gripper...