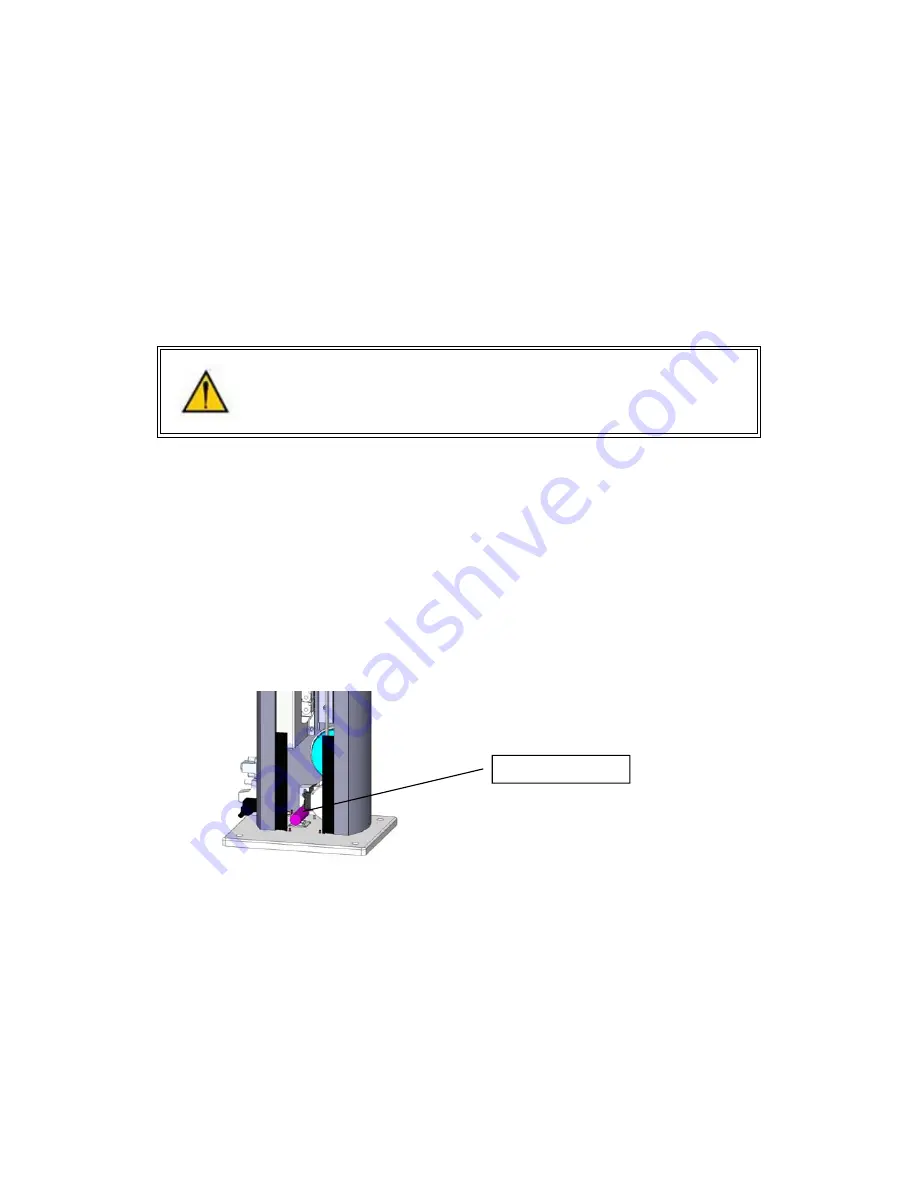
PreciseFlex_Robot
94
Calibrating the Robot), or another known position, and check the joint angles in the Virtual
Pendant in the Web Operator Interface. The joint angles in the Calibration Position are:
Z Axis: -1mm (-2mm for Beta robots)
J2 or Shoulder: -90
J3 or Elbow: 179.99
J4 or Wrist: -180
If the robot joints after this procedure followed by homing are different from the above, then the
robot needs to be re-calibrated. See procedure below.
Replacing the Encoder Battery
DANGER:
Before replacing the encoder battery, the AC power should be
disconnected. Removing the front cover allows access to the AC power
terminals.
The Encoder Battery is designed to last for several years with robot power turned off. With robot power
turned on, there is no drain on the battery. The battery voltage is monitored by the system. The nominal
battery voltage is 3.6 volts. If the battery voltage drops to 3.3 volts an error message “Encoder Battery
Low” is generated. At this level the absolute encoder backup function will still work, however the Battery
should be replaced. If the voltage drops to 2.5 volts, an error message “Absolute Encoder Down” is
generated. At this point, the absolute encoder backup function will not work.
Note that if any motor/encoder is disconnected from the encoder battery by disconnecting the encoder
cable, the “Encoder Battery Low” or Encoder Battery Down” message will be generated. However in this
case the encoder battery does not need to be replaced. It is only necessary to re-calibrate the robot, see
below.
Tools Required:
1. 3.0mm hex driver or hex L wrench
Parts Required:
1. New Encoder Battery PN PF00-EA-00002
2. 6 in long by .125 wide tie wrap
Encoder Battery
Summary of Contents for PF3400
Page 8: ......
Page 32: ...PreciseFlex_Robot 24 Appendix B TUV Verification of PF400 Collision Forces...
Page 33: ...Introduction to the Hardware 25...
Page 34: ...PreciseFlex_Robot 26...
Page 35: ...Introduction to the Hardware 27...
Page 37: ...Introduction to the Hardware 29 Appendix C Table A2 from ISO TS 15066 2016...
Page 38: ...PreciseFlex_Robot 30 Table A2 Continued...
Page 41: ...Introduction to the Hardware 33 PF400 500gm Safety Circuits PF3400 3kg Safety Circuits...
Page 45: ...Installation Information 37...
Page 46: ...PreciseFlex_Robot 38...
Page 47: ...Installation Information 39...
Page 48: ...PreciseFlex_Robot 40...
Page 54: ...PreciseFlex_Robot 46 Schematic System Overview...
Page 55: ...Hardware Reference 47 Schematic FFC Boards Revision B PF400...
Page 56: ...PreciseFlex_Robot 48...
Page 57: ...Hardware Reference 49 Schematic FFC Boards Revision C PF400...
Page 58: ...PreciseFlex_Robot 50 Schematic FFC Boards 3kg PF400...
Page 59: ...Hardware Reference 51...
Page 60: ...PreciseFlex_Robot 52 Schematic Safety System Overview PF400 CAT3...
Page 61: ...Hardware Reference 53...
Page 62: ...PreciseFlex_Robot 54 Controller Power Amplifier Connectors Control Board Connectors...
Page 63: ...Hardware Reference 55 Gripper and Linear Axis Controller Connectors...
Page 64: ...PreciseFlex_Robot 56...
Page 65: ...Hardware Reference 57...
Page 66: ...PreciseFlex_Robot 58 Schematic Slip Ring for 60N Gripper...
Page 67: ...Hardware Reference 59...
Page 68: ...PreciseFlex_Robot 60...
Page 69: ...Hardware Reference 61...
Page 70: ...PreciseFlex_Robot 62...
Page 71: ...Hardware Reference 63...
Page 72: ...PreciseFlex_Robot 64...
Page 73: ...Hardware Reference 65 Motor 60N Gripper...
Page 74: ...PreciseFlex_Robot 66...
Page 106: ...PreciseFlex_Robot 98 b The CALPP application takes about 1 minute to run...
Page 124: ...PreciseFlex_Robot 116 Wiring for 60N Gripper with Battery Pigtail Wiring for Pneumatic Gripper...
Page 125: ...117 Wiring for Vacuum Gripper Wiring for Vacuum Pallet Gripper...