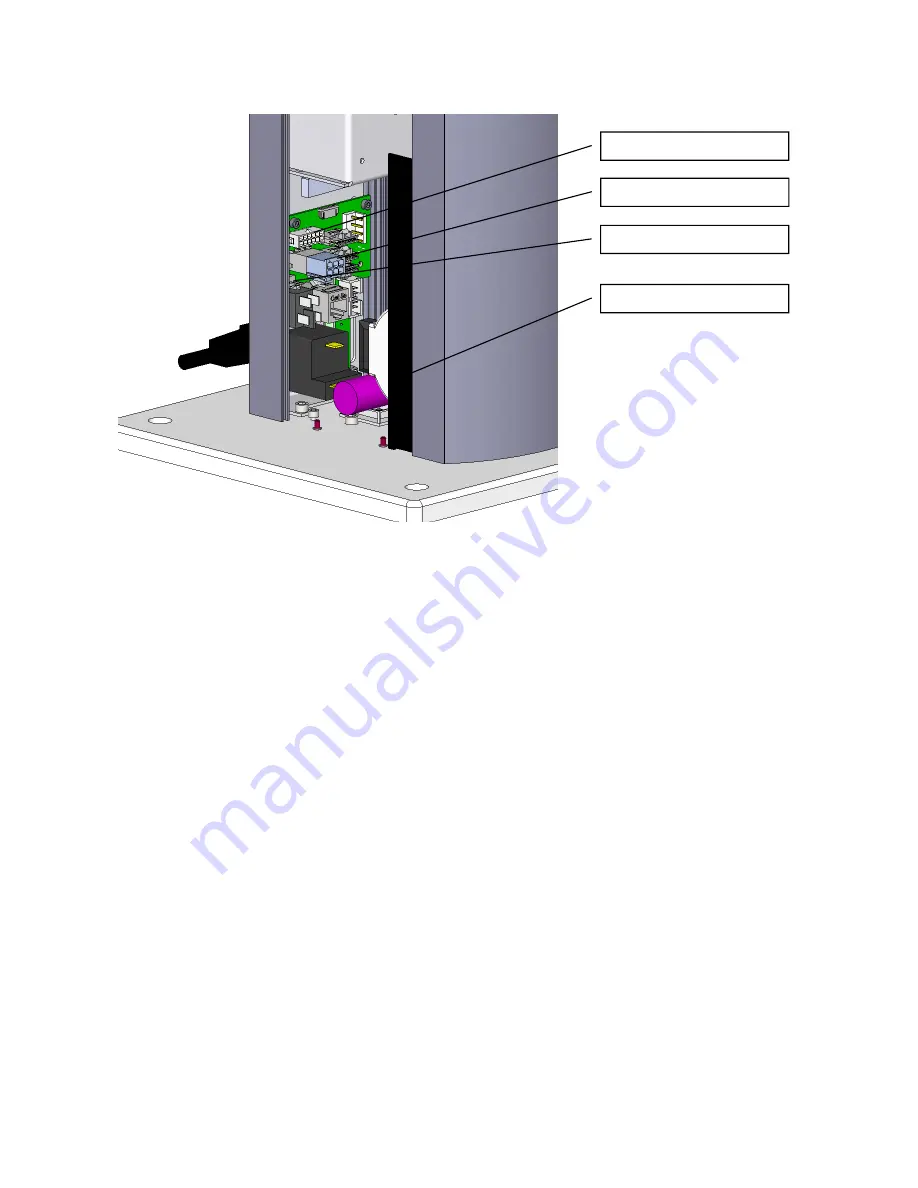
111
11. Remove the J1 motor and encoder connectors that plug into the J1 Motor Interface Board.
12. Remove the Battery connector that plugs into the J1 Motor Interface Board.
13. Loosen the M4 SHCS screws attaching the Z bearing rail to the Z Extrusion.
14. Slide the Z Rail and Z Carriage with the robot arm still attached partially out the top of the robot,
far enough to expose the power supplies. It may be more convenient to slide the carriage and Z
rail all the way out of the Z extrusion. Take care the bearing block does not slide off the Z rail. It
may be helpful to wrap some tape around the rail to prevent this. If the bearing block slides off
the rail, the bearing balls may be lost, damaging the bearing. Simultaneously slide the Electronic
Chassis out of the Z Extrusion and lay both assemblies on the table.
15. Unplug the cables from the failed power supply.
16. Remove the 4 M3 X 8 SHCS and lock washers to replace the power supply or energy dump PCA.
Be careful not to pull the J1 FFC encoder cable (white 14mm wide flat cable) out of the FFC
connector on the J1 Motor Interface PCA. If this cable is pulled out, you must carefully release
the clamping lid on the FFC cable connector on the J1 Motor Interface PCA by inserting a small
flat bladed screwdriver in the notch in the clamping lid and VERY gently prying the lid out of the
connector. This lid is a cam-lock type of lid, which when inserted, clamps the flat white J1
encoder ribbon cable. Re-insert the J1 flat white encoder ribbon cable into this connector and
carefully press the clamping lid back into the connector. If the J1 encoder cable is disconnected
during this procedure, it will be necessary to re-calibrate the robot as the absolute encoder
backup power will be interrupted to the J1 absolute encoder.
17. Re-attach the power supply cables and re-assemble the robot. Be sure the bearing rail reference
edge is tightly pressed against the reference boss in the Z extrusion. The top of the bearing rail
should be about 35mm below the top of the extrusion and the bottom of the rail should clear the
stage one Z timing belt on the large diameter pulley.
18. Recalibrate the robot.
J1 Encoder Connector
J1 Motor Connector
Battery Connector
Splash Guard
Summary of Contents for PF3400
Page 8: ......
Page 32: ...PreciseFlex_Robot 24 Appendix B TUV Verification of PF400 Collision Forces...
Page 33: ...Introduction to the Hardware 25...
Page 34: ...PreciseFlex_Robot 26...
Page 35: ...Introduction to the Hardware 27...
Page 37: ...Introduction to the Hardware 29 Appendix C Table A2 from ISO TS 15066 2016...
Page 38: ...PreciseFlex_Robot 30 Table A2 Continued...
Page 41: ...Introduction to the Hardware 33 PF400 500gm Safety Circuits PF3400 3kg Safety Circuits...
Page 45: ...Installation Information 37...
Page 46: ...PreciseFlex_Robot 38...
Page 47: ...Installation Information 39...
Page 48: ...PreciseFlex_Robot 40...
Page 54: ...PreciseFlex_Robot 46 Schematic System Overview...
Page 55: ...Hardware Reference 47 Schematic FFC Boards Revision B PF400...
Page 56: ...PreciseFlex_Robot 48...
Page 57: ...Hardware Reference 49 Schematic FFC Boards Revision C PF400...
Page 58: ...PreciseFlex_Robot 50 Schematic FFC Boards 3kg PF400...
Page 59: ...Hardware Reference 51...
Page 60: ...PreciseFlex_Robot 52 Schematic Safety System Overview PF400 CAT3...
Page 61: ...Hardware Reference 53...
Page 62: ...PreciseFlex_Robot 54 Controller Power Amplifier Connectors Control Board Connectors...
Page 63: ...Hardware Reference 55 Gripper and Linear Axis Controller Connectors...
Page 64: ...PreciseFlex_Robot 56...
Page 65: ...Hardware Reference 57...
Page 66: ...PreciseFlex_Robot 58 Schematic Slip Ring for 60N Gripper...
Page 67: ...Hardware Reference 59...
Page 68: ...PreciseFlex_Robot 60...
Page 69: ...Hardware Reference 61...
Page 70: ...PreciseFlex_Robot 62...
Page 71: ...Hardware Reference 63...
Page 72: ...PreciseFlex_Robot 64...
Page 73: ...Hardware Reference 65 Motor 60N Gripper...
Page 74: ...PreciseFlex_Robot 66...
Page 106: ...PreciseFlex_Robot 98 b The CALPP application takes about 1 minute to run...
Page 124: ...PreciseFlex_Robot 116 Wiring for 60N Gripper with Battery Pigtail Wiring for Pneumatic Gripper...
Page 125: ...117 Wiring for Vacuum Gripper Wiring for Vacuum Pallet Gripper...