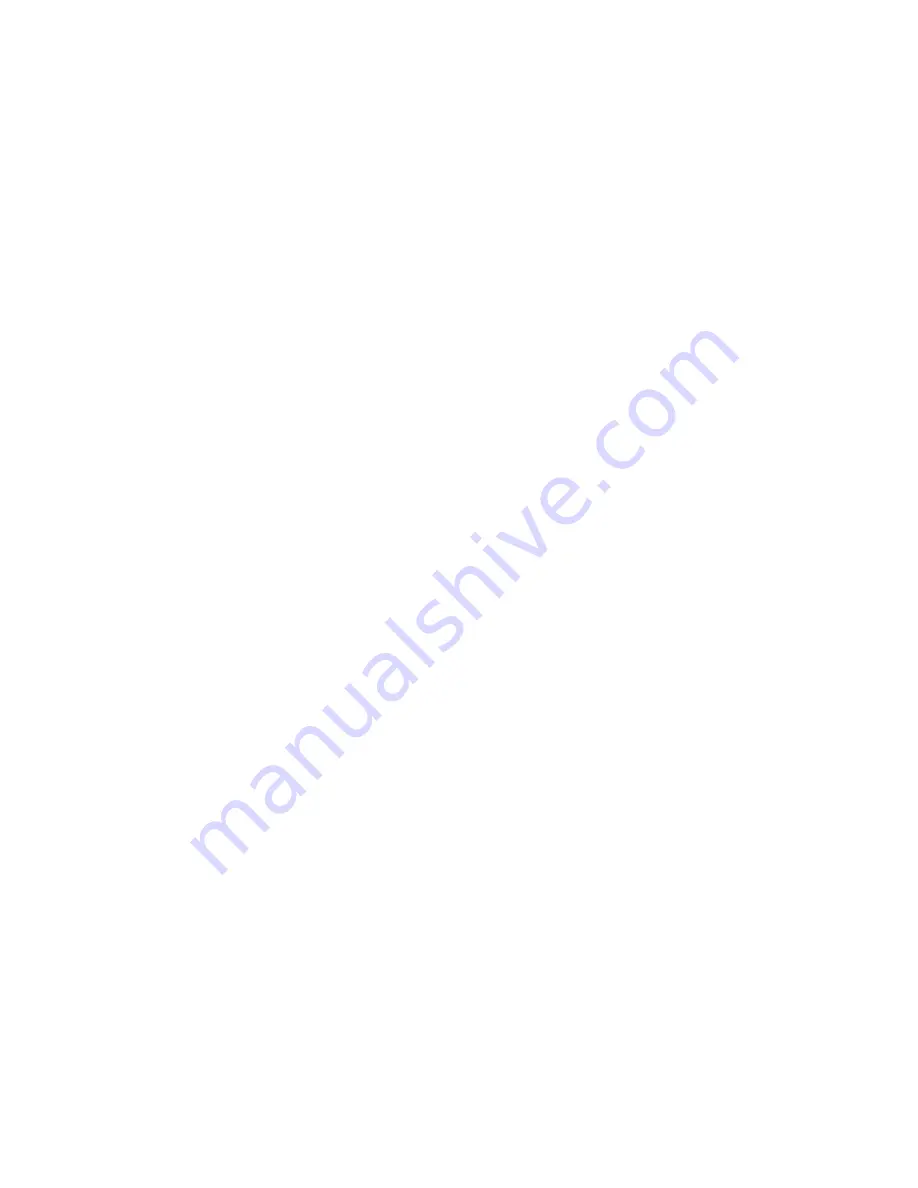
Introduction to the Hardware
13
Collaborative Robot Safety
Summary.
The PF400 and PF3400 robots have been designed to be safe for collaborative use by means of inherent
design and control when evaluated under ISO/TS 15066 “Robots and Robotic Devices – Collaborative
Robots” released February 15, 2016. In all free space collisions (transient contact), up to its maximum
speed and payload, these robots do not exceed the forces in the standard. In all horizontal rigid surface
collisions PF400 does not exceed the forces (quasi-static) in the standard. The PF3400 can exceed the
maximum recommended force in the horizontal plane if J2 is driven at maximum velocity so that the tool
crashes into a rigid surface. For vertical downward collisions into a rigid surface these robots do exceed
the forces (quasi-static) at higher speeds. Horizontal and vertical motions at 100% speed may be
programmed as long as an approach point is specified at least 50mm above any rigid surfaces with a final
motion at a speed of 60% or less. Collision testing has been performed and certified by TUV and a table
of collision speeds and forces is provided in Appendix B of this section.
The PF robot is available in two versions: the PF400 500gm payload version and the PF3400 3kg
payload version. Both of these robots have extensive safety features as listed in Appendix D of this
section. The 3kg payload version has some additional hardware safety circuitry, including full dual Estop
circuitry and a circuit to turn off the 48V motor power supply in addition to the standard amplifier disable
circuitry in the 500gm version and meets Performance Level d, CAT3*. (* There is one exception to the
CAT3 specification: in the PF3400 it is possible for the computer to re-enable motor power under certain
conditions after a crash. This allows auto-recovery and continued motion if the application programmer
wishes to include this capability.)
All controller failures for both versions which might result in an uncontrolled motion have been listed and
tested under supervision by TUV. None of these failures can result in an uncontrolled motion. For the
500gm payload version of the PF400 a single, PLd, EStop circuit is provided. However, this robot can
also be stopped safely by hand, providing a redundant means of stopping. For the PF3400, a safety/IO
board in the base of the robot provides two redundant Estop circuits compliant with CAT 3.
Background.
Recently there has been increased interest in humans and articulated machines working in the same
workspace in a safe manner. Safety standards are being updated based on a wider variety of application
conditions and taking into consideration that many articulated manipulators are now low payload devices
with limited power. The current safety standard used by most organizations for evaluating the safety of
“Industrial” robots is EN ISO 10218-1:2011 and 10218-2:2011. These standards have recently been
augmented in 2016 by ISO/TS 15066 “Robots and Robotic Devices – Collaborative Robots”.
“Collaborative Operation” is defined in section 3.4 of 10218:1:2011 as “a state in which purposely
designed robots work in direct cooperation with a human within a defined workspace”.
One of the requirements listed as sufficient to meet the 10218:1:2011 standard is:
Summary of Contents for PF3400
Page 8: ......
Page 32: ...PreciseFlex_Robot 24 Appendix B TUV Verification of PF400 Collision Forces...
Page 33: ...Introduction to the Hardware 25...
Page 34: ...PreciseFlex_Robot 26...
Page 35: ...Introduction to the Hardware 27...
Page 37: ...Introduction to the Hardware 29 Appendix C Table A2 from ISO TS 15066 2016...
Page 38: ...PreciseFlex_Robot 30 Table A2 Continued...
Page 41: ...Introduction to the Hardware 33 PF400 500gm Safety Circuits PF3400 3kg Safety Circuits...
Page 45: ...Installation Information 37...
Page 46: ...PreciseFlex_Robot 38...
Page 47: ...Installation Information 39...
Page 48: ...PreciseFlex_Robot 40...
Page 54: ...PreciseFlex_Robot 46 Schematic System Overview...
Page 55: ...Hardware Reference 47 Schematic FFC Boards Revision B PF400...
Page 56: ...PreciseFlex_Robot 48...
Page 57: ...Hardware Reference 49 Schematic FFC Boards Revision C PF400...
Page 58: ...PreciseFlex_Robot 50 Schematic FFC Boards 3kg PF400...
Page 59: ...Hardware Reference 51...
Page 60: ...PreciseFlex_Robot 52 Schematic Safety System Overview PF400 CAT3...
Page 61: ...Hardware Reference 53...
Page 62: ...PreciseFlex_Robot 54 Controller Power Amplifier Connectors Control Board Connectors...
Page 63: ...Hardware Reference 55 Gripper and Linear Axis Controller Connectors...
Page 64: ...PreciseFlex_Robot 56...
Page 65: ...Hardware Reference 57...
Page 66: ...PreciseFlex_Robot 58 Schematic Slip Ring for 60N Gripper...
Page 67: ...Hardware Reference 59...
Page 68: ...PreciseFlex_Robot 60...
Page 69: ...Hardware Reference 61...
Page 70: ...PreciseFlex_Robot 62...
Page 71: ...Hardware Reference 63...
Page 72: ...PreciseFlex_Robot 64...
Page 73: ...Hardware Reference 65 Motor 60N Gripper...
Page 74: ...PreciseFlex_Robot 66...
Page 106: ...PreciseFlex_Robot 98 b The CALPP application takes about 1 minute to run...
Page 124: ...PreciseFlex_Robot 116 Wiring for 60N Gripper with Battery Pigtail Wiring for Pneumatic Gripper...
Page 125: ...117 Wiring for Vacuum Gripper Wiring for Vacuum Pallet Gripper...