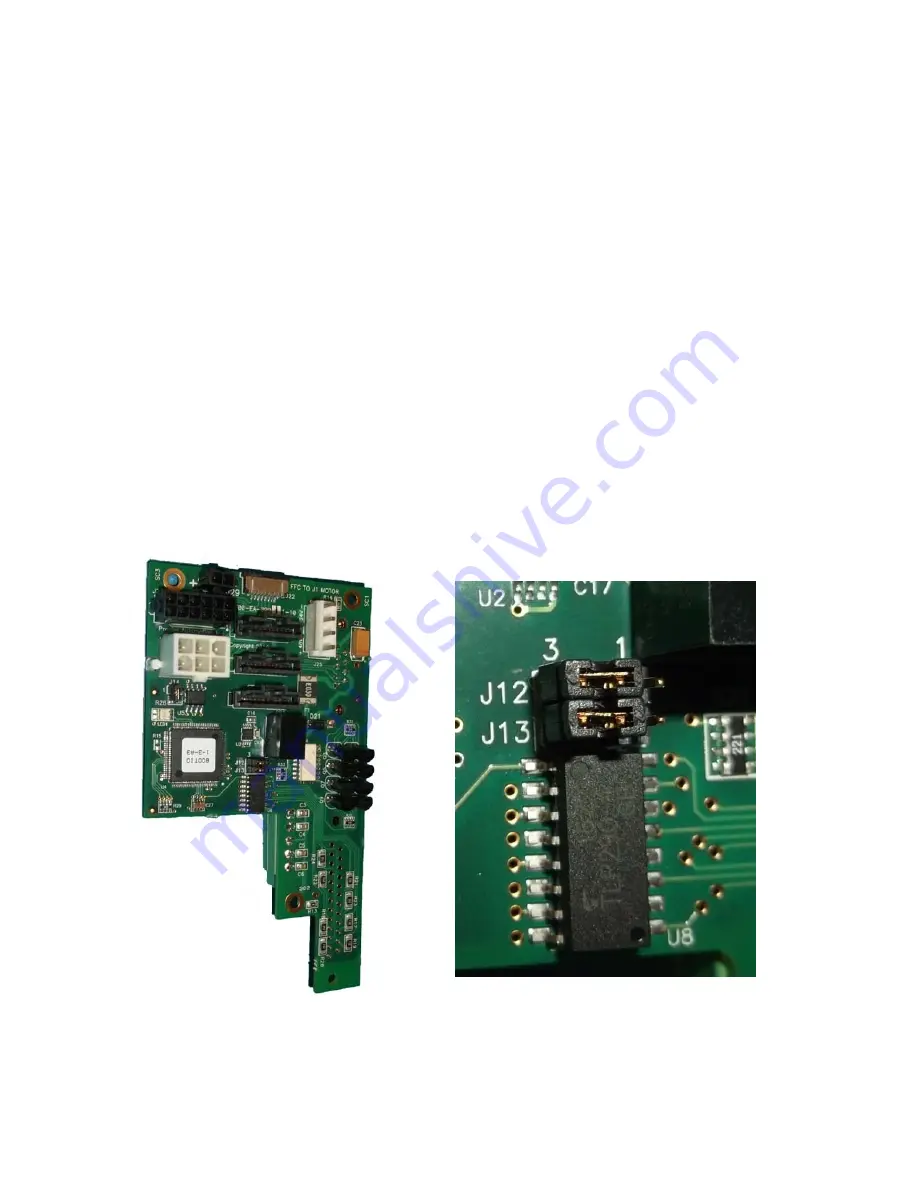
Hardware Reference
73
The RS485 Remote IO Module (GIO) provides 12 general purpose optically isolated digital input signals
and 8 general purpose optically isolated digital output signals. Two inputs, 11 and 12, can be optionally
configured as analog inputs by means of jumpers J1 and J2. Connecting J1 to pins 1 and 2 (default)
configures these inputs as digital and connecting pins 2 and 3 configures them as analog (if the analog
option has been ordered). These input and output signals are intended for interfacing to tooling and
sensors or for general application needs. This board is connected to the controller by an RS485 serial line
that allows the controller to scan the GIO I/O with a nominal period of 4 milliseconds.
The DIO signals are accessible via the DB25 female connector that is mounted on the facilities panel
when this option is ordered. The DIO signals addresses are determined by a base address set by a DIP
switch on the DIO board. For the PF400 robot without the linear axis option the DIO option is located at
the robot connector panel and for both this location and also for the location at the end of the optional
linear axis, all the address jumpers will NOT be installed, which sets the address of this module to “8”.
This address avoids conflicts with other RS485 network controllers for the gripper and optional linear axis.
See “Installing the optional G IO Board” under Service Procedures for details on installing this module.
PF3400 3kg IO in Base of Robot (GIO)
For the 3kg PF400, the GIO function is integrated as a standard feature in the base of the robot, however
only inputs 1-8 are supported. All outputs are sourcing and cannot be changed. Inputs are set to sinking
in the factory and can be changed in blocks of 4 by moving J12 and J13 to connect pins 1 and 2, instead
of 2 and 3.
Summary of Contents for PF3400
Page 8: ......
Page 32: ...PreciseFlex_Robot 24 Appendix B TUV Verification of PF400 Collision Forces...
Page 33: ...Introduction to the Hardware 25...
Page 34: ...PreciseFlex_Robot 26...
Page 35: ...Introduction to the Hardware 27...
Page 37: ...Introduction to the Hardware 29 Appendix C Table A2 from ISO TS 15066 2016...
Page 38: ...PreciseFlex_Robot 30 Table A2 Continued...
Page 41: ...Introduction to the Hardware 33 PF400 500gm Safety Circuits PF3400 3kg Safety Circuits...
Page 45: ...Installation Information 37...
Page 46: ...PreciseFlex_Robot 38...
Page 47: ...Installation Information 39...
Page 48: ...PreciseFlex_Robot 40...
Page 54: ...PreciseFlex_Robot 46 Schematic System Overview...
Page 55: ...Hardware Reference 47 Schematic FFC Boards Revision B PF400...
Page 56: ...PreciseFlex_Robot 48...
Page 57: ...Hardware Reference 49 Schematic FFC Boards Revision C PF400...
Page 58: ...PreciseFlex_Robot 50 Schematic FFC Boards 3kg PF400...
Page 59: ...Hardware Reference 51...
Page 60: ...PreciseFlex_Robot 52 Schematic Safety System Overview PF400 CAT3...
Page 61: ...Hardware Reference 53...
Page 62: ...PreciseFlex_Robot 54 Controller Power Amplifier Connectors Control Board Connectors...
Page 63: ...Hardware Reference 55 Gripper and Linear Axis Controller Connectors...
Page 64: ...PreciseFlex_Robot 56...
Page 65: ...Hardware Reference 57...
Page 66: ...PreciseFlex_Robot 58 Schematic Slip Ring for 60N Gripper...
Page 67: ...Hardware Reference 59...
Page 68: ...PreciseFlex_Robot 60...
Page 69: ...Hardware Reference 61...
Page 70: ...PreciseFlex_Robot 62...
Page 71: ...Hardware Reference 63...
Page 72: ...PreciseFlex_Robot 64...
Page 73: ...Hardware Reference 65 Motor 60N Gripper...
Page 74: ...PreciseFlex_Robot 66...
Page 106: ...PreciseFlex_Robot 98 b The CALPP application takes about 1 minute to run...
Page 124: ...PreciseFlex_Robot 116 Wiring for 60N Gripper with Battery Pigtail Wiring for Pneumatic Gripper...
Page 125: ...117 Wiring for Vacuum Gripper Wiring for Vacuum Pallet Gripper...