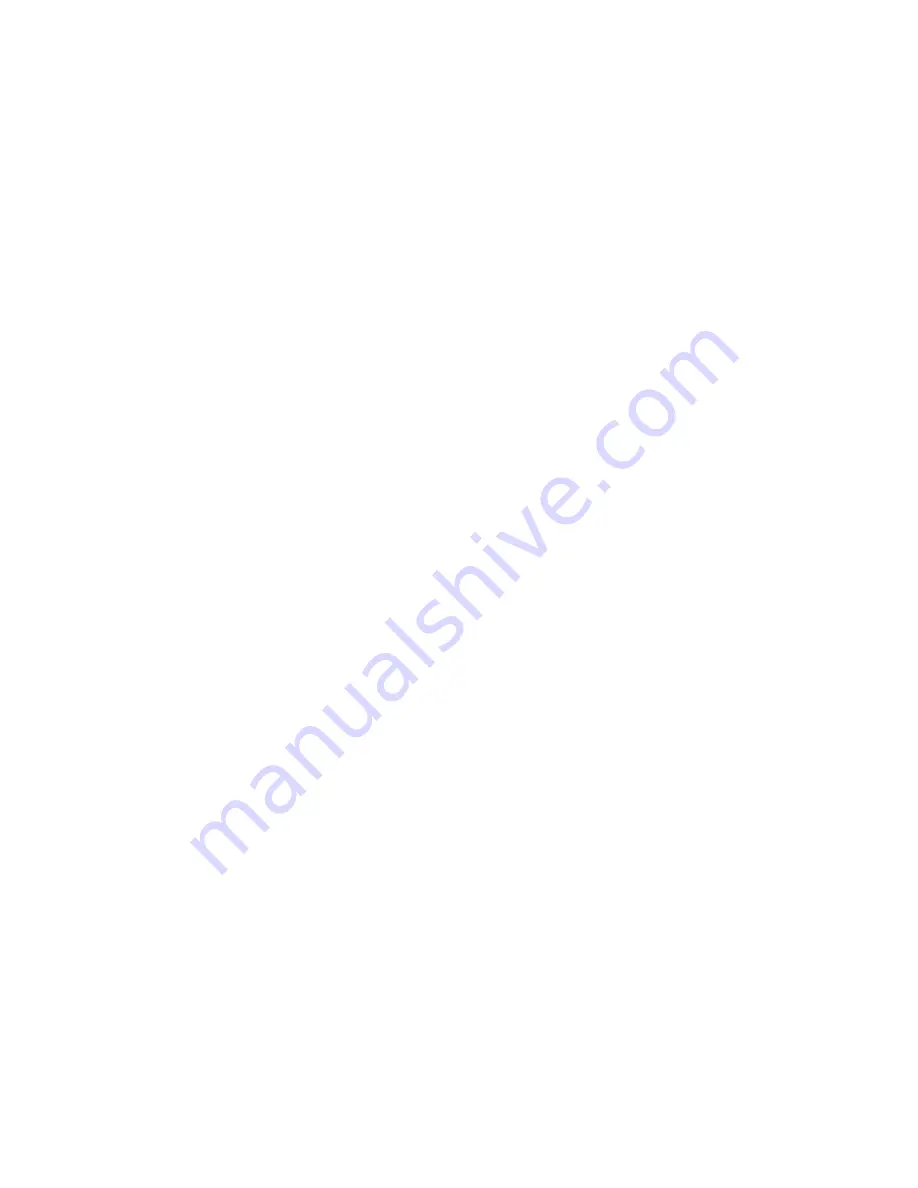
PreciseFlex_Robot
88
In a similar manner parameter 10351 can be used to limit the gripper opening force. In this case the
value for the opening force is ( (<Contents of 10351>-<tcnts to oppose spring force>)/4378)X18N –
(Spring force at position). For example, in landscape mode the spring force is about 8N, and if the
contents of 10351 are 5200, this value will be (5200-2200)/4378X18N -8N or 4.3N. Note that 5200 is
about as low a value as you would want to use in landscape mode for parameter 10351, to ensure there
is enough force to oppose the spring and open the gripper all the way to the homing position. For many
cases, 10351 can be left at its default value of 0, in which case it is disabled.
End of Travel Sensor
The Precise 23N EGripper includes a sensor to detect the gripper closed to hard stop position. The spring
will return the gripper to this position if power is off and there is no plate in the gripper. This sensor is
wired to Digital Input 2 on the Gripper Controller Board which can be read at Digital Input 210002. This
input can be viewed in the Web Browser under Control Panels/Remote IO/Network Node 2 IO. At power
up this sensor can be checked to determine if the gripper is fully closed, and thus not holding a plate. If
the gripper is not fully closed it will be holding a plate, and the operator should be directed to remove the
plate before homing the robot, which will open the gripper to the maximum hard stop. The 60N servo
gripper has an absolute encoder and position can be checked after homing, which does not move the
gripper fingers.
Grip Test and Squeeze Check
It may be desirable to check if a plate is gripped by checking the gripping torque value. The output torque
to the motor is available in Parameter 12304, value 5 in the parameter data base. For a non-spring
gripper, this value varies between 0 and 4378 tcnts for a maximum gripper force of 18N. For a spring
gripper, per above, for a portrait grip, the spring adds about 1600 tcnts to the squeeze and for a
landscape grip, it adds about 2200 torque counts to the squeeze. Since this value is taken into account
by the spring compensation and is offset from the torque commanded to the motor in Parameter 12304,
when checking Parameter 12304 to determine squeeze the spring compensation must be subtracted from
the torque value in Parameter 12304. For example, if the gripper is at the portrait position and not holding
a plate, it must servo against the spring. In this case the value in Parameter 12304 will be about 1600
tcnts. To determine the effective squeeze torque, subtract 1600 tcnts from this value, which results in
zero tcnts of squeeze force. If the value in 12304 is -2700, then the gripper motor is squeezing with -
2700 tcnts, and the spring is adding -1600 tcnts, and the effective squeeze is -4300 tncts, or about 18N.
The exact spring compensation value is stored in field 5 of Parameter 12331. For the best accuracy in
determining effective squeeze force at any gripper opening, subtract this value from the value in 12304.
Servo Gripper Controller Digital Inputs and Outputs
The Servo Gripper Controller PCA (GSB) adds 3 general optically isolated digital outputs and 3 general
optically isolated digital inputs to the standard digital I/O found on the Guidance Controller. Like the other
general inputs and outputs, they can be assigned for various control purposes during system setup, or
they can be used directly by a GPL procedure.
Unlike the controller's standard digital I/O that are directly accessed on demand, these I/O are scanned
by the controller. The scanning period is nominally 4 milliseconds, so your application must be able to
handle a delay of up to 4 milliseconds for signal changes to propagate through the system. Note that
effective with Rev 4 of the GSB board
, two IO pins have optional assignments based on jumpers. J4 is
connected to pins 2 and 3 to connect Digital Input 1 to pin 6 and is connected to pins 1 and 2 to connect
pin 6 to a line that goes back to the controller RS232 RXD input. J7 is connected to pins 2 and 3 to
connect Digital Output 3 to pin 3 and is connected to pins 1 and 2 to connect pin 3 to a line that goes
back to the controller RS232 TXD input. Note further that on the controller CPU board, two more jumpers
Summary of Contents for PF3400
Page 8: ......
Page 32: ...PreciseFlex_Robot 24 Appendix B TUV Verification of PF400 Collision Forces...
Page 33: ...Introduction to the Hardware 25...
Page 34: ...PreciseFlex_Robot 26...
Page 35: ...Introduction to the Hardware 27...
Page 37: ...Introduction to the Hardware 29 Appendix C Table A2 from ISO TS 15066 2016...
Page 38: ...PreciseFlex_Robot 30 Table A2 Continued...
Page 41: ...Introduction to the Hardware 33 PF400 500gm Safety Circuits PF3400 3kg Safety Circuits...
Page 45: ...Installation Information 37...
Page 46: ...PreciseFlex_Robot 38...
Page 47: ...Installation Information 39...
Page 48: ...PreciseFlex_Robot 40...
Page 54: ...PreciseFlex_Robot 46 Schematic System Overview...
Page 55: ...Hardware Reference 47 Schematic FFC Boards Revision B PF400...
Page 56: ...PreciseFlex_Robot 48...
Page 57: ...Hardware Reference 49 Schematic FFC Boards Revision C PF400...
Page 58: ...PreciseFlex_Robot 50 Schematic FFC Boards 3kg PF400...
Page 59: ...Hardware Reference 51...
Page 60: ...PreciseFlex_Robot 52 Schematic Safety System Overview PF400 CAT3...
Page 61: ...Hardware Reference 53...
Page 62: ...PreciseFlex_Robot 54 Controller Power Amplifier Connectors Control Board Connectors...
Page 63: ...Hardware Reference 55 Gripper and Linear Axis Controller Connectors...
Page 64: ...PreciseFlex_Robot 56...
Page 65: ...Hardware Reference 57...
Page 66: ...PreciseFlex_Robot 58 Schematic Slip Ring for 60N Gripper...
Page 67: ...Hardware Reference 59...
Page 68: ...PreciseFlex_Robot 60...
Page 69: ...Hardware Reference 61...
Page 70: ...PreciseFlex_Robot 62...
Page 71: ...Hardware Reference 63...
Page 72: ...PreciseFlex_Robot 64...
Page 73: ...Hardware Reference 65 Motor 60N Gripper...
Page 74: ...PreciseFlex_Robot 66...
Page 106: ...PreciseFlex_Robot 98 b The CALPP application takes about 1 minute to run...
Page 124: ...PreciseFlex_Robot 116 Wiring for 60N Gripper with Battery Pigtail Wiring for Pneumatic Gripper...
Page 125: ...117 Wiring for Vacuum Gripper Wiring for Vacuum Pallet Gripper...