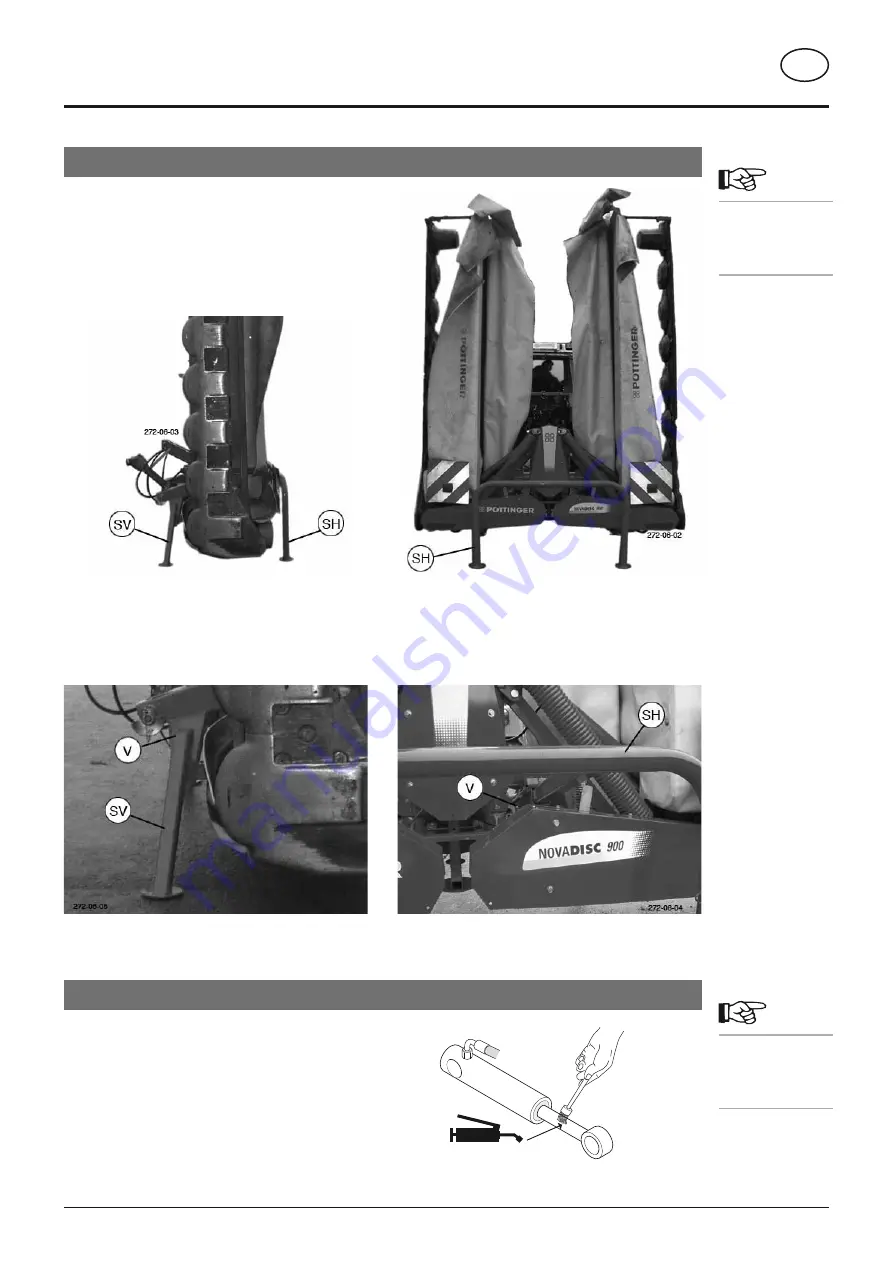
- 8 -
0600-GB Abstellen_3904
GB
PARKING THE UNIT
Parking implement in transport position
Rear fitting of parking supports (SH)
- Pin the supporting yoke (SH) in retaining tube
- secure with linch pin (V) (left and right)
When parking for longer periods in the open, clean
plunger rods and then coat with grease.
At season‘s end
- clean plunger rod and all other shiny parts, then grease
them
- pay attention to the hints in chapter
„MAINTENANCE“
FETT
TD
49/9
3/2
Parking in the open
Note!
Additional parking supports (SV, SH) can be fitted to
implement when parking in transport position (optional
extra)
Front fitting of parking supports (SV)
- Pin the support stands (SV) left and right in the
recesses
- secure with linch pin (V)
Note!
Remove the
parking supports
from the machine
during operation
Note
A rusty plunger
rod can damage
cylinder‘s sealing
elements.