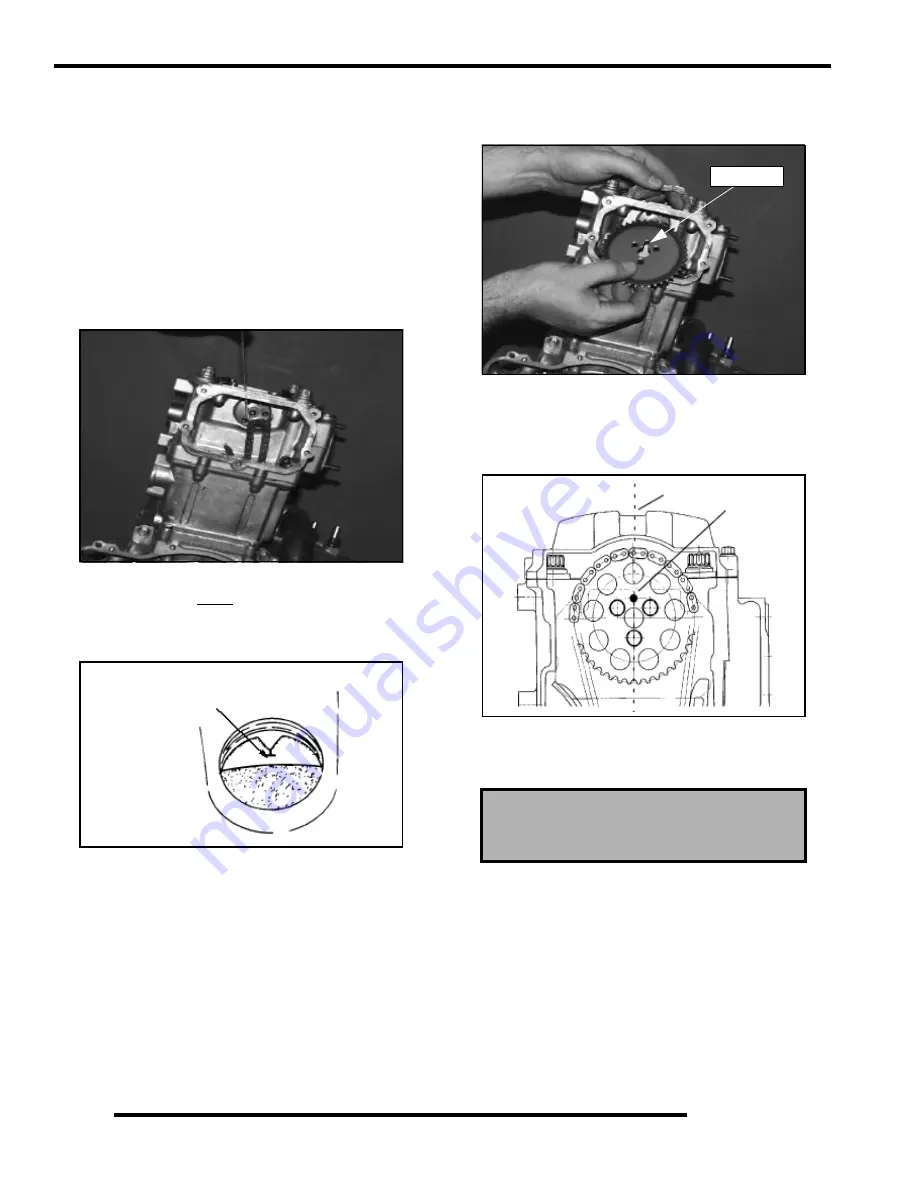
3.46
ENGINE
IMPORTANT: CAMSHAFT TIMING NOTE: In order to
time the camshaft to the crankshaft, the piston must
be precisely located at Top Dead Center (TDC).
Camshaft Timing
1. Apply Polaris Premium Starter Drive Grease (PN
2871460) to the camshaft main journals and cam lobes.
Lubricate automatic compression release mechanism with
clean engine oil. (To install the compression release
mechanism, refer to Page 3.21).
2. Install the camshaft with the lobes facing downward and the
sprocket alignment pin facing upward.
3. Disconnect the wire from the cam chain and rotate the
engine to align the single (TDC ) timing mark (Top Dead
Center) on the flywheel with the notch in the timing
inspection window. Be sure to use the single TDC mark
when installing the cam. Do not use the advance marks.
4. Loop the cam chain on the cam sprocket with the dots on
the sprocket facing outward and the alignment pin notch
facing directly upward.
5. Before positioning the sprocket on the camshaft, check the
position of the cam sprocket alignment pin. When the cam
is positioned properly, the cam sprocket alignment pin (A)
is directly in line with the crankshaft / camshaft centerline
(B).
6. Install the sprocket on the camshaft. Apply Loctite™ 242
(PN 2871949)
to the cam sprocket bolts and torque to
specifications.
7. Verify TDC mark in timing inspection hole and alignment
pin is directly in line with crankshaft to camshaft centerline.
Refer to Illustration on the following page.
8. Apply Crankcase Sealant
(PN 2871557)
to the camshaft
end cap and install using a new O-Ring.
9. Check all cam timing marks to verify proper cam timing,
and install the cam chain tensioner body with a new gasket.
10. After tensioner installation, rotate engine at least two
revolutions and re-check marks/timing.
Single (TDC)
Mark Aligned
Cam Sprocket Bolt Torque:
6 ft. lbs. (8 Nm)
Pin Notch
A
B
Summary of Contents for Ranger 500 2x4 2007
Page 1: ......
Page 20: ...1 18 GENERAL INFORMATION SAE Tap Drill Sizes Metric Tap Drill Sizes Decimal Equivalents ...
Page 82: ...3 23 ENGINE 3 Cylinder Head Exploded View EH50PL EFI Shown A A ...
Page 153: ...4 45 ELECTRONIC FUEL INJECTION 4 Fuel Pump Circuit Ignition Coil Circuit ...
Page 157: ...4 49 ELECTRONIC FUEL INJECTION 4 Diagnostic Connector Circuit ...
Page 296: ...10 10 ELECTRICAL POWER DISTRIBUTION MODULE NON EFI MODELS PDM Operation ...
Page 309: ...10 23 ELECTRICAL 10 EFI Cooling System Break Out Diagram PDM RD WH Key On 12 V Power ...
Page 332: ...10 46 ELECTRICAL Transmission Switch Circuit Differential Solenoid Circuit ...
Page 333: ...10 47 ELECTRICAL 10 Charging System Circuit Cooling Fan Circuit ...
Page 334: ...10 48 ELECTRICAL AWD Circuit ...
Page 339: ...WD 1 WIRE DIAGRAM RANGER 500 2X4 4X4 CHASSIS ...
Page 340: ...WD 2 WIRE DIAGRAM RANGER 500 2X4 4X4 DASH ...
Page 341: ...WD 3 WIRE DIAGRAM RANGER 500 EFI 4X4 CHASSIS PAGE 1 OF 2 ...
Page 342: ...WD 4 WIRE DIAGRAM RANGER 500 EFI 4X4 CHASSIS PAGE 2 OF 2 ...
Page 343: ...WD 5 WIRE DIAGRAM RANGER 500 EFI 4X4 DASH ...
Page 344: ...WD 6 WIRE DIAGRAM RANGER 500 EFI 4X4 BREAKOUTS ...
Page 345: ...WD 7 WIRE DIAGRAM RANGER 500 2X4 4X4 BREAKOUTS ...