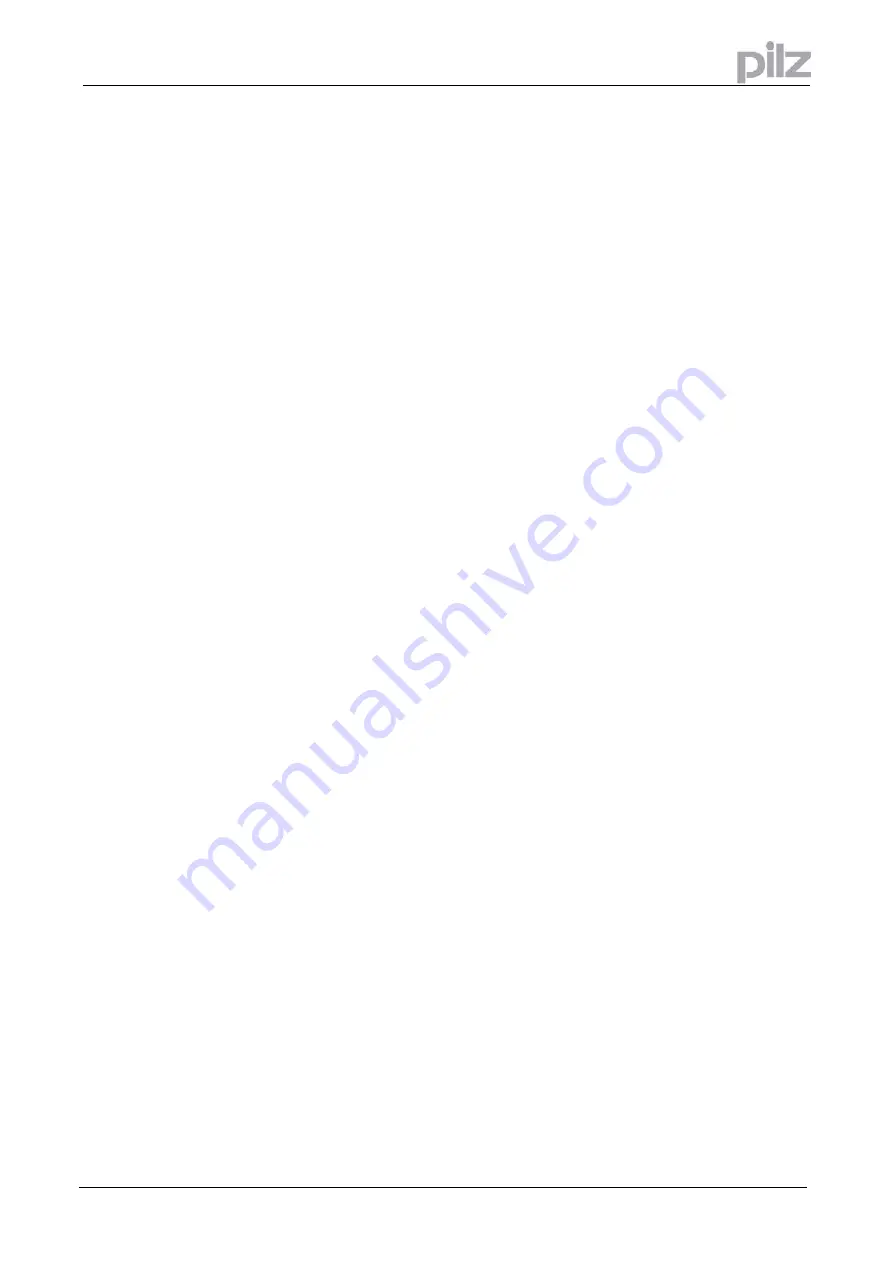
2 Table of contents
Installation manual PMCprimo Drive2
Page
5
10
Commissioning................................................................................................. 78
10.1
Important notes ....................................................................................................... 78
10.2
Setup software PDRIVE.......................................................................................... 80
10.2.1
Use as directed............................................................................................... 80
10.2.2
Software description ....................................................................................... 80
10.2.3
Hardware requirements .................................................................................. 80
10.2.4
Minimum requirements for the PC: ................................................................. 80
10.2.5
Installation under WINDOWS 95 / 98 / NT / 2000 / XP................................... 80
10.2.6
Working with PDRIVE..................................................................................... 80
10.3
Parametrization of the PMCprimo Drive2................................................................ 81
10.4
Programming of the PMCprimo Drive2 ................................................................... 81
10.5
Error messages....................................................................................................... 82
10.5.1
Error messages PMCprimo
............................................................................ 82
10.5.2
Error messages amplifier................................................................................ 83
10.6
Warnings................................................................................................................. 84
10.7
Status messages..................................................................................................... 85
10.7.1
Status messages PMCprimo .......................................................................... 85
10.7.2
Status messages drive ................................................................................... 85
11
Appendix ........................................................................................................... 86
11.1
Notes on EMC problems ......................................................................................... 86
11.1.1
Cable screening.............................................................................................. 86
11.1.2
Metallic, large area connections ..................................................................... 87
11.1.3
PE connection, earthing, grounding................................................................ 87
11.1.4
Motor choke.................................................................................................... 87
11.1.5
Expansion board............................................................................................. 88
11.1.6
Ethernet interface of the expansion board X11/5 ........................................... 88
11.1.6.1
General................................................................................................... 88
11.1.6.2
Interface.................................................................................................. 89
11.1.6.3
Configuration IP address
........................................................................ 90
11.2
Change of the buffer battery ................................................................................... 92
11.3
Transport, storage, maintenance, disposal ............................................................. 93
11.4
Removing faults ...................................................................................................... 94
11.5
Index ....................................................................................................................... 96
Artisan Technology Group - Quality Instrumentation ... Guaranteed | (888) 88-SOURCE | www.artisantg.com