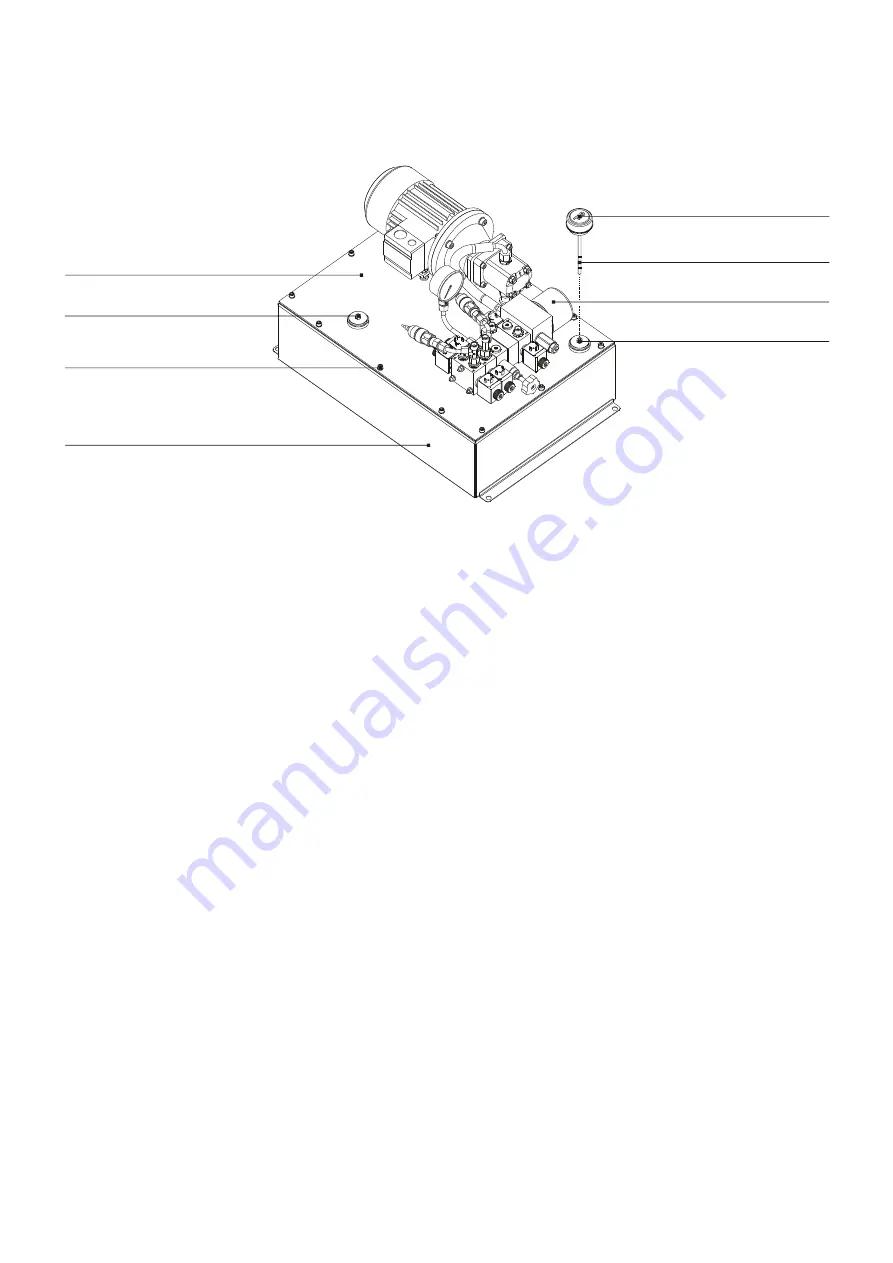
FILLING CAP
OIL LEVEL
RETURN FILTER
TRANSPORT CAP
TRANSPORT CAP
LID
SCREW M10
TANK
The following principles must be adhered to during the assembly of hydraulic circuit elements and piping. The basic rule in cleaning
and maintenance is cleanliness and orderliness! The hydraulic circuit consists of very precise elements and it is very difficult,
complicated and costly to remove any contamination and its consequences. Remove the protective cap just before putting the device
into operation. Consistently check the oil level on the gauge located on the filling cap on the hydraulic unit.
6.5.1. Work safety
The hydraulic circuits are reliable and safe even when under high pressure, if all the elements are appropriately sized. However,
a breakdown due to material defect or fatigue can occur in them, which could endanger the safety of the staff or contaminate the
environment with oil. Examples of visible defects:
• dripping oil;
• destruction of pressure-loaded circuit parts.
Oil dripping from an untight connection or another spot, which collects on the floor, can cause slipping and falling of persons or floor
damage and
leakage to
the environment, it can cause extensive pollution of large quantities of water. The destruction of pressure -
loaded circuit parts does not lead to any explosion. If the crack is small, oil is disperses to the environment in the form of mist, if the
crack is large, mostly the whole tank will discharge. The destruction of pressure hoses will manifest itself by oil leaking, but very
frequently also by bursting of hose socket. In such case, the hose can spring up and cause a serious injury. Both failures cause
pollution of the environment and even a small spark can lead to a huge fire.
It follows that the following principles must be taken into account for installation and operation of hydraulic circuits:
• keep the machine clean, sprinkle the
leaked
oil with wood chips or VAPEX absorbate, sweep the floor, clean it with an
appropriate solvent and dry;
• while dismantling, prevent oil spilling by installing suitable containers;
• units and all hydraulic elements including hoses and pipelines must be protected against external mechanical damage and heat
resources;
• if the circuit is under pressure, do not come close to the pipelines and hoses, particularly do not expose your face;
• should oil be spilled into eyes, flush eyes with Ophtal or any other suitable agent immediately;
• if the anti-flaming agent is in eyes, seek medical help immediately.
• do not smoke or use open fire in the
storage facility
and near the units and hydromotors;
• shut down the hydrogenerator drive whenever you make any changes or repairs;
• electrical equipment must comply with ESC regulations;
• containers with industrial petrol may only be used in specifically designed spaces and must be covered with a cover or a closure at
all times;
• hydromotors, which could start turning automatically in case that the driving hydrogenerator switches off (pressure drop), must be
mechanically or hydraulically locked against this possibility;
• all hydraulic systems and circuits must be protected by a pressure valve against an overload, as well as hydromotors, which could
become overloaded after hydraulic locking;
• the person responsible for maintenance and setting of the hydraulic unit must be appointed.
The afore mentioned
principles of safety at work are not exhaustive.
There are different conditions for each hydraulic circuit and different possibilities of endangering the environment.
The afore
mentioned
, however, should reduce the accident rate and improve the working conditions of users.
6.5.
Principles of Hydraulic Unit Maintenance