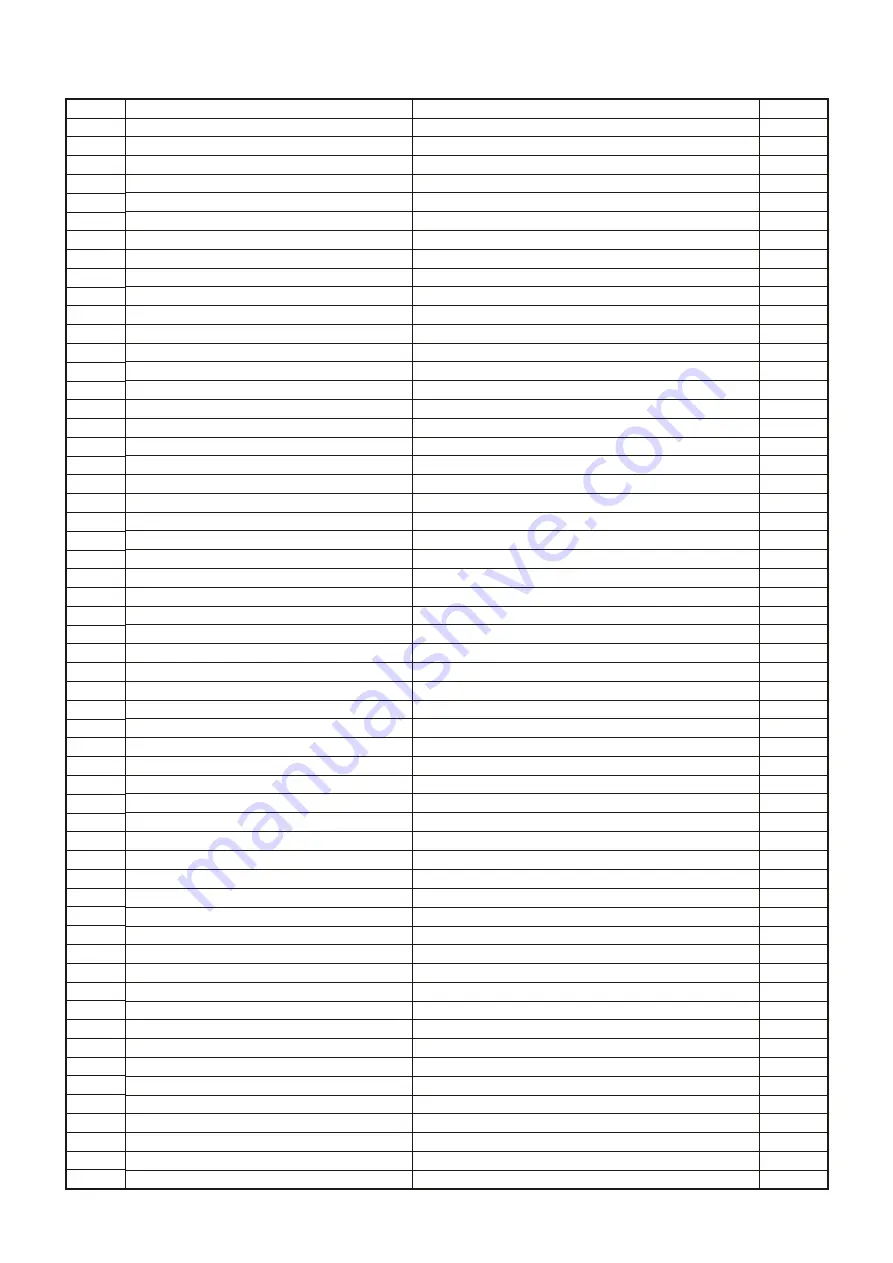
BP1
BP2
BP3
BP4
BP5
BP6
BP7
IS1
IS2
IS3
IS4
KM1
KM2
KM3
KM4
KM5
KM6
KM7
FQ1
FQ2
FQ3
FQ4
FQ5
FQ6
FU1
FU2
FU3
FU4
FU5
FU6
FU7
FU8
FU9
KA1
KA2
KA3
KA4
KA5
KA6
P1
SB1
Diagram:
Limit switch
Limit switch
Limit switch
Limit switch
Limit switch
Limit switch
Limit switch
optical sensor (receiver)
optical sensor (transmitter)
inductive sensor
inductive sensor
Contactor
Contactor
Contactor
Contactor
Contactor
Contactor
Contactor
Motor actuator
Circuit breaker
Motor actuator
Circuit breaker
Motor actuator
Circuit breaker
The fuse holder
Fuse glass
The fuse holder
fuse glass
The fuse holder
fuse glass
The fuse holder
Fuse glass
The fuse holder
Fuse glass
The fuse holder
Fuse glass
The fuse holder
Fuse glass
The fuse holder
Fuse glass
The fuse holder
fuse glass
Relay
Cap
Relay
Cap
Relay
Cap
Relay
Cap
Relay
Cap
Relay
Cap
Potentiometer
Machine button
TOTAL STOP button
Type:
Order No.:
016830
002491
002490
002532
002491
002491
002490
016447
016448
019513
019513
012488
012488
012488
012488
016828
016828
012488
001921
003896
001871
003597
021178
003597
001779
001597
001779
004197
001779
004197
001779
012712
001779
001792
001779
001597
001779
001597
001779
006674
001779
004197
013691
013490
013691
013490
013691
013490
013691
013490
013691
013490
013691
013490
002780
002781
006104
FR993 with the key D1
FR615
FR6A1
FR693 with the key D1
FR615
FR615
FR6A1
BOS 08M PS RE11 S49
BOS 08M X RS11 S49
BES M08MI-POC20B-S49G
BES M08MI-POC20B-S49G
DILEM - 10(24V DC)
DILEM - 10(24V DC)
DILEM - 10(24V DC)
DILEM - 10(24V DC)
DILEM - 01(24V DC)
DILEM - 01(24V DC)
DILEM - 10(24V DC)
MS 325 + HKF11 1-1,6A
S 203-C 10
MS 325 + HKF11 0,24-0,4A
S 201-C 6
MS 325 + HKF11 0.6-1A
S 201-C 6
Fuse terminal 5x20 tiltable
2A
Fuse terminal 5x20 tiltable
500mA
Fuse terminal 5x20 tiltable
500mA
Fuse terminal 5x20 tiltable
5A
Fuse terminal 5x20 tiltable
1,5A
Fuse terminal 5x20 tiltable
2A
Fuse terminal 5x20 tiltable
2A
Fuse terminal 5x20 tiltable
1A
Fuse terminal 5x20 tiltable
500mA
RJ2S-CL-D24
SJ2S-07L
RJ2S-CL-D24
SJ2S-07L
RJ2S-CL-D24
SJ2S-07L
RJ2S-CL-D24
SJ2S-07L
RJ2S-CL-D24
SJ2S-07L
RJ2S-CL-D24
SJ2S-07L
TP195 4K7/N
dia. 34.8mm
YW1B-V4E01R
Name:
Partlist ARG 260 CF-NC, ARG 300 CF-NC, ARG 300 DCT CF-NC
v 5.6 21.1.2015