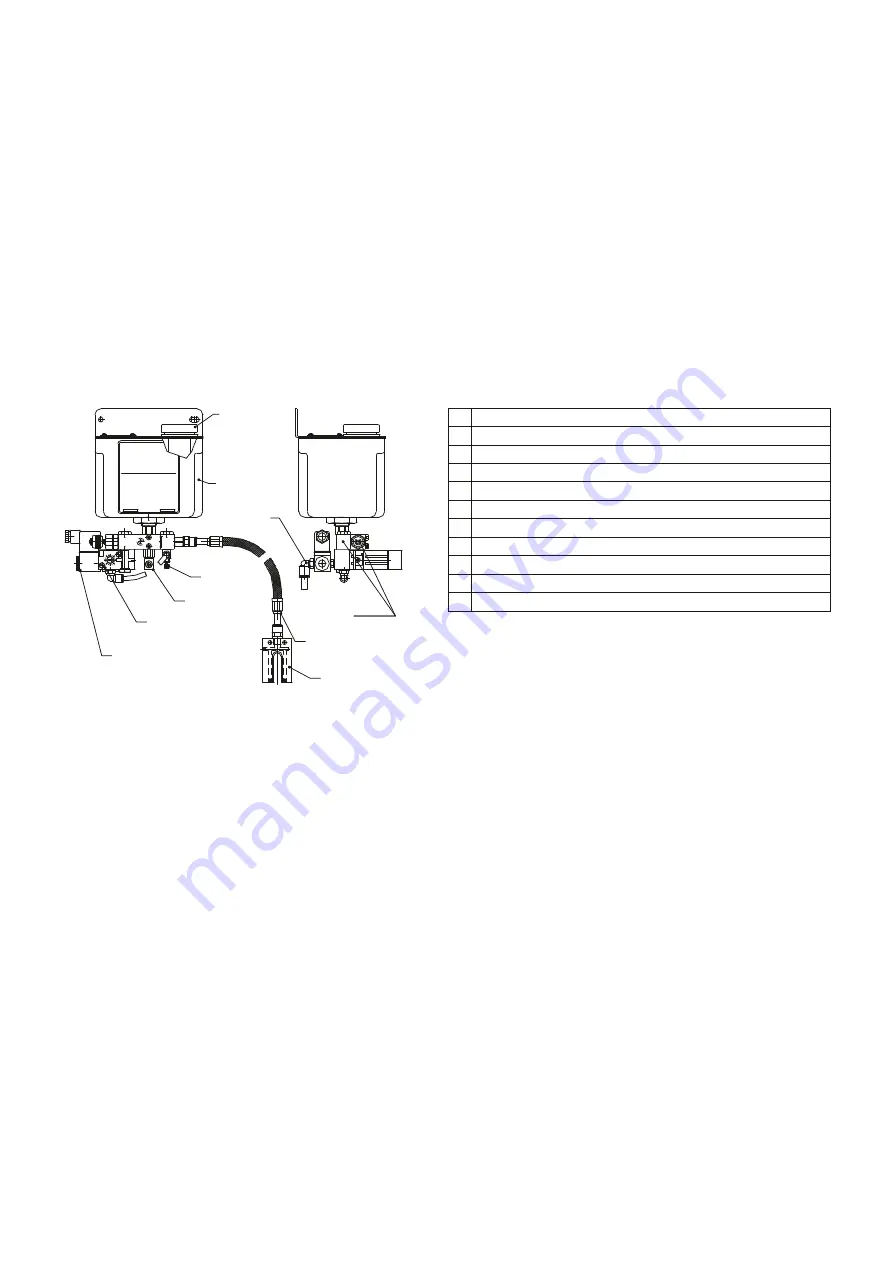
12.2. Oil Mist Lubrication
When using the standard cooling equipment, coolant leakages from the machine often occur, particularly when cutting long sections.
Oil mist lubrication is a device that creates oil mist, which is subsequently applied through nozzles directly onto the saw blade that is
then cooled and lubricated. The device functions by dosing oil and air mixture. It is also useful in the processing of material that
excludes the contact with a regular coolant. This lubrication system is lossy, so it is necessary to refill the coolant regularly.
The injection nozzle holder must be placed near the designated point in order to reach the optimum adjustment of the nozzle with the
least possible distance from the lubrication point. The supplied compressed air must be absolutely dry and oil free. Optimum
operating pressure is between 4 and 8 bars. Commissioning is carried out during the open subordinate actuating valve by an external
signal from the control valve (optional), the connection to the mains is facilitated by a supplied screw connector (PG9). Fill the tank
with COOLcut Micro liquid and the mist lubrication is ready for operation.
Important:
In the event of use of lubricating media other than the recommended, a risk of decay or deposits arise. That is why the system
functionality can only be guaranteed for the use of COOLcut Micro liquid.
SCREW-ON LID WITH A FILTER
1.2L CONTAINER
OIL MIST SETTING
FITTING HOLE
VENTING
PULSE GENERATOR
SOLENOID VALVE 24V DC PG 9 SOCKET
DOSING PUMP
COUPLING 8MM
2.5 M COAXIAL POWER CABLE (METAL PROTECTION)
NOZZLE HEAD CAT. NO.: 70.107.1
1
2
3
4
5
6
7
8
9
10
11
3
5
6
7
11
10
8
9
2
1
4
Oil mist venting
Oil mist lubrication system is supplied after testing.
Before commissioning and maintenance on the coaxial cable or nozzle, the system has to be vented. If the volume of oil in the
container does not drop under the minimum threshold, other venting is not necessary.
Venting procedure:
1.
Fill the tank with a clean lubrication medium.
2.
Loosen the drainage and venting screw a little and keep releasing the lubricating medium until there are no air bubbles present in it.
3.
Set the pulse generator frequency to the maximum value (approx. 66 pulses per minute).
4.
Set the dosing pump piston stroke to the maximum.
5.
Connect the compressed air and fill the capillary tube, so that all the tubing along the whole length is bubble-free (filling duration
depends on the length of tubing).
6.
C
onnect to coaxial head to the spray head.
7.
After venting, set the frequency and piston stroke to operating values again.
Oil mist setting
1.
Pulse generator settings: pneumatic time relay controls the dosing pump. You can set the frequency continuously from 0 to 66
pulses per minute.
2.
Dosing pump settings: the piston vacuum pump doses the lubricating medium under high pressure. The quantity of the lubricant
can be regulated by turning the manual setting wheel.
3.
Oil mist spray setting: By spraying the air the drops form a very fine lubricating film and its setting influences the degree of
dispersion, cooling and chips formation. Volume of air in the nozzle can be adjusted by the adjustment screw.