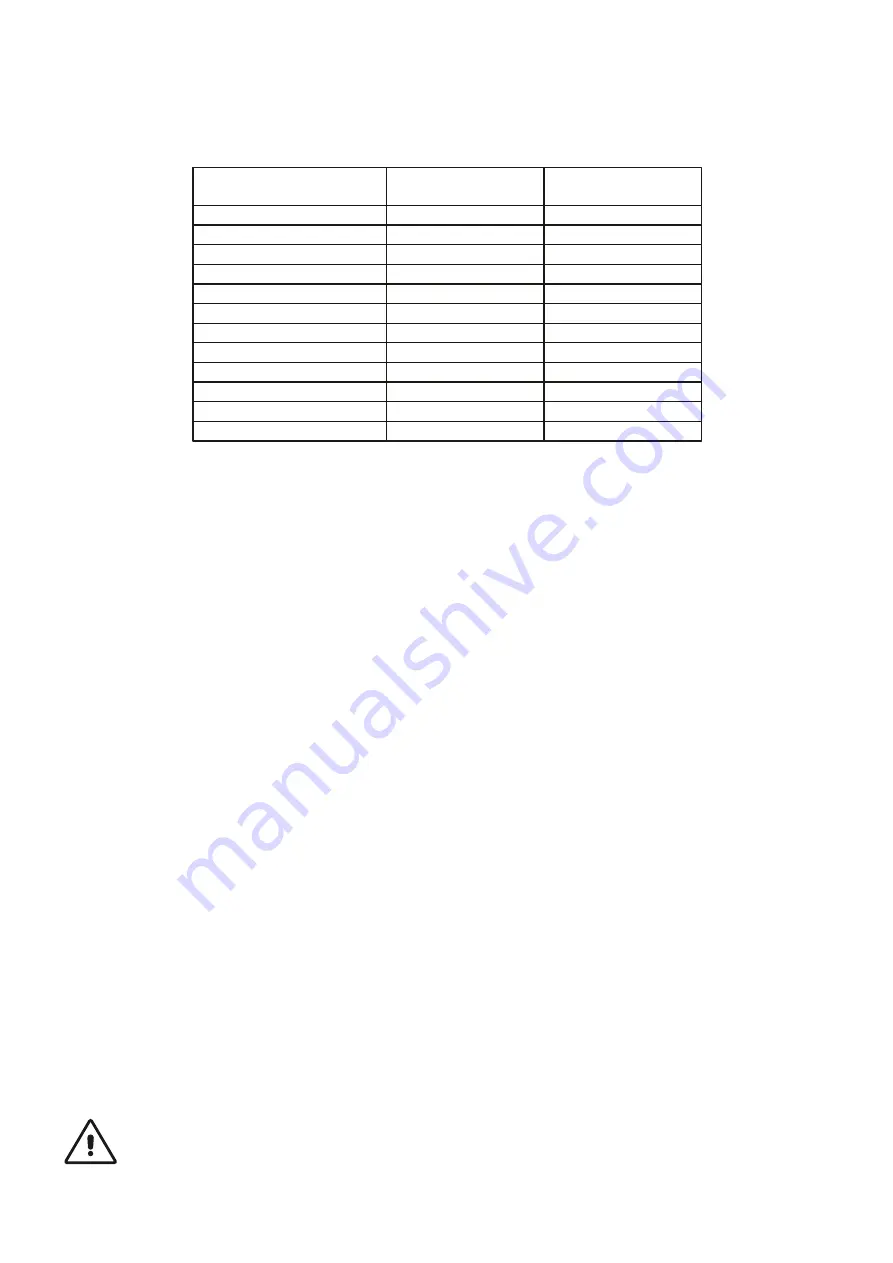
6.5.5. Service intervals
The hydraulic unit is filled with OPTIMA HV46 hydraulic oil, for which it is recommended to replace the oil within a time
interval shorter than 4,500 operating hours, along with the return filter, or once in a year depending on what occurs first.
Replace the return filter each 1,500 operating hours (MANN FILTER W 79 supplied by the manufacturer). Consistently
check the oil level on the gauge located on the filling cap on the hydraulic unit in the machine base. The oil level must be
maintained between the two oil marks.
6.5.6. Oil Refill and Filter Replacement
• Unscrew the return oil filter.
• Remove the lid of the hydraulic unit by unscrewing the twelve M10 bolts.
• Very carefully raise the lid and make sure the sealing does not stick to the lid or the tank, leading to its damage.
• If the sealing is damaged, replace it for a new one. Never use a damaged sealing, otherwise you risk contamination of the hydraulic
system by the remnants of cork sealing.
• When replacing the oil, pour out the old oil and clean the tank. A cloth is a sufficient tool for cleaning, but it must be non-linting. You
can use a solution that does not disturb the tank coating and does not leave residues in the tank. After the cleaning, check the inside of
the tank thoroughly. Check the condition of the oil-resistant coating. Should any flaking or poor quality manifest themselves, remove
the coating with an appropriate solvent, wash, dry and clean with pressure air. In this way, failures caused by the deteriorated coating,
which contaminates the entire hydraulic system, will be prevented.
• Once the tank is clean and free from deposits, place the lid and the sealing back on the tank using a reverse procedure and cross-
tighten the screws.
• Pour in new oil. Only oil recommended by the equipment manufacturer can be filled in. Never refill directly from barrels. Always use
a filter unit with filters with a mesh density lower than 25 µm. Using filters with contamination indication improves the quality and
convenience of the work. Consistently check the oil level on the gauge located on the filling cap.
The oil level must be maintained
between the two oil marks.
• Unscrew the new return oil filter.
• check the piping for noise and leakage.
• Start the hydraulic unit within short intervals.
• Vent the hydraulic circuit. Venting is performed usually by raising and descending the arm, clamping and unclamping the vice.
Repeat several times, until the system is ventilated (usually 5-10 times).
Caution: Oil and the filter are classified as special waste!
7. Faults and Remedies
7.1. Repairs
HM 32
HM 46
CETOP RP 91 H Specifications
AGIP
ARAL
BP
CASTROL
ESSO
MOBIL
MOGUL
OLEA
ÖMV
PARAMO
SHELL
VALVOLINE
OSO 32
VITAM GM 32
ENERGOL HLP 32
HYSPIN AXS 32
NUTO H 32
MOBIL DTE 24
MOGUL HM 32
OPTIMA HM 32
HLP 32
PARAMOL HM 32
TELLUS OIL 32
ULTRAMAX AW 32
VITAM GF 46
ENERGOL HLP 46
HYSPIN AWS 46
NUTO H 46
MOBIL DTE 25
MOGUL HM 46
OPTIMA HM 46
HLP 46
PARAMOL HM 46
TELLUS OIL 46
ULTRAMAX AW 46
OSO 46
6.5.4. Hydraulic Mineral Oils
HM performance class according to CETOP RP 91H European specification in viscosity classes ISO VG 32 and 46. Oils marked as
HM 32 are recommended for use in environment with ambient temperatures reaching 0 °C and below 0 °C. HM 46 oil types are
recommended for use in environment with ambient temperatures within the range +5 °C and +40 °C.
Caution! Danger of injury!
Carry out repairs only when the master switch is off or secured against switching on or when the machine is
isolated from the power supply and secured against restarting. The saw arm must always be supported
mechanically in the lower position while it is being repaired - see section 3.5. We recommend to contact an
authorised service centre for repairs.