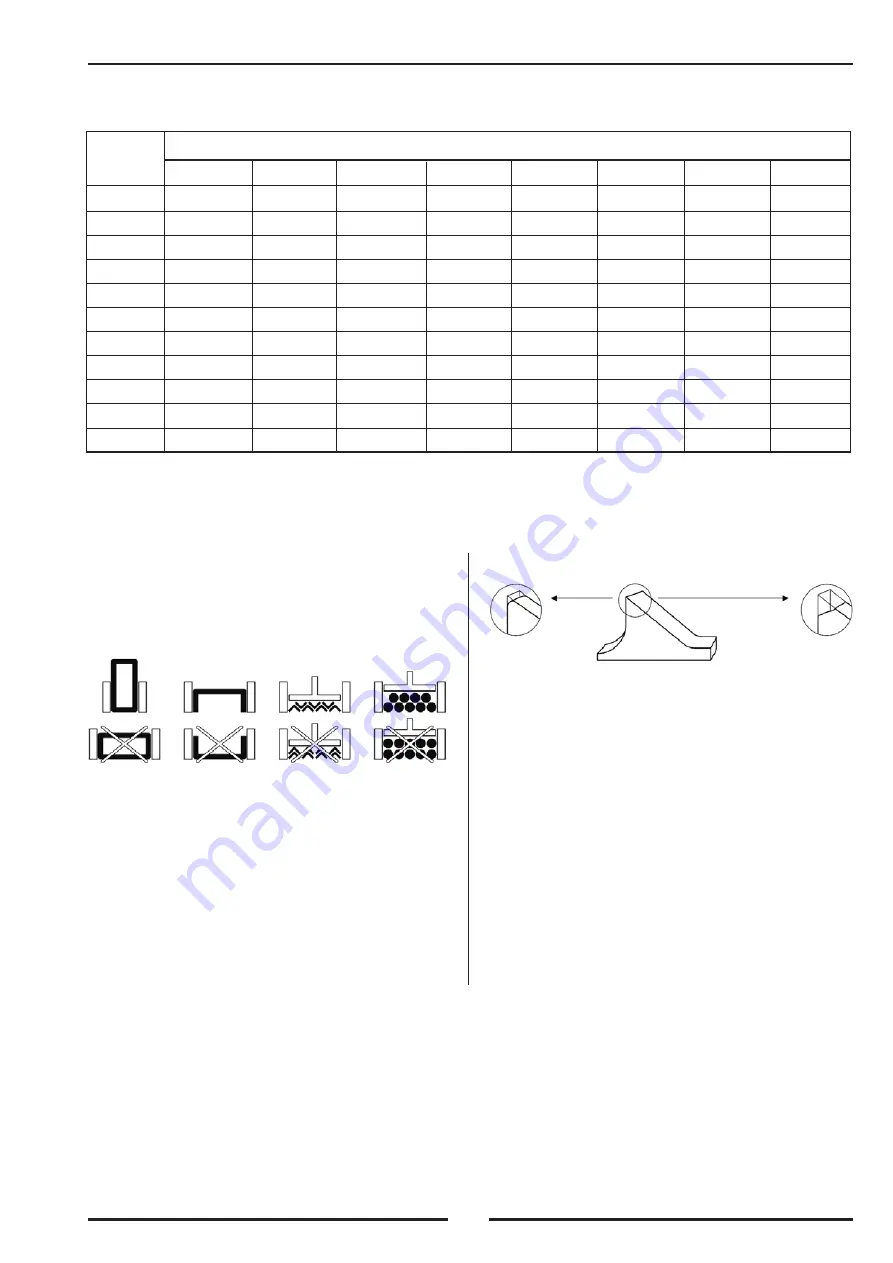
23
20
40
60
80
100
120
150
200
2
18
18
18
10/14
10/14
10/14
10/14
10/14
3
18
18
10/14
10/14
10/14
10/14
8/12
8/12
4
18
10/14
10/14
10/14
8/12
8/12
6/10
6/10
5
18
10/14
10/14
8/12
6/10
6/10
6/10
5/8
6
10/14
10/14
8/12
8/12
6/10
6/10
5/8
5/8
8
10/14
8/12
6/10
6/10
5/8
5/8
5/8
4/6
10
8/12
6/10
6/10
5/8
5/8
5/8
4/6
4/6
12
8/12
6/10
5/8
5/8
4/6
4/6
4/6
4/6
15
6/10
5/8
5/8
4/6
4/6
4/6
4/6
3/4
20
6/10
5/8
4/6
4/6
4/6
3/4
3/4
3/4
30
6/10
5/8
4/6
4/6
3/4
3/4
3/4
2/3
Wall
thickness
(mm)
Tube diameter D (mm)
Note: The a.-m. values do not refer to cutting of different sections. Such a requirement must be treated with respect to the section shape, the number of pieces
in the bundle and the dimensions. When the saw blade is used for cutting sections, its life becomes
Rule: At least four, but not more than thirty teeth must bite while a workpiece is being cut.
Tooth sizes recommended for cutting sections
6.3. Optimum Workpiece Clamping
The correct workpiece clamping can substantially influence the saw blade
life, the quality and precision of the cut and enables the correct selection of
the tooth size. For bundle cutting, the use of the upper (vertical) pressure
device is recommended. Observe the following kinds of clamping to achi-
eve an optimum cut (life and cutting power):
6.4. Running-in New Saw Blades
The running-in refers to new saw blades. The sharp cutting edges with
extremely small edge radii enable high cutting power. In order that the
maximum tool life may be achieved, it is necessary to run in the saw blade
to the optimum. Depending on the correct cutting speed and the workpie-
ce feed and the quality of its material, the saw blade must be run in only
with 50% of currently used feed. In this way the breaking of extremely
sharp edges particularly in big workpiece sections will be prevented. These
micro-fragments cause destruction of further teeth. Should vibrations or
sounds due to oscillations manifest themselves when a new saw blade has
been fitted, reduce the cutting speed slightly. In small workpiece sections
it is recommended to run in the saw blade with a reduced power for 15
minutes, in big sections for 30 minutes. Then increase the feed slowly to
the optimum value.
Observe the saw blade
running-in at all times
Correctly run-in
cutting edge
Micro-chips in
high starting feed
6.5. Factors Influencing Saw Blade Life
inappropriate saw blade tooth size • inappropriate saw blade speed and saw
blade lowering speed in the cutting position • the saw blade (the whole
band saw head) bears against the workpiece when the band saw is not in
the cutting position • the workpiece is not clamped as recommended • the
saw blade tension is not correct (mostly too little tension) • the saw blade
is not correctly fitted on the guide wheels (the saw blade touches the wheel
shoulder) • the saw blade guide heads are not correctly adjusted • the
distance between the saw blade guide heads and the workpiece is too big •
the oil content of the coolant is too low • the saw blade is not correctly run
in • saw blade maintenance is bad, the metal chips have not been removed
from the band saw.
The a.-m. faults cause inaccurate cut, reducing the saw blade life
and/or causing even its damage.
6.6. Values Recommended for Cutting
The selection of values depends on the material class and the material sec-
tion. The table data serve only as a guide; they have to be adjusted to the
material for certain ranges. The numbers of the CSN-Standards serve for
information only. They define only the guide for the material properties for
which the respective saw blade type is designed.
Summary of Contents for 20875-0204
Page 5: ...4 ARG 380 Plus S A F ARG 500 Plus S A F...
Page 35: ...34 ARG 380 Plus S A F ARG 500 Plus S A F...
Page 65: ...64 ARG 380 Plus S A F ARG 500 Plus S A F...
Page 92: ...91...
Page 93: ...92...
Page 94: ...93...
Page 95: ...94...
Page 96: ...95...
Page 97: ...96...
Page 98: ...97...
Page 99: ...98...
Page 100: ...99...
Page 101: ...100...
Page 102: ...101...
Page 103: ...102...
Page 104: ...103...
Page 105: ...104...
Page 106: ...105...
Page 107: ...106...
Page 108: ...107...
Page 109: ...108...
Page 110: ......