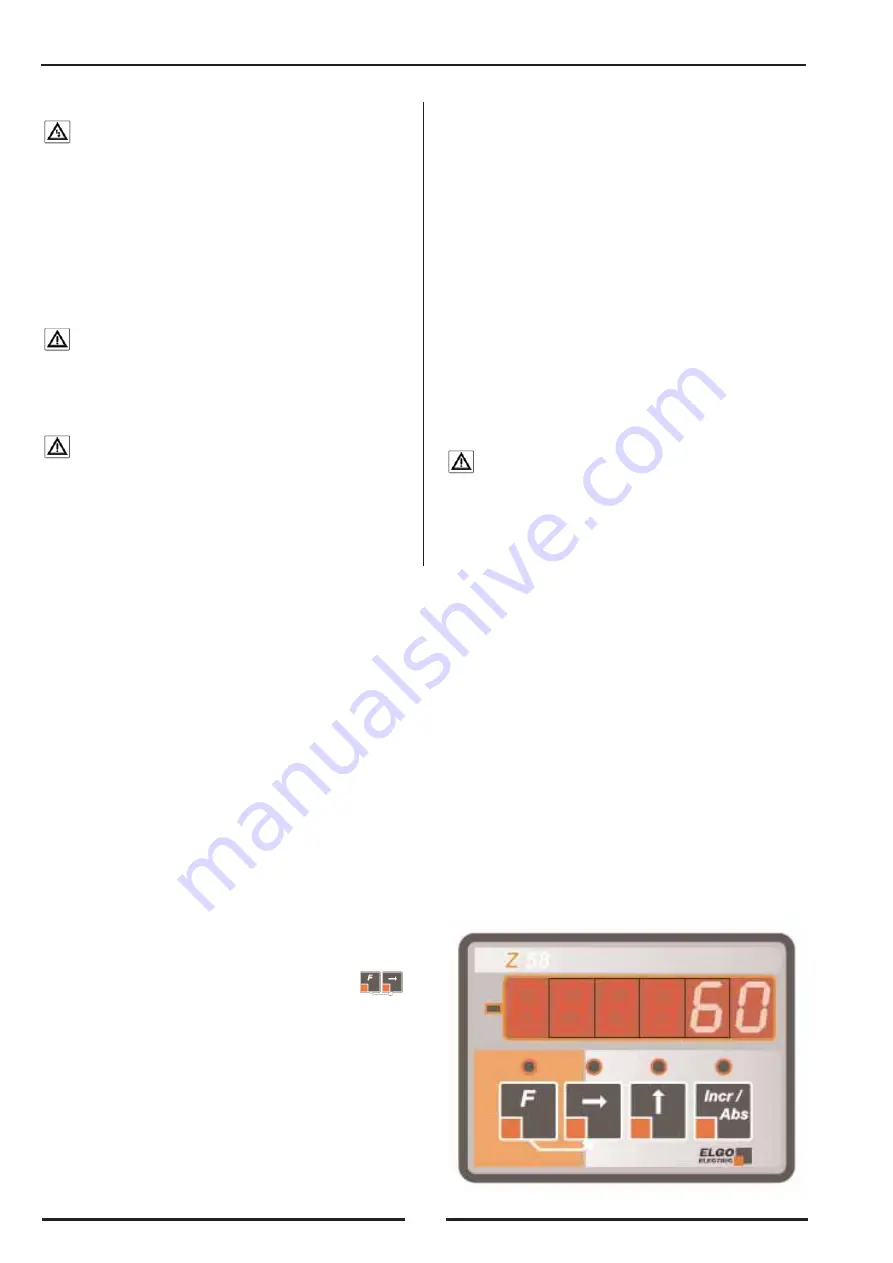
26
Feed Line Checking
Make a regular check of the following items at least once a week:
power line integrity • intactness of line connections and pull relief.
Inspections and checks of electric appliances are subject to valid legal
regulations of the respective country.
Machine Cleaning
Clean the machine thoroughly at regular intervals (always after the shift or
during the shift, if required). Use appropriate cleaning agents. Do not use
solvents (e.g. nitrosolvents). Do not use compressed air for cleaning the
machine! Otherwise the fine chips and impurities will penetrate under the
sliding elements or the persons’ health may be endangered by air-borne
particles.
Metal Chips Removal / Disposal
Observe the instructions and recommendations concerning safe
disposal of waste produced during operation.
Correct cutting angles will be achieved when the bearing surfaces for the
workpiece and the surfaces of gripping jaws are free from metal chips or
other impurities.
Cooling System Cleaning
When coolants are handled, the exposure to dangerous substan-
ces cannot be excluded. Observe in your own interest the
instructions and recommendations (operating instructions of profes-
sional associations or your company referring to safe coolant hand-
ling).
The coolant tank can be removed from the machine base for cleaning and
maintenance. The pump is restricted by the length of the connecting cable).
Warning: The used up coolant is special waste!
Our recommendation:
Regular cleaning and maintenance of the cooling
system extend the life and the functionality of the coolant pump. Coolants
miscible with water, non irritating the skin, highly ageing and corrosion
resistant should be used. Oil content in the coolant should be checked at
least once a week. Good lubrication increases the productivity of cutting.
Integrated in the coolant tank is a setting tank, which should be checked in
the course of routine checks depending on the material cut.
Hydraulic Unit
The hydraulic unit is maintenance-free. The Pilous band saws are filled
with PARAMOL HM 46 oil. The exchange of the oil charge is recommen-
ded within 5000 operating hours. The oil level in the oil level gauge on the
hydraulic unit in the machine base should be consequently checked.
Lubrication
Regular lubrication and cleaning extend the life and the reliability of per-
formance of the machine. While making routine checks, make sure there is
sufficient grease on the vice friction surfaces and the trapezoidal screw and
on the friction surfaces of the saw blade moving bar. Make sure that the
measuring bar, the guide bars of the moving vice as well as the vice are tho-
roughly lubricated (see figure). Add grease, if necessary.
8.2. Repairs
Caution - danger of injury!
Carry out repairs only when the master switch is off or secured
against switching, or when the machine is isolated from the supply and
secured against restarting. We recommend to contact an authorized
service center.
Extra accessorie angle calibration
The button TOTAL STOP is unlocked. Switch on the MASTER SWITCH
and active the machine with the HYDRAULIC UNIT button.
Set cutting angle to +60° (right). At the same time press buttons
and angle calibration of LG380, 400, 500 is done.
Summary of Contents for 20875-0204
Page 5: ...4 ARG 380 Plus S A F ARG 500 Plus S A F...
Page 35: ...34 ARG 380 Plus S A F ARG 500 Plus S A F...
Page 65: ...64 ARG 380 Plus S A F ARG 500 Plus S A F...
Page 92: ...91...
Page 93: ...92...
Page 94: ...93...
Page 95: ...94...
Page 96: ...95...
Page 97: ...96...
Page 98: ...97...
Page 99: ...98...
Page 100: ...99...
Page 101: ...100...
Page 102: ...101...
Page 103: ...102...
Page 104: ...103...
Page 105: ...104...
Page 106: ...105...
Page 107: ...106...
Page 108: ...107...
Page 109: ...108...
Page 110: ......