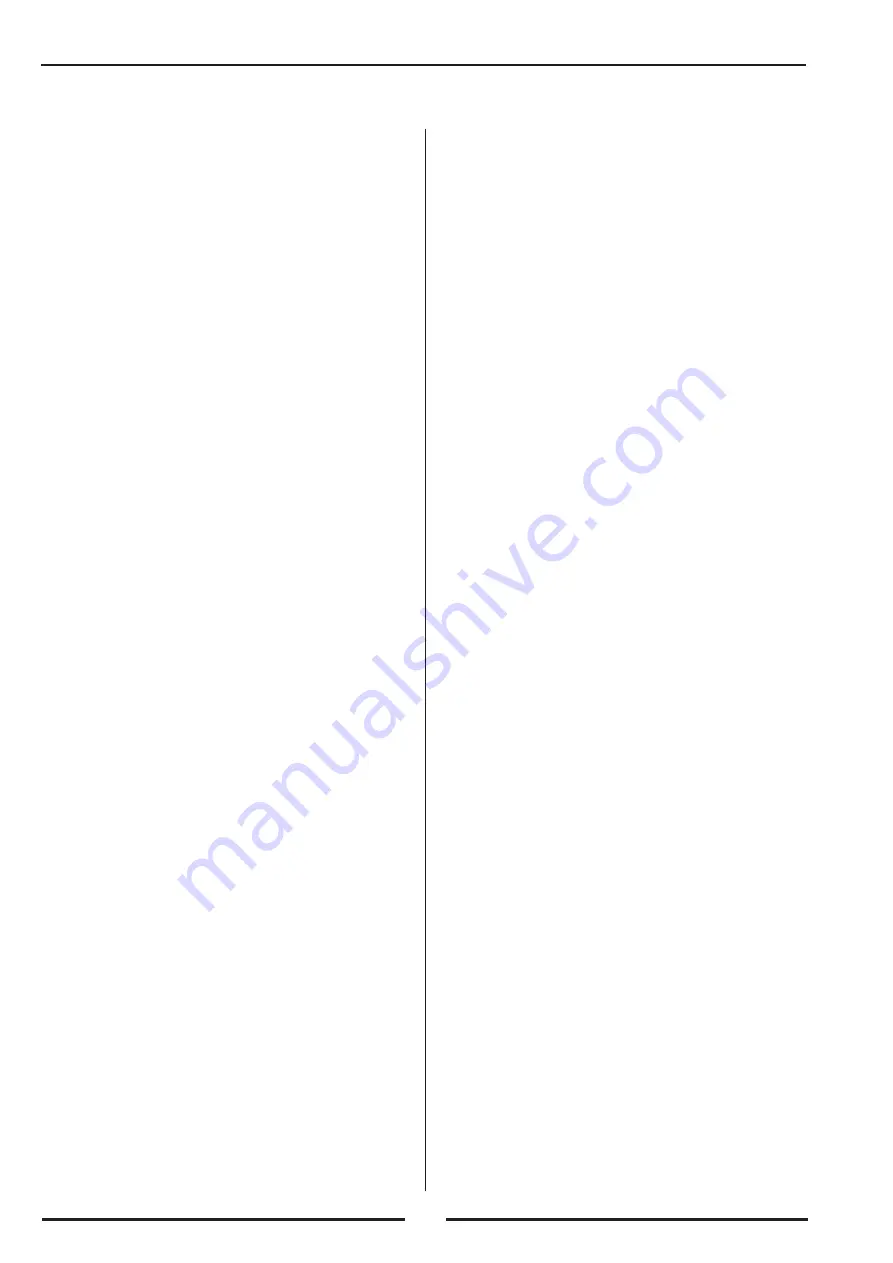
28
Principles of Hydraulic Unit Assembly and Maintenance
The following principles must be adhered to during assembly of hydraulic
circuit sub-assemblies, elements and piping. The basic rule is cleanliness
and good order! The hydraulic circuit consists of very precise elements and
it is very difficult, tough and costly to remove any contamination and its
consequences. Inappropriate storage or failure to renew the rust protection
of hydraulic elements causes locking of internal moving parts of the ele-
ments. The element must be washed with a suitable degreasing agent
(petrol, etc.) and the oil film must be renewed. Read through the manufac-
turer's documentation containing the instructions concerning the method of
assembly, the torque of bolts, etc. All the hydraulic circuit components
must be mounted without force. When lifting the hydraulic units and sets,
make sure they are protected against mechanical damage by the binding
equipment. Hydraulic element guards (transport plates on bearing surfaces,
plugs in threaded chambers) should be removed immediately before
assembly.
Electrical Installation
Electrical installation, electromagnet and control element leads (electro-
magnets) must comply with the valid regulations and standards, especially
CSN 33 2200 and CSN 34 5611. Check the plate or catalogue operational
voltage and frequency values with regard to the network values before
making the connection to the electric network. Protection against dange-
rous touch voltage must comply with CSN 34 1010, according to which the
entire equipment must, among others, be properly earthed. The earth con-
nection (interconnection of the equipment with the earthing system or the
neutral conductor) is carried out by the earthing screw provided on one leg
of the unit tank. The nut welded to the tank is provided with the earthing
marking. The regulations stipulated by the CSN 34 3100 must be followed
during attendance and repair of the electrical installation.
Filling Tank with Oil
First, check the inside space of the tank thoroughly. Check the condition of
the oil-resistant coating. Should any flaking or poor quality manifest them-
selves, remove the coating with an appropriate solvent, wash, dry and clean
with pressure air. In this way, failures caused by poor-quality coating,
which contaminates the entire hydraulic system, will be prevented. On
principal, only oil recommended by the equipment manufacturer may be
filled in. Never make the filling directly from barrels. Always use a filter
unit with filters 25 mm and better. The proven method is using two filters
with different filtering property. The first coarse filter with a metal sleeve,
the other one fine with a paper sleeve. The work will be facilitated and
achieve better quality if the filters are provided with signaling of clogging.
What should be done before putting hydraulic unit into opera-
tion after repair.
Make sure that
• the tank has been filled with the prescribed pure oil up to the upper limit;
• all pipelines have been thoroughly cleaned, the connections properly
tightened and the pipeline assembled without internal strain;
• all pipe unions and elements have been properly mounted and tightened
by the specified torque and the assembled connection corresponds to the
hydraulic diagram;
• alignment and axial clearance have been adhered to when the couplings
between motors and hydrogenerators and/or hydromotors and other
equipment have been mounted;
• the electric motor has been correctly connected (D or Y), the sense of
rotation adhered to and the level, pressure and temperature sensors fun-
ction properly;
• the filters (sleeves) have the specified filtration values and are mounted
in the correct flow direction and filled with oil identical to the tank oil,
and the inside space of the piston hydrogenerators is filled with oil.
Putting the Equipment into Operation
• start the hydrogenerator within short intervals,
• check the piping for noise and leakage,
• vent the hydraulic circuit,
• check the circuit functions with minimum load, if possible,
• gradually increase the pressure to the specified operating value; at the
same time, adjust the control elements, such as control valves, etc.,
• monitor the gauges and measuring devices, noise, oil level and tempera-
ture in the tank,
• follow the instructions of the individual operating manuals.
Putting out of Operation
• tighten all connections.
Restarting
• check oil level,
• test all functions simultaneously; compare the values measured to valu-
es specified,
• check the signaling of pressure gradient on filters.
Brief survey of defects,
which can occur on a hydraulic device. An open
circuit consisting of standard components is considered.
I. The hydrogenerator does not supply oil
a) reversed sense of rotation of hydrogenerator,
b) not sufficient oil in tank,
c) suction piping closed,
d) suction piping leakage,
e) zero geometrical volume set with control hydrogenerator,
f) oil viscosity does not comply with the specified value,
g) hydrogenerator failure.
II. Oil contains air bubbles (pressure aggregate is noisy - hydraulic
device running is unsteady)
a) the new circuit has not been sufficiently vented,
d) suction piping leakage,
c) suction piping is not fully immersed in oil,
d) circulating oil is not fed under the level and entrains air,
e) hydrogenerator shaft sealing is damaged,
f) incorrect design of suction piping big negative pressure in suction part
(cavitation),
g) temperature too low for the specified oil,
III. Increased mechanical noise
a) drive is not trued up,
b) drive coupling damaged,
c) damaged or ruined bearings,
d) damaged rubber mounting of drive equipment,
e) air infiltration.
IV. Hydrogenerator supplies oil but pressure does not increase
a) hydraulic circuit unloaded,
b) safety valve defect,
c) pressure manifold connected to drain, probably in distributor,
d) hydrogenerator functional surfaces are worn,
e) hydraulic unit leakage portion of oil leaks outside the working space.
V. Increase of hydrogenerator loss flow (refers also to rotating
hydromotor)
a) degree of hydrogenerator functional surface wear and tear is high due to
the influence of impurities contained in oil,
b) low viscosity superheated oil,
c) mechanical failure of hydrogenerator.
VI. Hydrogenerator has seized
d) the basic parameters overload have not been adhered to,
b) damage due to cavitation,
c) damage by solid particles contained in oil,
d) the specified oil viscosity has not been adhered to,
e) inappropriate kind of oil,
f) hydrogenerator life has been exceeded,
g) permissible radial and thrust forces at the output shaft have been excee-
ded.
VII. Overheating of oil in tank
a) efficiency has decreased due to wear and tear; loss flow of hydrogene-
rator has sufficiently increased; a portion of energy supplied changes to
heat,
b) some of the elements is leaking, portion of pressure oil flows to drain,
c) tank capacity is small, the heat exchanging surface is insufficient,
d) external source of heat,
e) element base in circuit is inappropriately designed.
VIII. Hydraulic circuit does not comply with designed parameters
a) hydrogenerator flow does not comply with the original calculation,
b) two or more functions take place at the same time,
c) hydraulic device is undersized or oversized,
d) increased pressure loss of piping,
b) some of the elements is leaking, portion of pressure oil flows to drain,
f) gradual fouling of pressure filter.
ATTACHMENT TO OPERATING INSTRUCTIONS FOR HYDRAULIC UNIT
Summary of Contents for 20875-0204
Page 5: ...4 ARG 380 Plus S A F ARG 500 Plus S A F...
Page 35: ...34 ARG 380 Plus S A F ARG 500 Plus S A F...
Page 65: ...64 ARG 380 Plus S A F ARG 500 Plus S A F...
Page 92: ...91...
Page 93: ...92...
Page 94: ...93...
Page 95: ...94...
Page 96: ...95...
Page 97: ...96...
Page 98: ...97...
Page 99: ...98...
Page 100: ...99...
Page 101: ...100...
Page 102: ...101...
Page 103: ...102...
Page 104: ...103...
Page 105: ...104...
Page 106: ...105...
Page 107: ...106...
Page 108: ...107...
Page 109: ...108...
Page 110: ......