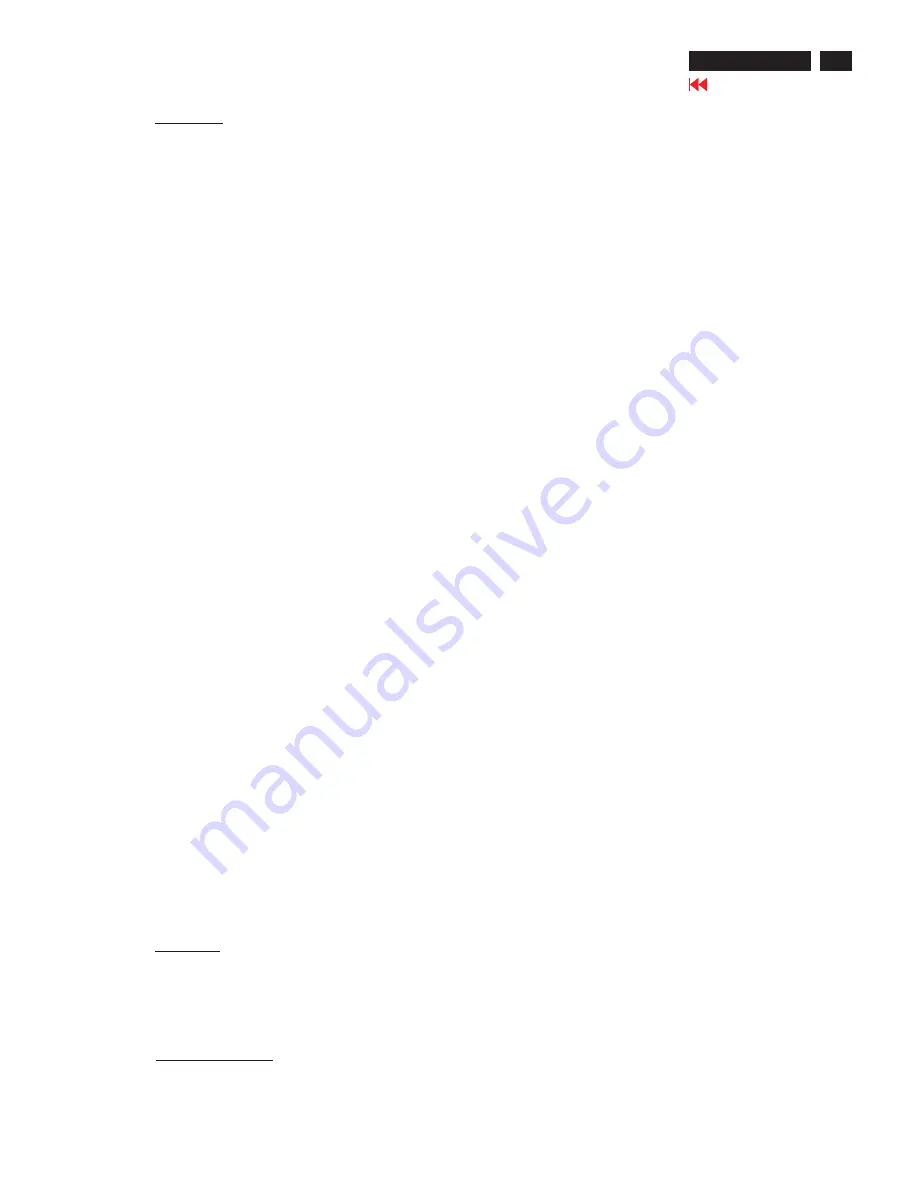
Go to cover page
202P7 CRT
5
Electrical Instructions
1.
General point
1.1
During the alignment and measurement supply a distortion free
AC-mains voltage to the apparatus via an isolating transformer
with a low internal resistance.
1.2
All voltages have to be measured or applied with respect to
ground,unless otherwise stated.
Note: Don't use heatsink as ground.
1.3
The term "Linear RGB" is meant the 0.7Vpp video with separate
sync. (TTL level).The factory preset timing formats from pattern
generator "CHROMA- 2250" are shown in TABLE 1 to 36.
1.4
Any external voltage source should have low internal impedance.
1.5
The alignment has to be done in room temperature 25
±
5
°
C.
1.6
Digital control buttons for
OSD MENU:
Language
-Language: multi-language (8 languages)
Input
-Input signal selection
Zoom
- Zoom
Adjust horizontal
-Adjust position
-Adjust size
Adjust vertical
-Adjust position
-Adjust size
Adjust shape
-Adjust side curve
Pincushion
Balanced
-Adjust side angles
Trapezoid
Parallelogram
-Rotate image
Rotate
Adjust color
-9300
°
K for general use
-6500
°
K for image management
-5500
°
K for photoretouch
-sRGB
-Smart mode
-Professional mode
Reset to factory settings
- No
-Yes
Extra Controls
-Adjust moire
Horizontal
Vertical
-Degauss
-Adjust convergence
Horizontal
Vertical
-Adjust purity
NS purity
-Auto calibrate OFF AUTO
2.
Pre warm-up
2.1
Align in pre-warmed condition at least 30 minutes during
manufacturing.
2.2
Warm up the monitor by pushing power switch and OSD key
3.
Main-chassis alignment
3.1
Power supply adjustment
3.1.1
To preset potmeter R3157 (B+) and R3698 (EHT) to center
position.
3.1.2
Set VG2 (screen) to fully anti-clockwise (zero beam current).
3.1.3
To apply a 69KHz/85Hz cross hatch signal.
3.1.4
Adjust R3157 (B+) to obtain 230 V +/- 0.5 VDC across C2131.
4.
H-deflection supply voltage adjustment
4.1
Apply a 69 kHz / 85Hz signal.
4.1.1
Adjust R3698 (EHT) to obtain 27.0 +/- 0.2kV at CRT anode at
zero beam current for SDI 21" DFT tube. Glue fix the R3698VR.
4.1.2
Monitor the following auxiliary voltages.
+ 8.0V
SOURCE ACROSS C2362 +
8.0V +/- 0.5 VDC
+ 5.0V
SOURCE ACROSS C2143 +
5.0V +/- 0.5 VDC
+ 12.0V SOURCE ACROSS C2361 + 12.0V +/- 0.5 VDC
+ 15.0V SOURCE ACROSS C2134 + 15.1V +/- 1.0 VDC
- 15.0V SOURCE ACROSS C2137 - 15.4V +/- 1.0 VDC
+
6.3V SOURCE ACROSS D6143 +
6.1V +/- 0.5 VDC
+230.0V SOURCE ACROSS C2131 + 230.0V +/- 0.5 VDC
+ 80.0V SOURCE ACROSS C2133 + 82.0V +/- 2.0 VDC
5.
General conditions for alignment
5.1
During all alignments, supply distortion free AC mains
voltage to set via an isolating transformer with low internal
impedance.
5.2
All measurements are carried out at nominal mains voltage,
unless otherwise stated.
5.3
Align in pre-warmed condition, at least 30 minutes
warm-up with nominal picture brightness.
5.4
Purity, convergence, geometry and subsequent alignments
should be carried out in magnetic cage with correct magnetic
field.
Northern hemisphere: H = 0, V = 430mG, Z = 0 .
Southern hemisphere: H = 0, V = - 520mG, Z = 0 .
Equatorial Support
: H = 0, V =
0 mG,
Z = 0.
5.5
All voltages are to be measured or applied with respect to
ground,unless otherwise stated.
Note: Do not use heatsink as ground.
5.6
Any external voltage sources should have a low internal
impedance.
5.7
Adjust function controls to center position except for contrast
control which should be set to MAX.
5.8
The white balance and purity has to be adjusted in subducted
lighted room.
5.9
All alignments have to be done in a room with a temperature
of 25 +/- 5
°
C.
5.10
Adjust picture tilt for correct TOP/BOTTOM lines Via I2Cbus.
(Picture tube should be mounted without tilt CRT cabinet)
5.11
All the alignment can be done only when set is working
in 'factory mode' - pressing the 'Right' and 'left' keys together
while power on the test set, or by CAA test controller.
Prepare the test set in 'factory mode' before the set alignment.
6.
X-ray protection adjustment
6.1
Set the brightness and contrast controls to minimum. Connect
EHT meter
the high tension cap of CRT, set X-ray adj. R3695 to maximum
activation voltage(fully clockwise, viewing from component side)
and then turn on the set.
Summary of Contents for 202P70/00
Page 37: ...37 202P7 CRT Go to cover page Wiring Diagram ...
Page 41: ...41 202P7 CRT Go to cover page Main Board C B A 1 ...
Page 42: ...42 Main Board C B A 2 Go to cover page 202P7 CRT ...
Page 44: ...44 Go to cover page Video Board C B A 1 202P7 CRT ...
Page 45: ...45 202P7 CRT Go to cover page Video Board C B A 2 ...
Page 47: ...47 202P7 CRT Go to cover page TERMINAL Board C B A 1 ...
Page 48: ...48 TERMINAL Board C B A 2 Go to cover page 202P7 CRT ...
Page 50: ...50 Driver Board C B A Go to cover page 202P7 CRT ...
Page 51: ...51 202P7 CRT Go to cover page KEY CONTROL Schematic Diagram C B A ...
Page 52: ...52 MHR Schematic Diagram C B A Go to cover page 202P7 CRT ...