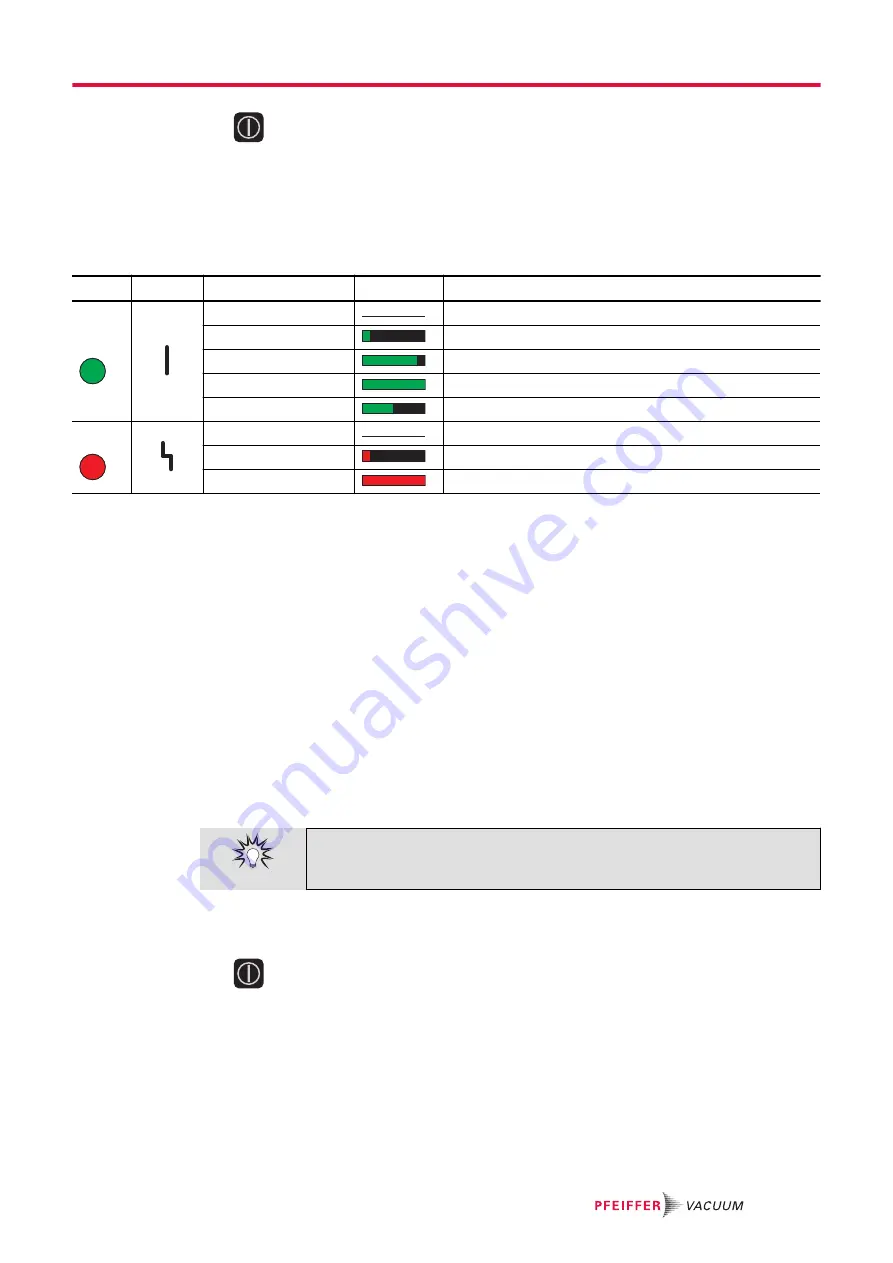
6.
Switch on the turbo pumping station.
6.5 Operation monitoring
6.5.1 Operating mode display via LED
The LEDs on the front panel of the DCU display basic operating statuses.
LED
Symbol
LED status
Display
Meaning
Green
Off
without current
On, flashing
"Pumping station OFF", rotation speed ≤ 60 rpm
On, inverse flashing
"Pumping station ON", set rotation speed not reached
On, constant
"Pumping station ON", set rotation speed reached
On, flashing
"Pumping station OFF", rotation speed > 60 rpm
Red
Off
no error, no warning
On, flashing
Warning
On, constant
Defect
Tbl. 9:
LED display and meaning at the DCU
6.5.2 Temperature monitoring
If threshold values are exceeded, output signals from temperature sensors allow the vacuum pumps to
be brought to a safe condition. Depending on pump type, temperature threshold values for warnings
and malfunction messages are saved unchanged in the electronic drive unit. For information purposes,
various status queries are prepared in the parameter set.
● The drive power of the turbopump is reduced in case of impermissible motor temperature or non-
permissibly high housing temperature. This can cause the motor to fall below the set rotation
speed switchpoint and so result in switching off of the turbopump.
● At a non-permissibly high temperature (> 75 °C) of the backing pump, the motor rotation speed is
reduced to nominal rotation speed to prevent overheating. After cooling down (< 72° C) the back-
ing pump runs at set rotation speed again.
6.6 Switching off and venting
We recommend
Vent the turbopump after shutdown. By doing so, you prevent particles flowing back
into the vacuum system from the fore-vacuum area.
6.6.1 Shutting down the turbo pumping station
Procedure
►
Shut down the turbo pumping station.
– The components shut down according to their configuration. The pumping station remains
ready for operation.
► Shut off the entire current supply at the master switch.
Operation
35/60