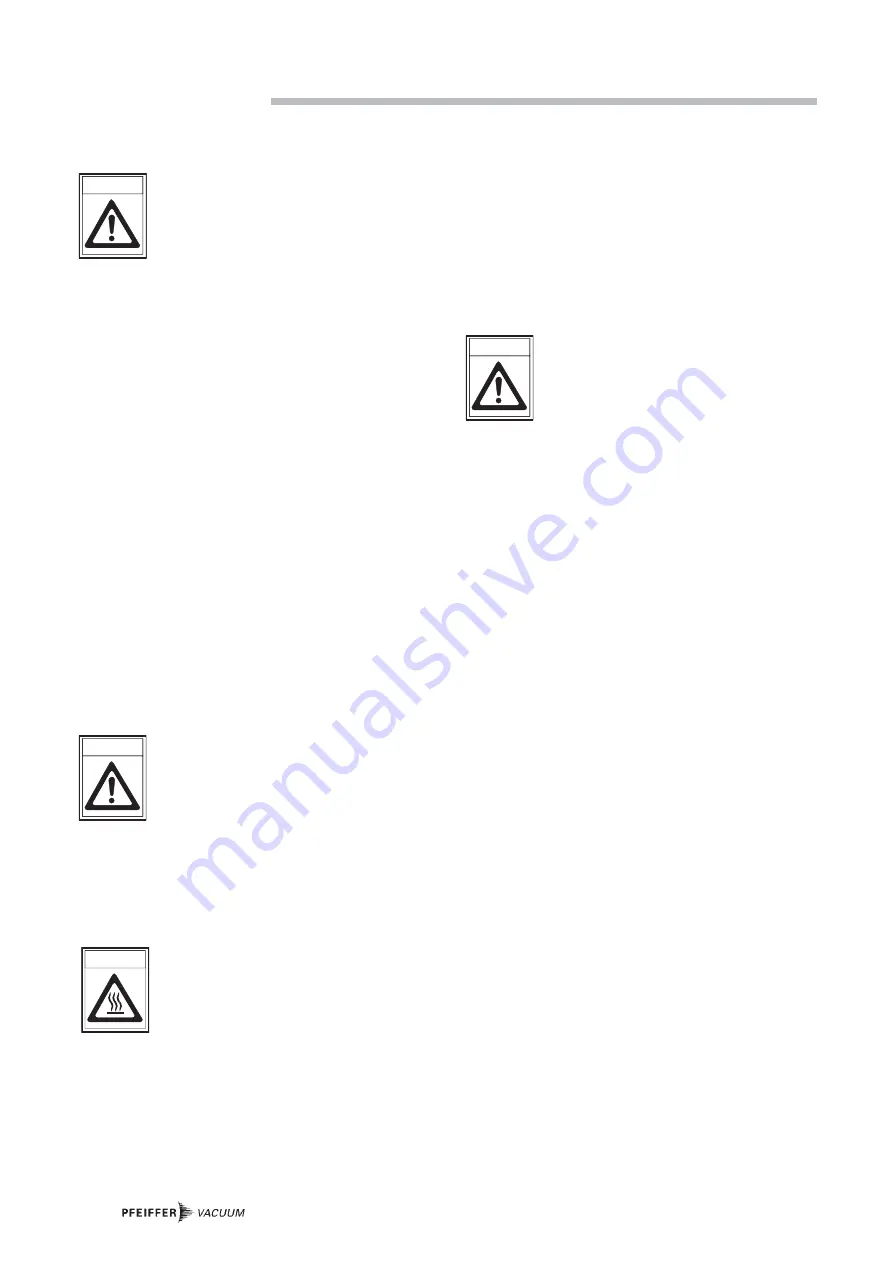
12
➡
Screw in operating fluid drain screw 43.
➡
Allow pump to run for about 10 seconds with open vacuum
flange.
➡
Drain off remaining operating fluid.
➡
In the case of serious contamination, the operating fluid
will have to be changed several times.
➡
Screw in operating fluid drain screw 43 with O-ring.
➡
Fill in fresh operating fluid and check level as per
section 4.1.
Operating fluid can contain substances from
the medium pumped. Operating fluid must be
disposed of in accordance with the local
respective regulations.
Please request safety instruction data sheets for operating
fluids from PFEIFFER or download from the INTRANET/
INTERNET.
6.2. Re-Setting The Silencer
If the silencer 13 is not functioning, a knocking noise
becomes audible at end vacuum. This does not cause dama-
ge to the pump but it may be disturbing in quiet rooms. Setting
can be carried out while the pump is running and the intake
socket and gas ballast valve are closed, using a normal
screwdriver:
➡
The pump must have reached its operating temperature.
➡
Remove locking screw 44 (UNO 120A) or operating medium
filler screw 42 (DUO 120 A).
➡
Using a screwdriver, open the valve spindle 47 approx. 3
turns (flushing) for some seconds and then close it again
completely (clockwise).
➡
Slowly open the valve spindle 47 (1/2 to a complete turn)
until the knocking noise is no longer audible.
➡
Replace locking screw 44 or operating medium filler screw
42 paying attention to the O-ring.
Please note:
Silencer cleaning is described in the service instructions.
WARNUNG
When carrying out servicing work, take the following
precautions:
Always ensure the pump cannot be switched
on when carrying out any work on the pump. If
necessary, remove the pump from the system
to carry out inspection work.
➡
Only dismantle the pump as far as is necessary in order to
repair defects.
➡
Dispose of used operating fluid in compliance with local
regulations.
➡
When working with synthetic operating media, toxic
substances and substances contaminated with corrosive
gases, the relevant instructions governing their use must
be observed.
➡
Only use benzine or similar agents for cleaning pump
parts. Do not use soluble cleaning agents.
6.1. Changing The Operating Fluid
The rate of deterioration of the operating fluid depends on the
pump applications.
➡
The level of deterioration of organic operating fluids (for
example P3) can be read off from the colour scale in
accordance with DIN 51578 on the supplementary sheet
PK 800 219 BN/B, on request.
– The colour scale enables precise colour determination.
➡
Fill a specimen in a test tube or some similar vessel and
test by holding against the light.
➡
Where the discolouration is dark yellow to red brown
(equivalent to 4 ... 5 on the scale) change operating fluid.
Where organic operating fluids, for example P3,
are involved, the operating fluid should be
changed at least once a year!
Replacing The Operating Fluid
➡
Switch off the pump.
➡
Unscrew operating fluid drain screw 43 and drain
operating fluid.
The operating fluid temperature can be as high
as 80 °C. During maintenance and repair work,
process related toxic gases and vapours can
escape from the operating fluid which may
become contaminated with harmful substances
(radioactive, chemical etc.).
Disposal of used operating fluid is subject to the relevant
regulations.
WARNING
CAUTION
WARNING
6. Maintenance