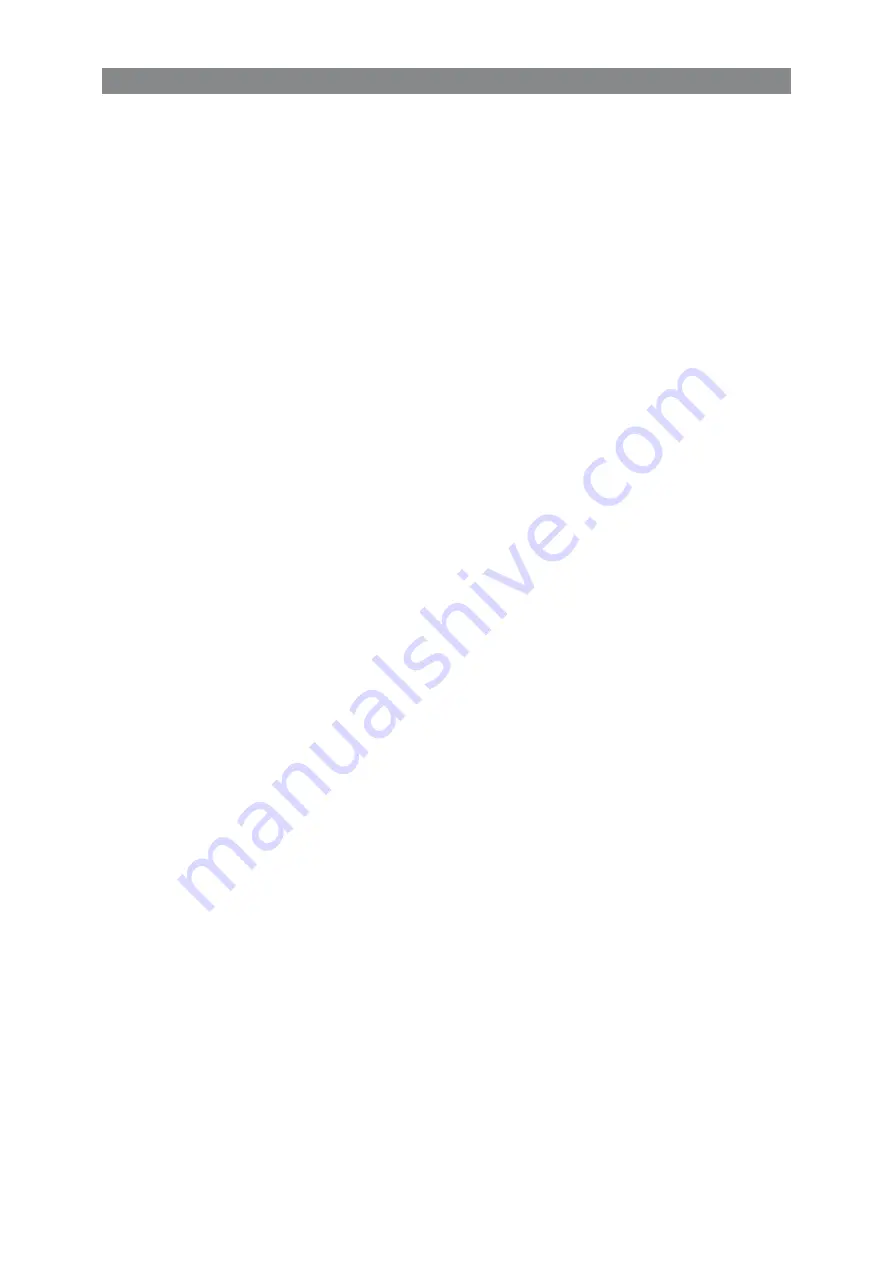
54
Trouble Shooting guide
Troubleshooting R-net
3.1
Joystick Error
The commonest cause for this error is that the joystick was moved away from its central position before
and during the time at which the control system was switched on. The screen for a shifted joystick is
displayed for 5 seconds. If the joystick is not released during this time, a joystick error is registered. Even
if an error screen is not displayed, the error and the number times it arises is registered in the system log.
• Ensure that the joystick is in the central position and start up the control system.
If the error persists, the joystick or joystick module may be defective. Read more in section 5.
3.2 Low Battery
This occurs when the control system detects that the battery voltage is lower than 16 V.
• Check the batteries and their connection to the control system.
If the error persists after the batteries and connections have been checked, the power module may be
defective. Read more in section 5.
3.3 High Battery
This occurs when the control system detects that the battery voltage is higher than 35 V. The commonest
causes for this error are that the battery has been overcharged or a poor connection between the control
system and the batteries.
• Check the batteries and their connection to the control system.
If the error persists after the batteries and connections have been checked, the power module may be
defective. Read more in section 5.
3.4 Brake Error
This occurs when the control system detects a problem in the solenoid brakes or the connections to
them.
1505 -
M1 Brake Error
1506 -
M2 Brake Error
• Check the solenoid brakes, their cables and the connections to the control system.
If the error persists after the checks listed above, the power module may be defective. Read more in
section 5.
3.5 Motor Error
This occurs when the control system detects that a motor has been disconnected.
3B00 -
M1 Motor Error
3C00 -
M2 Motor Error
• Check the motors, their cables and the connections to the control system.
If the error persists after the checks listed above, the power module may be defective. Read more in
section 5.
3.6 Inhibit active
This occurs when one of the inhibit signals is active and is in blocked mode.
The last two digits of the error code indicate the active inhibit signal. The code is hexadecimal.
1E01 -
For inhibit signal 1.
1E09 -
For inhibit signal 9.
1E0A -
For inhibit signal 10.
• Cycle the voltage. This will deactivate the block mode, which may remedy the error.
• Check all connections and switches for the indicated inhibit signals.
Summary of Contents for C500
Page 1: ...SERVICE MANUAL Permobil C500 Power wheelchair US ...
Page 2: ......
Page 62: ...62 Cabling overview A B C D E F 1 2 3 4 ...
Page 63: ...63 Innehåll Cabling overview Cabling overview A B C D E F 5 6 7 8 ...
Page 64: ...64 Notes ...
Page 66: ......
Page 67: ......