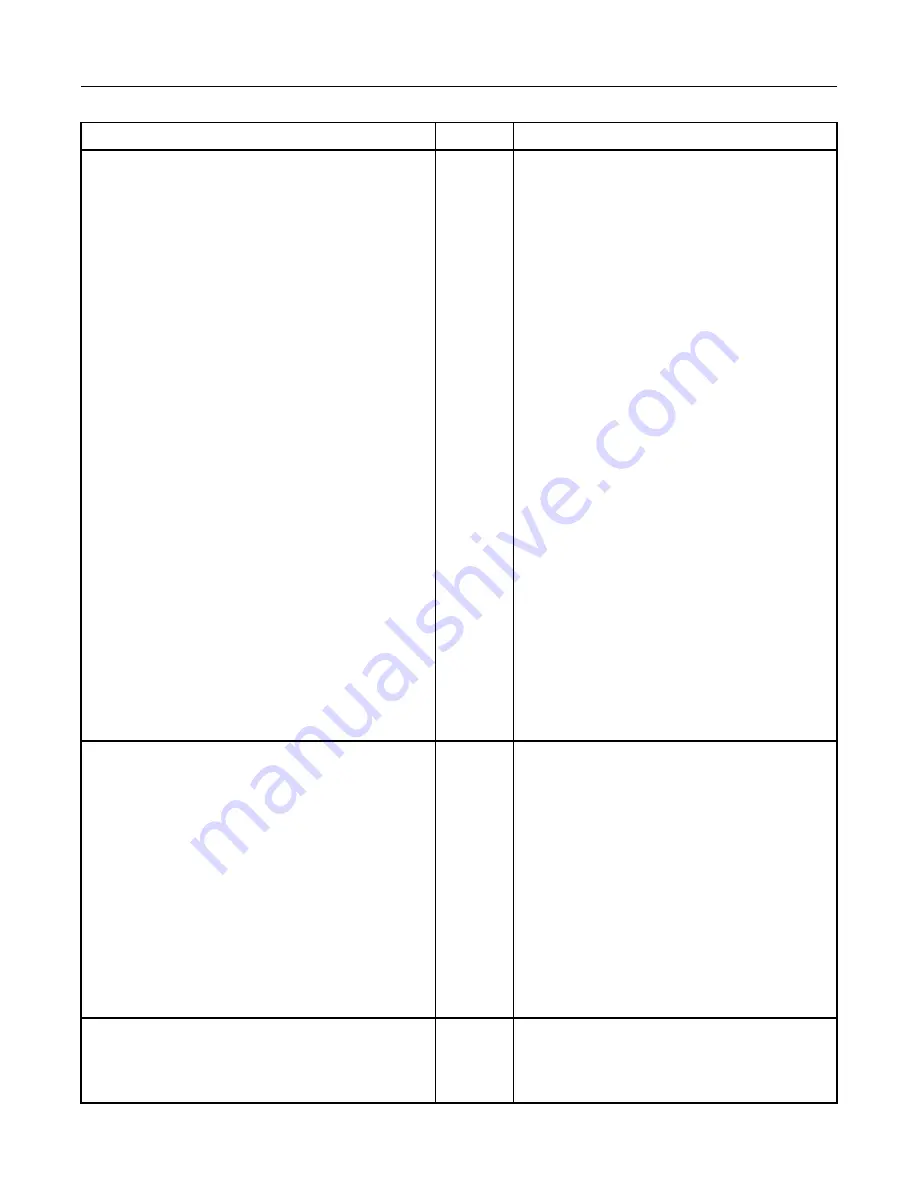
Table 116
Troubleshooting Test Steps
Values
Results
1. Check Connectors for Moisture and Corrosion
A. Inspect all the harnesses. Ensure that the routing of the wiring
harness allows the wires to enter the face of each connector at a
perpendicular angle. Otherwise, the wire will deform the seal bore.
This will create a path for the entrance of moisture. Verify that the
seals for the wires are sealing correctly.
B. Ensure that the sealing plugs are in place. If any of the plugs are
missing, replace the plug. Ensure that the plugs are inserted cor-
rectly into the connector.
C. Disconnect the suspect connector and inspect the connector
seal. Ensure that the seal is in good condition. If necessary, replace
the connector.
D. Thoroughly inspect the connectors for evidence of moisture
entry.
Note:
It is normal to see some minor seal abrasion on connector
seals. Minor seal abrasion will not allow the entry of moisture.
If moisture or corrosion is evident in the connector, the source of
the moisture entry must be found and the source of the moisture
entry must be repaired. If the source of the moisture entry is not re-
paired, the fault will recur. Simply drying the connector will not recti-
fy the fault. Check the following items for the possible moisture
entry path:
·
Missing seals
·
Incorrectly installed seals
·
Nicks in exposed insulation
·
Improperly mated connectors
Moisture can also travel to a connector through the inside of a wire.
If moisture is found in a connector, thoroughly check the connector
harness for damage. Also check other connectors that share the
harness for moisture.
Note:
The ECM is a sealed unit. If moisture is found in an ECM
connector, the ECM is not the source of the moisture. Do not re-
place the ECM.
Harness,
connectors,
and seals are
OK.
Result:
A fault has been found with the harness or the
connectors.
Repair the connectors or the wiring, as required. Ensure that
all of the seals are correctly installed. Ensure that the con-
nectors have been reattached.
If corrosion is evident on the pins, sockets or the connector,
use only denatured alcohol to remove the corrosion. Use a
cotton swab or a soft brush to remove the corrosion.
If moisture was found in the connectors, run the engine for
several minutes and check again for moisture. If moisture re-
appears, the moisture is wicking into the connector. Even if
the moisture entry path is repaired, it may be necessary to re-
place the wires.
Use the electronic service tool in order to clear all logged di-
agnostic codes and then verify that the repair eliminates the
fault.
Result:
The harness, connectors, and seals are in good
condition.
Proceed to Test Step 2.
2. Check the Wires for Damage to the Insulation
A. Carefully inspect each wire for signs of abrasion, nicks, and
cuts.
Inspect the wires for the following conditions:
·
Exposed insulation
·
Rubbing of a wire against the engine
·
Rubbing of a wire against a sharp edge
B. Check all of the fasteners for the harness and the strain relief
components on the ECM in order to verify that the harness is cor-
rectly secured. Also check all of the fasteners in order to verify that
the harness is not compressed. Pull back the harness sleeves in
order to check for a flattened portion of wire. A fastener that has
been overtightened flattens the harness. This damages the wires
that are inside the harness.
The wiring is
OK
Result:
There is damage to the harness.
Repair the wires or replace the wires, as required.
Use the electronic service tool in order to clear all logged di-
agnostic codes and then verify that the repair eliminates the
fault.
Result:
The wires are free of abrasion, nicks, and cuts and
the harness is correctly clamped.
Proceed to Test Step 3.
3. Inspect the Connector Terminals
Terminals are
aligned and
undamaged
Result:
The terminals of the connector are damaged.
Repair the terminals and/or replace the terminals, as
required.
(continued)
244
UENR0612
This document has been printed from SPI2. NOT FOR RESALE