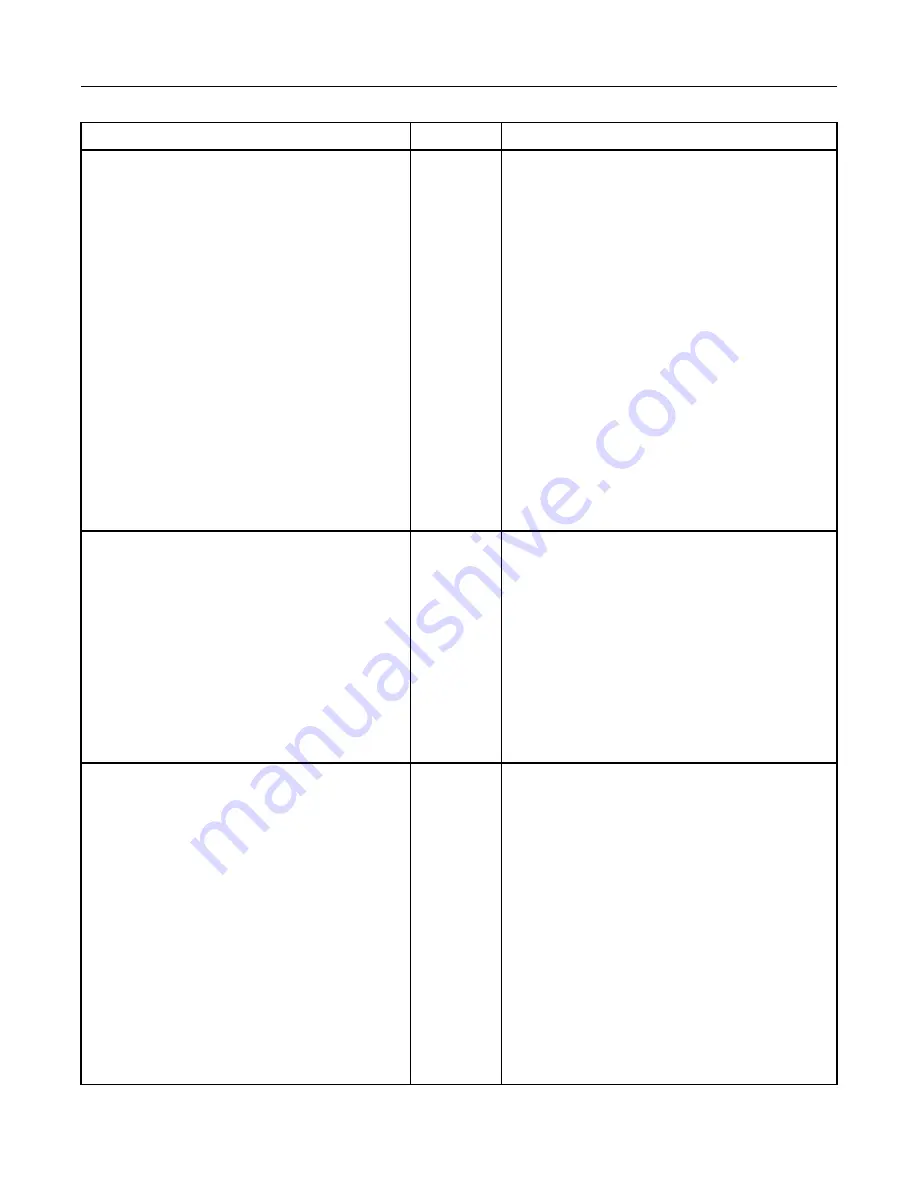
Table 102
Troubleshooting Test Steps
Values
Results
1. Inspect Electrical Connectors and Wiring
A. Turn the keyswitch to the OFF position.
B. Inspect the connectors for the speed/timing sensors. Refer
to Troubleshooting, “Electrical Connectors - Inspect”.
C. Perform a 30 N (6.7 lb) pull test on each of the wires in the
suspect sensor connector and the sensor connections at the
ECM.
D. Check that the ground connection on the ECM and the neg-
ative terminal on the battery are correctly installed.
E. Check the ground connection on the ECM for abrasions
and pinch points.
F. Check the harness for abrasion and pinch points from the
suspect sensor to the ECM.
G. Check that the suspect sensor is installed correctly. Check
that the suspect sensor is fully seated into the engine. Check
that the sensor is securely latched.
Damaged wire
or connector
Result:
A damaged wire or damaged connector was found.
Repair the damaged wire or the damaged connector.
Use the electronic service tool to clear all logged diagnostic co-
des. Verify that the repair eliminates the fault.
Result:
All connectors, pins, and sockets are correctly con-
nected and/or inserted and the harness is free of corrosion, of
abrasion or of pinch points.
Proceed to Test Step 2.
2. Check for Active Diagnostic Codes and Recently
Logged Diagnostic Codes
A. Turn the keyswitch to the OFF position.
B. Connect the electronic service tool to the diagnostic
connector.
C. Turn the keyswitch to the ON position. If the engine will
start, then run the engine.
D. Use the electronic service tool in order to monitor active di-
agnostic codes or recently logged diagnostic codes.
Diagnostic
codes
Result:
Diagnostic code 190-8 is active or recently logged.
Proceed to Test Step 3.
Result:
Diagnostic code 723-8 is active or recently logged.
Proceed to Test Step 5.
Result:
Diagnostic code 637-11 is active or recently logged.
Proceed to Test Step 8.
3. Measure the Signal Frequency at the Sensor Connector
A. Turn the keyswitch to the OFF position.
B. Disconnect the primary speed/timing sensor.
Note:
A multimeter that can measure frequency (Hz) is re-
quired for this procedure.
C. Connect the multimeter to pin 1 and pin 2 on the sensor
connector.
D. Turn the keyswitch to the START position.
E. Record the frequency while the engine is cranking.
At least 100 Hz.
Result:
The measured frequency is less than 100 Hz.
Remove the primary speed/timing sensor. Refer to Disassem-
bly and Assembly, “Crankshaft Position Sensor - Remove and
Install”.
Inspect the primary speed/timing sensor for damage and/or
debris.
If the primary speed/timing sensor is free from damage and/or
debris, install a new primary speed/timing sensor. Refer to Dis-
assembly and Assembly, “Crankshaft Position Sensor - Re-
move and Install”.
Use the electronic service tool in order to clear all logged diag-
nostic codes and then verify that the repair eliminates the fault.
If the primary speed/timing sensor is damaged and/or contami-
nated with debris, proceed to Test Step 9.
Result:
The measured frequency is greater than 100 Hz.
Proceed to Test Step 4.
(continued)
214
UENR0612
This document has been printed from SPI2. NOT FOR RESALE