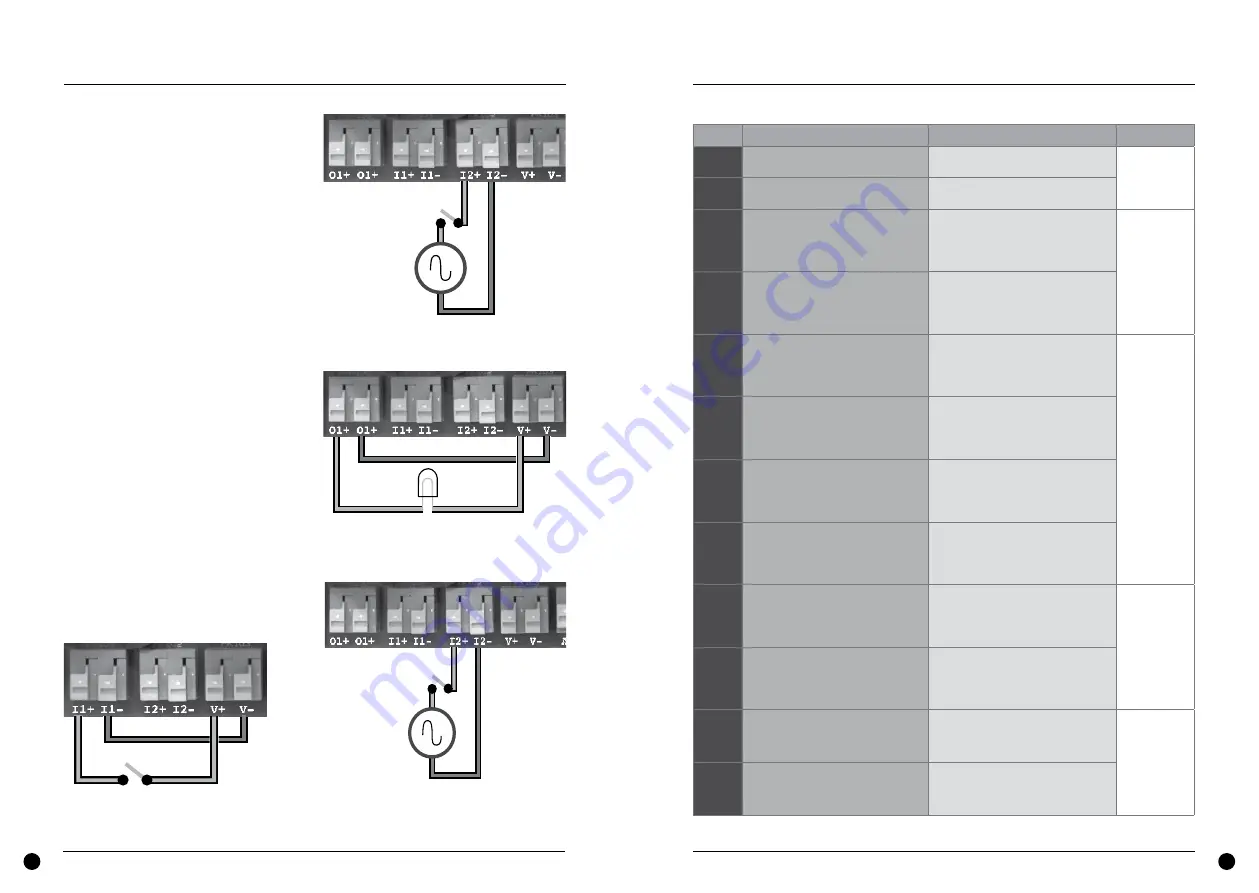
I/O CONNECTIONS
I/O CONNECTIONS
LABEL
FUNCTION
CONNECTION
RATING
AI+
Positive connection for transducer
Red transducer wire
24 Volt
(supplied)
AI-
Negative connection for transducer
Black transducer wire
V+
Positive side of 24 volt power supply.
Used to power external devices.
Positive side of 24V external device,
i.e., flow switch, moisture sensor,
alternator, etc. Need to complete the
circuit with V-. See Figures 15 and 17.
40mA
maximum
output
V-
Negative side of 24 volt power supply.
Used to power external devices.
Typically to I1-, I2-, or O1-. Used with
a flow switch, moisture sensor,
alternator, etc. Need to complete the
circuit with V+. See Figures 15 and 17.
I1+
Positive (dry contacts) connection of
Digital Input 1. Connect when using an
external device to control Drive.
From an external device i.e., flow
switch, moisture sensor, alternator, etc.
Requires complete circuit connection
with I1-. See Figures 15 and 16.
Accepts
24VDC and up
to 230VAC
I1-
Negative (dry contacts) connection of
Digital Input 1. Connect when using an
external device to control Drive.
Can be from V- or from the negative
side of an external power supply.
Requires complete circuit connection
with I1+. See Figures 15 and 16.
I2+
Positive (dry contacts) connection of
Digital Input 2. Connect when using an
external device to control Drive.
From an external device, i.e., flow
switch, moisture sensor, alternator, etc.
Requires complete circuit connection
with I2-. See Figures 15 and 16.
I2-
Negative (dry contacts) connection of
Digital Input 2. Connect when using an
external device to control Drive.
Can be from V- or from the negative
side of an external power supply.
Requires complete circuit connection
with I2+. See Figures 15 and 16.
O1+
Output relay (dry contacts)
connection. Programmed to close
when pump is
Running
or
Faulted
.
Positive wires of an external device.
See Figures 17 and 18.
Accepts up
to 5 Amps at
24VDC and
8 Amps at up
to 230VAC
O1+
Output relay (dry contacts)
connection. Programmed to close
when pump is
Running
or
Faulted
.
Positive wires of an external device.
See Figures 17 and 18.
P
Positive connection of an RS-485
communication device (see Figure 15). Positive wire from RS-485 device.
Per RS-485
Standard
N
Negative connection of an RS-485
communication device (see Figure 15).
Negative wire from RS-485 device.
TABLE 10 - I/O FUNCTION, CONNECTIONS, RATINGS
The I/O terminals are located in the center of
the wiring compartment, as shown previously
in Figure 9.
The Digital Input connections (
I1
and
I2
) are
used to control the Drive based on the state
of an external device, such as a flow switch,
moisture sensor, alternator, or other device.
Programming is needed to activate any of
these functions (see Table 9).
The Output Relay (
O1
) is used to control an
external device based on two states of Drive;
either Running the pump or Faulted.
Programming is needed to activate any of
these functions (see Table 9).
Cable Installation
Three 13mm conduit knockouts are provided
on the bottom of the Drive enclosure for the
I/O wires.
Break out the closest 13mm knockout and route
the wires through. Use a cord grip to prevent
the wire from rubbing and causing a short.
NOTICE
Never run low voltage I/O wire through
the same conduit hole as the 230V input wires
or motor wires.
To connect the external wires to the
terminals:
1. Strip wire 13mm
2. Push spring terminal up with finger
or slotted screwdriver
3. Insert wires from bottom
4. Release spring terminal
Connection Examples
Figures 15-18 show various connection
schemes for typical applications. Table 10
describes each I/O terminal, including purpose
and rating.
6540 0412
Figure 15 - Example Input with internal
24 volt supply
6542 0412
Figure 17 - Example Output relay with internal
24 volt supply
6541 0412
115 VAC
or
230 VAC
+
-
Figure 16 - Example external Input with
external supply
6541 0412
115 VAC
or
230 VAC
+
-
Figure 18 - Example Output with external supply
PENTEK IntelliDrive
™
Owner’s Manual
PENTEK IntelliDrive
™
Owner’s Manual
17
16