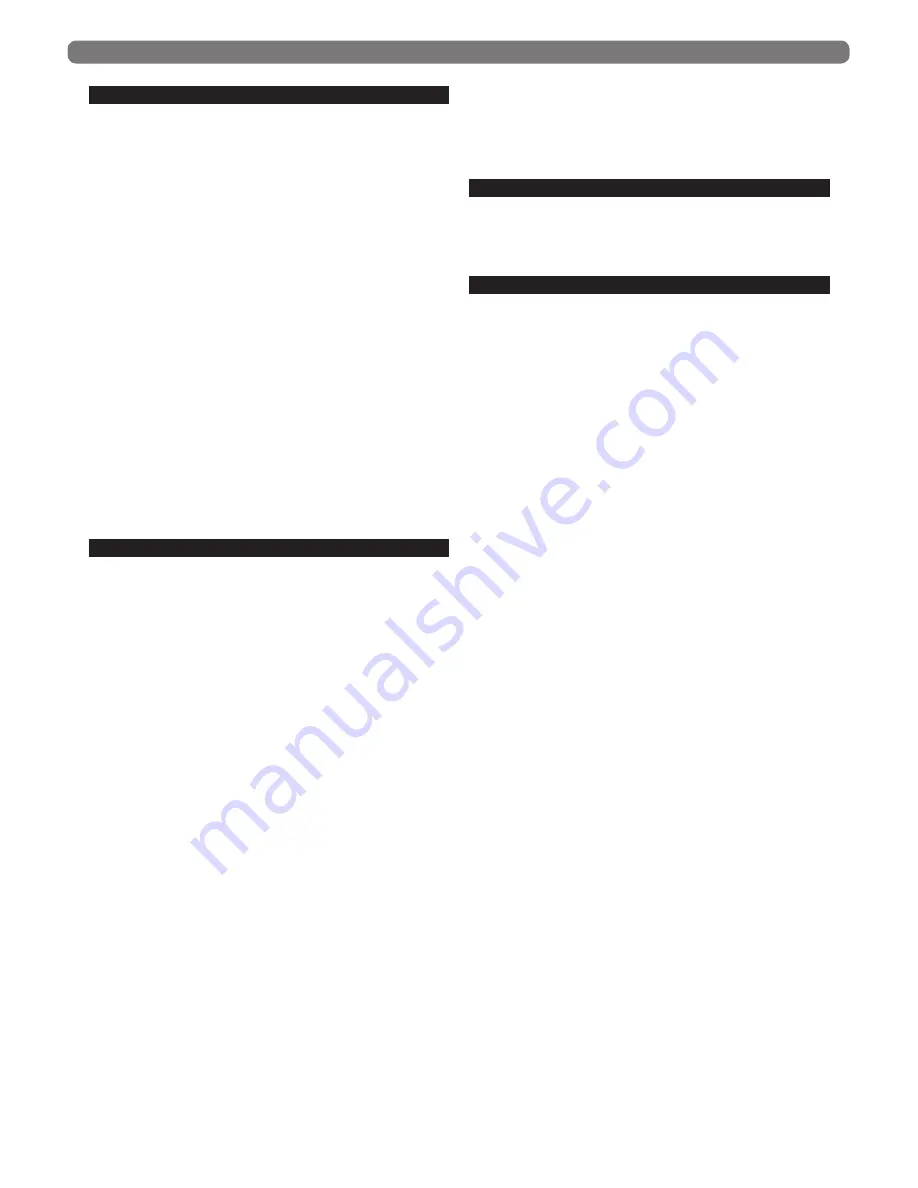
31
A. GENERAL
1. Disconnect this boiler from the gas supply piping
during any pressure testing of the gas system.
2. Check pipes adjacent to cold walls or in unheated
spaces. Insulate and tape them if necessary to be
sure they can’t freeze up. Keeping the water moving
at all times will reduce the likelihood of freezing. See
Section 3 for antifreeze instructions.
3. If there is considerable foreign matter in the boiler
water, the boiler should be shut down and allowed
to cool, then drained and thoroughly flushed out.
Use the drain valve at the bottom of the return
connection to drain the boiler. Pipe the drain cock to
a suitable drain or containment device if antifreeze is
used. Flush the system to remove remaining matter.
See Section 1 - PreInstallation, for water quality
requirements. If there is evidence that hard scale has
formed on the internal surfaces, the boiler should
be cleaned by chemical means as prescribed by a
qualified water treatment specialist.
4. There must not be signs of continuous wetness
at the chimney. If signs of continuous wetness
are observed, a qualified service agency must be
consulted to modify the vent configuration to prevent
the formation of condensate.
B. DAILY (WITH BOILER IN USE)
Daily boiler observation can be performed by the owner.
If any potential problems are found, a qualified installer
or service technician/agency must be notified.
1. Remove any combustible materials, gasoline and
other flammable liquids and substances that generate
flammable vapors from the area where the boiler
is contained. Make certain that the boiler area has
ample air for combustion and ventilation and that
there are no obstructions to the free flow of air to
and from the boiler.
2. Observe general boiler conditions (unusual noises,
vibrations, etc.)
3. Observe operating temperature and pressure on the
combination gauge located on the left side of the
boiler. Boiler pressure should never be higher than
5 psi (34 kPa) below the rating shown on the safety
relief valve [25 psig (172 kPa) maximum for a 30
psig (207 kPa) rating, 45 psig (310 kPa) maximum
for a 50 psig (345 kPa) rating]. The valve rating can
be found on the top of the safety relief valve (see
Figure 3.1 for location of the safety relief valve).
Boiler temperature should never be higher than
250°F (121°C).
4. Check for water leaks in boiler and system piping.
5. Smell around the appliance area for gas. If you
smell gas, follow the procedure listed in the Lighting/
Operating Instructions in Section 8.
C. WEEKLY (WITH BOILER IN USE)
1. Flush float-type low-water cut-off (if used) to remove
sediment from the float bowl as stated in the
manufacturer’s instructions.
D. MONTHLY (WITH BOILER IN USE)
1. Check boiler room floor drains for proper
functioning.
2. Check function of the safety relief valve (monthly
unless specified otherwise by manufacturer) by
performing the following test:
a. Check valve piping to determine that it is
properly installed and supported.
b. Check boiler operating temperature and
pressure.
c. Lift the try lever on the safety relief valve to the
full open position and hold it for at least five
seconds or until clean water is discharged.
d. Release the try lever and allow the valve to close.
If the valve leaks, operate the lever two or three
times to clear the valve seat of foreign matter. It
may take some time to determine if the valve has
shut completely.
e. If the valve continues to leak, it must be replaced
before the boiler is returned to operation.
f. Check that operating pressure and temperature
have returned to normal.
g. Check again to confirm that valve has closed
completely and is not leaking.
3. Test low-water cut-off (if used) as described by the
manufacturer.
4. Test limit as described in Section 8E, “Check-Out
Procedure.”
5. Test function of gas safety shut-off features as
described by gas valve and ignition control
manufacturer.
6. Cycle the boiler at least once and check operation of
the vent damper.
MAINTENANCE
Summary of Contents for Peerless Boilers GM Series
Page 1: ...GM Boilers Series Gas Installation Operation Maintenance Manual...
Page 21: ...19 ELECTRICAL Figure 6 2 Wiring Diagram Spark Ignited Pilot Hydrolevel 3200 Limit control...
Page 25: ...23 Figure 8 3 Operating Instructions Spark Intermittent Ignition START UP PROCEDURES...
Page 26: ...24 START UP PROCEDURES Figure 8 4 Operating Instructions Spark Intermittent Ignition...
Page 38: ...REPAIR PARTS Figure 12 3a Figure 12 3b 36...
Page 40: ...REPAIR PARTS 13 14 15 16 17 24 25 22 21 20 19 18 23 Figure 12 4 38...
Page 42: ...NOTES 40...