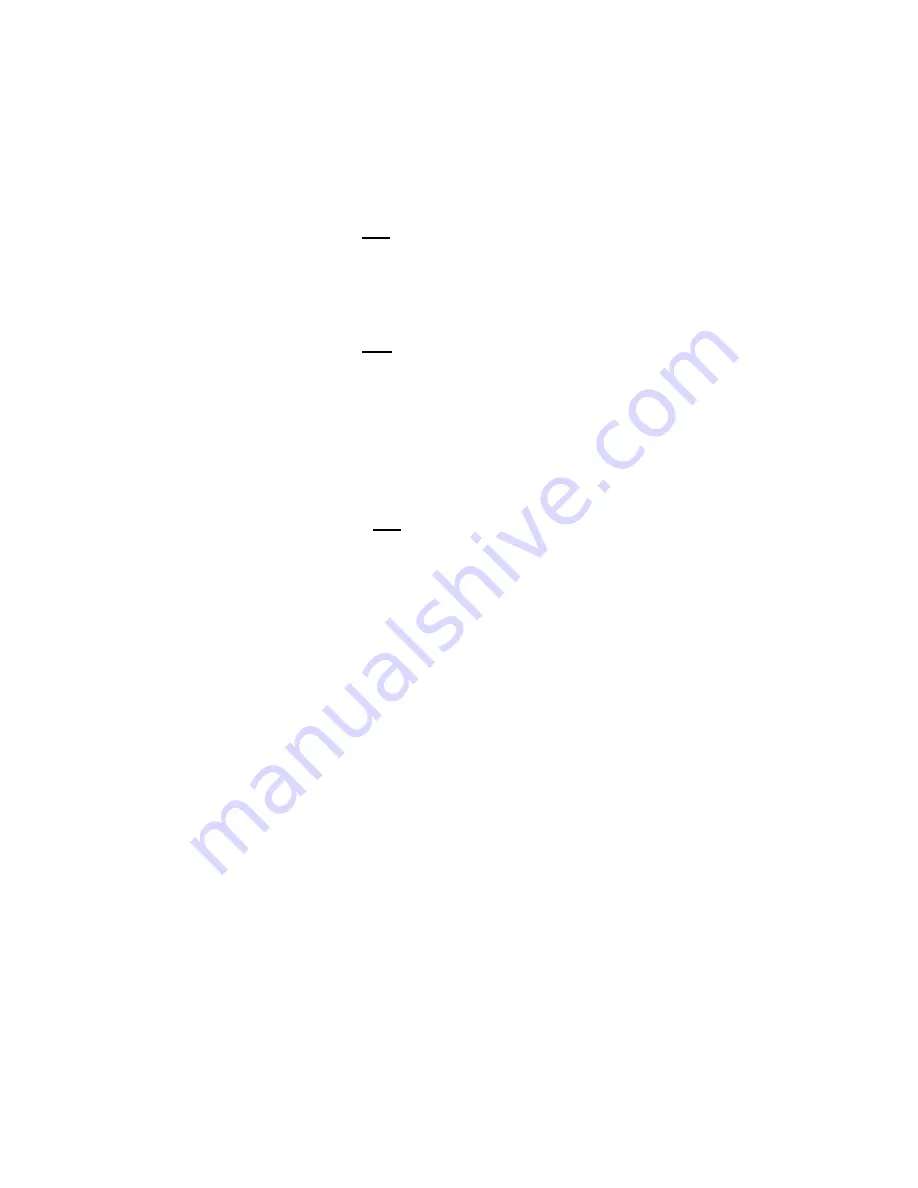
67
12.13 Anti Freeze Control
Anti freeze protection control menu can be set YES or NO by control panel.
In heatpump system, there are 3 types of anti freeze control:
1. Expansion tank anti-freeze control
Expansion tank anti freeze heater ON condition:
o
Outdoor ambient temp. < 3°C
Expansion tank anti freeze heater OFF condition:
o
Outdoor ambient temp. > 4°C
2. Water pump circulation anti freeze control
Water pump turns ON when
ALL
below conditions are fulfilled:
o
Heatpump OFF (stand by) OR error occurs.
o
Water flowing flag is ON.
o
Water flow switch is not abnormal.
o
Outdoor ambient temp. < 3°C OR outdoor ambient temp. sensor is abnormal.
o
Water inlet/outlet temp. < 6°C.
o
After 5 minutes from previous water pump OFF.
Water pump turn OFF when
ANY
of below conditions is fulfilled:
o
Outdoor ambient temperature
≥
4°C.
o
During -5°C < outdoor ambient temp. < 4°C
After water pump ON for 4 minutes, and water inlet temp.
≥
8°C.
Else, shift to back up heater anti freeze control.
o
During outdoor ambient temp. < -5°C
After water pump ON for 4 minutes, and water inlet/outlet
≥
20°C.
Else, shift to back up heater anti freeze control.
However, if flow switch is abnormal (H62), then water pump circulation anti freeze control will not activate.
3. Back up heater anti freeze control:
Back up heater turn ON when
ALL
below conditions is fulfilled:
o
Water inlet/outlet temp. < 6°C.
o
Water pump circulation anti freeze control activated and water pump ON for 4 minutes.
Back up heater turns OFF when ANY of below conditions is fulfilled:
o
Water inlet/outlet temp. > 28°C.
o
Water pump circulation anti freeze control deactivated/water pump OFF.
However, if back up heater is abnormal (H70) then back up heater anti freeze control will not activate.
Summary of Contents for WH-SHF09F3E5
Page 19: ...19 4 2 Outdoor Unit Air inlet rear Air outlet Air inlet side ...
Page 32: ...32 10 1 2 Solar Printed Circuit Board Optional ...
Page 48: ...48 67 C 67 C 60 C 65 C 63 C 67 C 67 C ...
Page 49: ...49 60 C 60 C 65 C 65 C 72 C ...
Page 55: ...55 67 C 67 C 67 C 67 C ...
Page 56: ...56 67 C 67 C 60 C 60 C 55 C 75 C ...