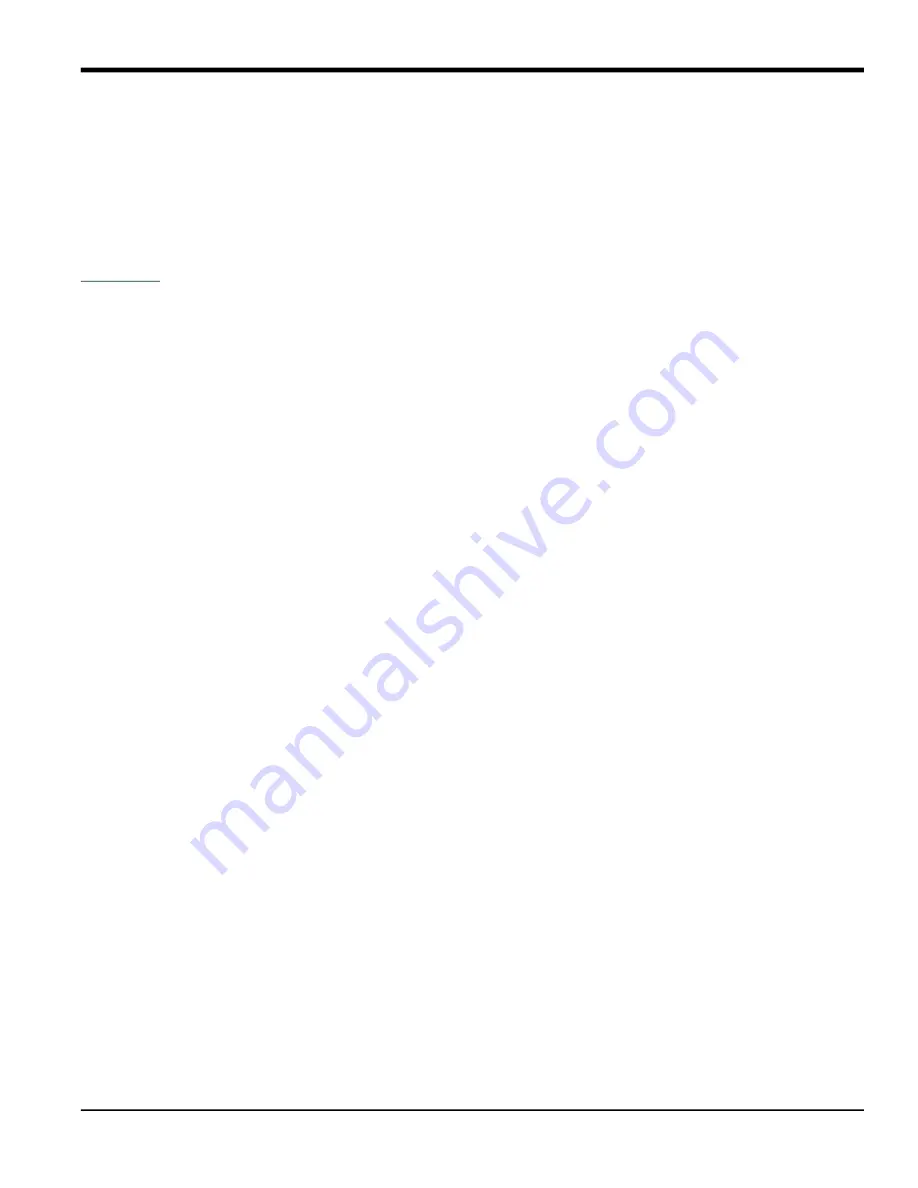
Model CTF878 Startup Guide
9
Chapter 2.
The CTF878 may be ordered for operation with power sources ranging from 85 to 264 VAC, at frequencies of 47 to
63Hz. The label on the shroud inside the electronics enclosure, just above the
TB1
line power terminal block, lists the
required line voltage and the fuse rating for the unit (the fuse rating is also listed in Chapter 4,
Specifications). Be sure
to connect the meter only to the specified line voltage.
Note:
For compliance with the European Union’s Low Voltage Directive (2006/95/EC), this unit requires an external
power disconnect device such as a switch or circuit breaker. The disconnect device must be marked as such,
clearly visible, directly accessible, and located within 1.8 m (6 ft) of the CTF878.
Refer to Figure 25 on page 40 to locate the power input terminal block and connect the line power as follows:
WARNING!
Improper connection of the line power leads, or connecting the meter to the incorrect line voltage,
may damage the unit. It may also result in hazardous voltages at the clamping fixture and
associated piping, and/or
within the electronics console.
1.
Prepare the line power leads by trimming the line and neutral AC power leads (or the positive and negative DC
power leads) to a length 0.5 in. (1 cm) shorter than the ground lead. This ensures that the ground lead is the last
to detach if the power cable is forcibly disconnected from the meter.
2.
Remove the plastic shroud that covers the terminal blocks.
3.
Strip 1/4 in. of insulation from the end of each of the three line power leads.
4.
Connect the line or positive
(
L
or
+
) and the neutral or negative
(
N
or
–
) power leads to the power input terminal block below the Main PC Board (see Figure 25 on page 40).
5.
Connect the ground lead to the ground connection on the inside wall of the enclosure (see Figure 25 on
page 40).
6.
Reinstall the shroud after all of the wiring has been completed.
Summary of Contents for CTF878
Page 1: ...panametrics com Flow 910 254U Rev A AUG 2021 Model CTF878 Clamp On Tag Flowmeter Startup Guide...
Page 2: ......
Page 4: ...ii no content intended for this page...
Page 6: ...Warranty iv Model CTF878 Startup Guide no content intended for this page...
Page 8: ...Contents vi Model CTF878 Startup Guide...
Page 76: ...Model CTF878 Startup Guide 68...
Page 96: ...Appendix A 88 Model CTF878 Startup Guide...
Page 99: ...Model CTF878 Startup Guide 91 Appendix B 9 21 10 22 11 23 12 24...
Page 100: ...Appendix B 92 Model CTF878 Startup Guide...
Page 104: ...Index 96 Doc Tittle Manual Type...
Page 106: ......
Page 107: ......