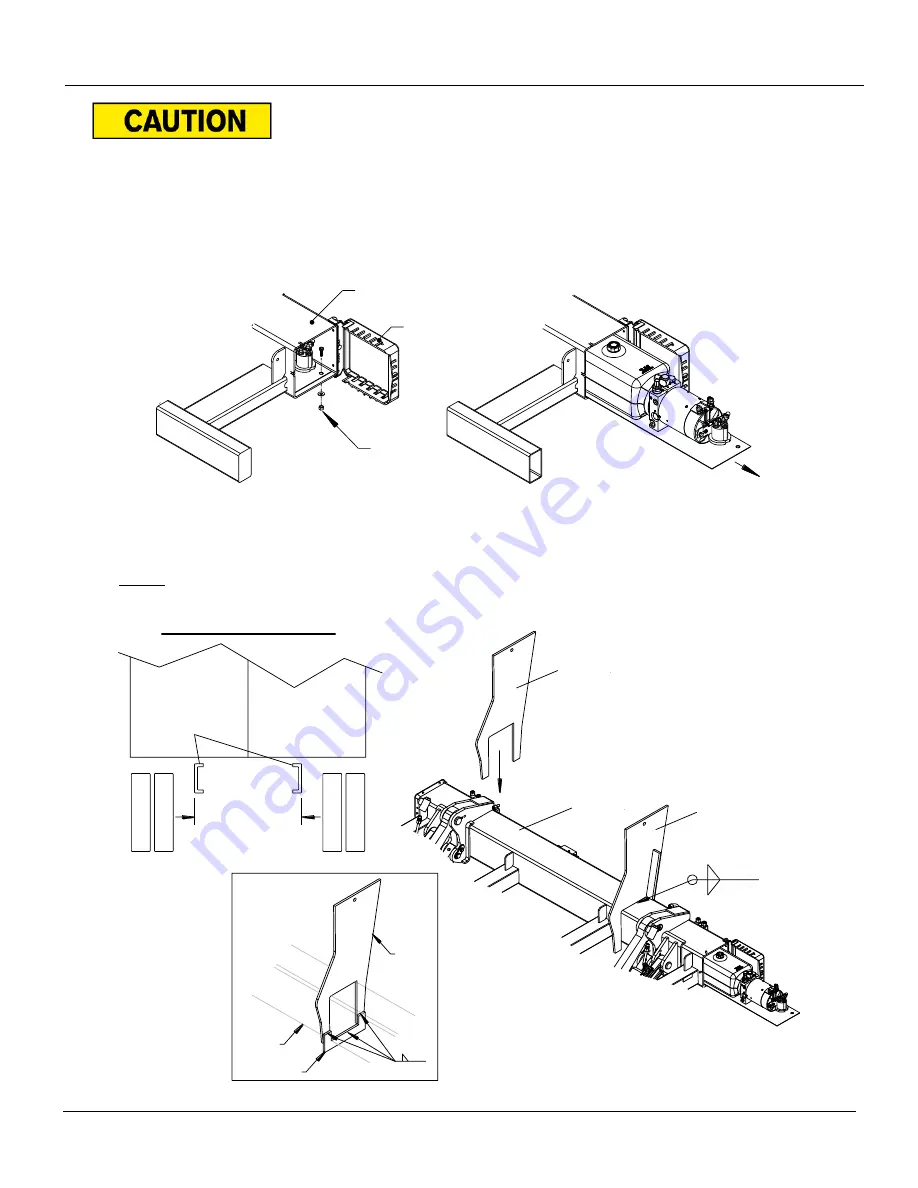
ILF 33/44/55 Installation Manual
Rev 1.1
26
Pull out power tray before welding. Power Tray is located inside the
mount tube and can be accessed through the curb side of the mount tube.
4.
Pull out the power pack tray approximately 20” out of the mount tube by removing the bolt on the
curbside and detach the ground strap and control power connector from the tray,
Fig. 14
.
Disconnect hoses, if necessary, to pull out tray far out. Verify hoses and cables are not in contact
with the inside walls of the tube prior to welding.
Cover
Mount
Tube
Hardware
Pull Out
5.
Weld the mount plates to the liftgates mount tube. Remember to keep the mount tube centered to
the truck. Determine the overall width of the frame and position the mount plates at the same
distance. Weld all around the mount plates and tube on both sides of the mount plates,
Fig. 15
.
NOTE
: ILF 55 will have an additional brace that’s required at the bottom of the plate,
Fig. 16
.
3/16"
Mount Tube
Mount Plate
Mount Plate
Dimension determines
the distance of the
mount plates.
Truck
Frame
3/16"
Rear View of Truck Frame
Mount Plate
Mount Tube
Gusset
3/16"
Fig. 15
Fig. 14
Fig. 16