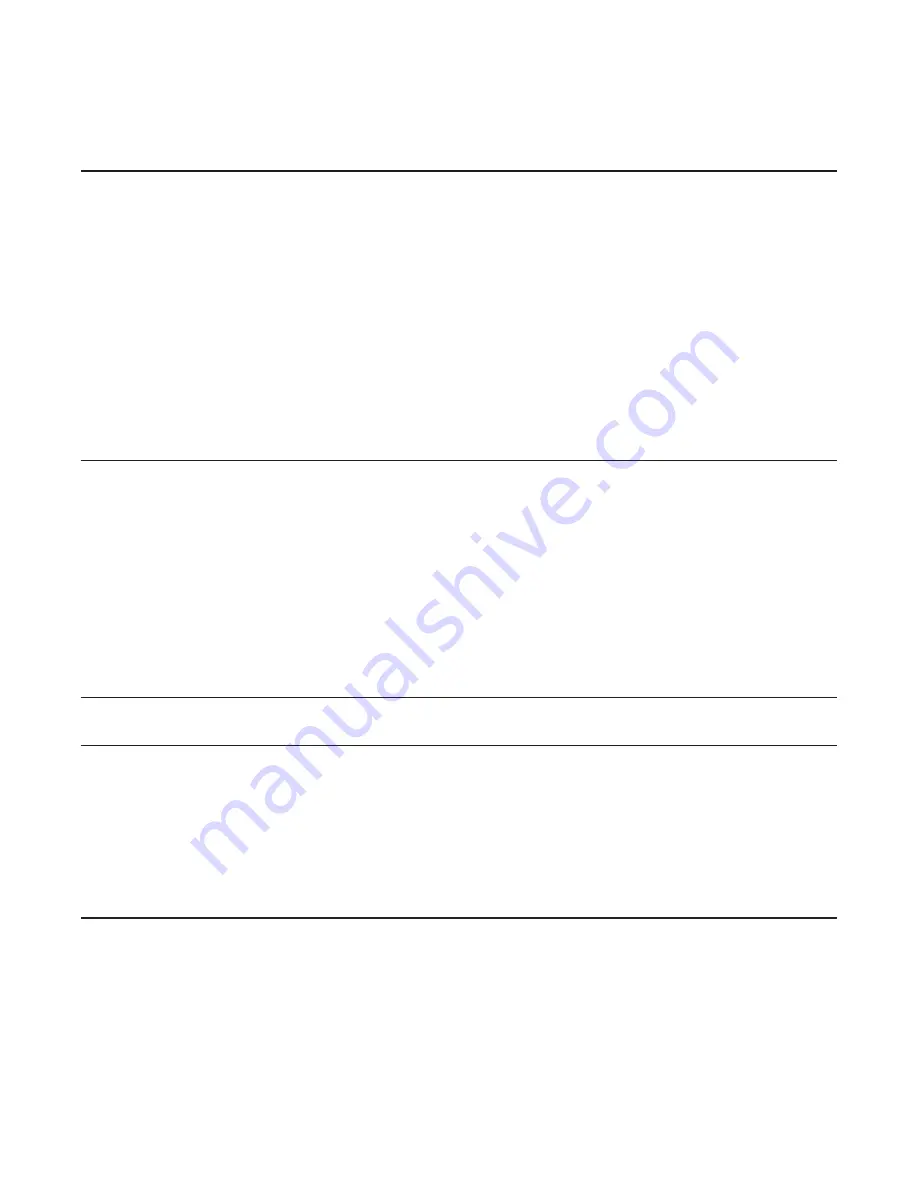
TROUBLESHOOTING
M-1659 10-26-07
PROBLEM
POSSIBLE
CAUSE
POSSIBLE
SOLUTION
Slow Speed
Low Flow
Check with flow meter. If low
investigate cause.
Line restrictions
Clear lines
Fittings or connections too small Replace with proper sizes.
Oil filter dirty
Replace
Hydraulic pump worn or
See Dealer for repair
damaged
Insufficient Digging
Worn teeth or point
Replace
Power
Low system Pressure (PSI)
Check with pressure gauge. If
low, investigate cause.
Relief Valve damaged or
Adjust or replace as required.
setting wrong
Excessive load
Reduce load to within machine
specifications.
Reverse Direction
Hoses reversed
Re-install hoses correctly.
Excessive Oil Heating
Line restrictions
Clear lines
Fluid dirty
Replace hydraulic fluid and filter.
Insufficient quantity of
Fill reservoir to proper level.
hydraulic fluid
increase reservoir storage
capacity.
Oil Leaks
Hoses loose or damaged
Tighten or replace
Fittings loose or damaged
Tighten or replace
Hydraulic motor seals worn
See Dealer for repair.
or damaged
75623
25