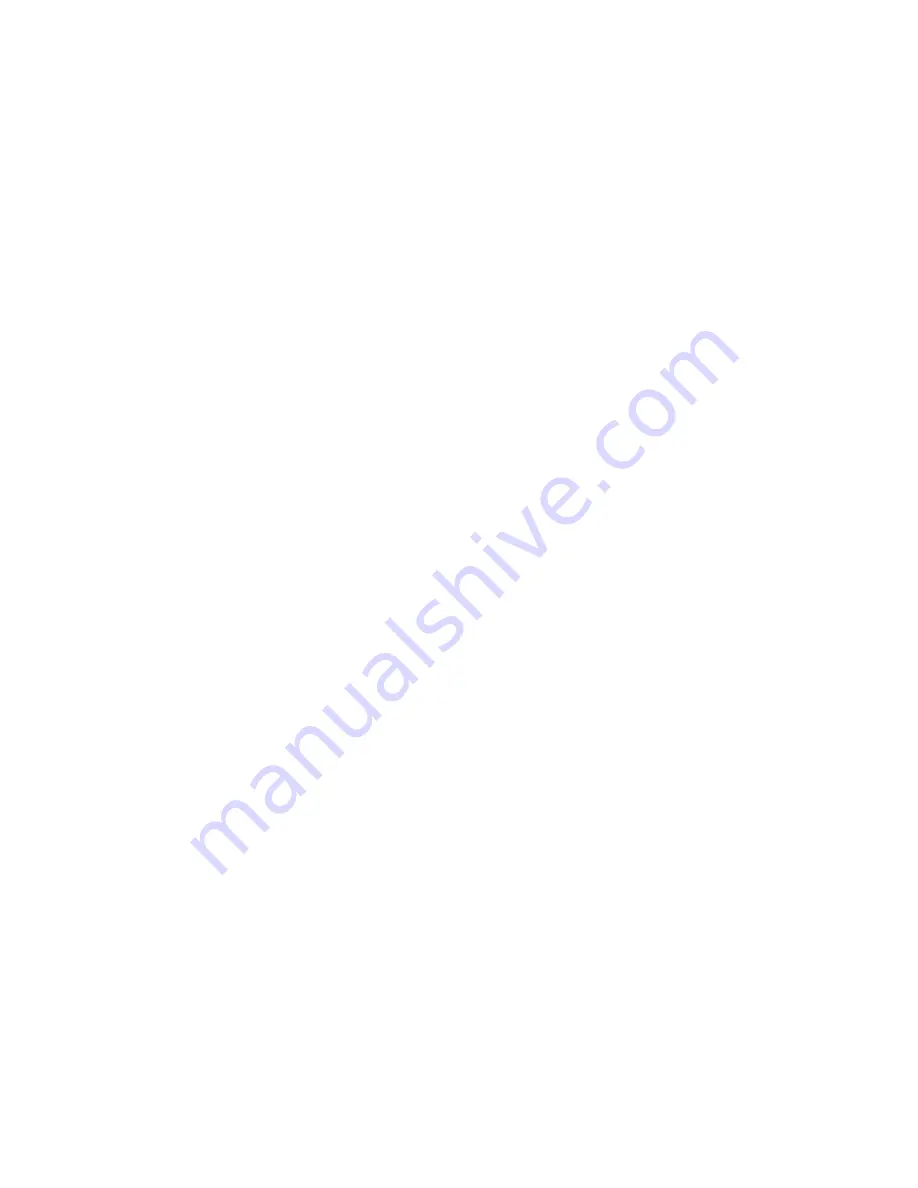
4
GENERAL SAFETY RECOMMENDATIONS
Safety for operators and ground personnel is of prime concern. Always take the necessary precautions to
ensure safety to others as well as yourself. To ensure safety, the prime mover and hoist must be operated with care
and concern for the equipment and a thorough knowledge of the machine’s performance capabilities. The following
recommendations are offered as a general safety guide. Local rules and regulations will also apply.
1.
Be certain equipment (boom, sheave blocks, etc.) is
either lowered to the ground or blocked securely be-
fore servicing, adjusting, or repairing hoist.
2.
Be sure personnel are clear of work area BEFORE
operating hoist.
3.
Read all warning and caution tags provided for safe
operation and service of the hoist and become fa-
miliar with the operation and function of all controls
before operating the hoist.
4.
Inspect rigging and hoist at the beginning of each
work shift. Defects should be corrected immediately.
Do not operate a hoist with defects.
5.
Keep equipment in good operating condition. Per-
form scheduled servicing and adjustments listed in
the “Preventive Maintenance” section of this manu-
al.
6.
An equipment warm-up procedure is recommended
for all start-ups and essential at ambient tempera-
tures below +40°F (+4°C).
7.
Do not exceed the maximum pressure (PSI, kPa)
or fl ow (GPM, lpm) stated in the hoist specifi cations
found in the specifi c sales brochure.
8.
Operate hoist line speeds to match job conditions.
9.
Protective gloves should be used when handling wire
rope.
10. Never attempt to handle wire rope when the hook
end is not free. Keep all parts of body and clothing
clear of cable rollers, cable entry area of fairleads,
sheaves and hoist drum.
11. When winding wire rope on the hoist drum, never at-
tempt to maintain tension by allowing wire rope to slip
through hands. Always use “Hand-Over-Hand” tech-
nique.
12. Never use wire rope with broken strands. Replace
wire rope that is damaged. Refer to wire rope sup-
plier manual.
13. Do not weld on any part of the hoist without approval
from PACCAR Winch Engineering.
14. Use recommended hydraulic oil and gear lubricant.
15. Keep hydraulic system clean and free from contami-
nation at all times.
16. Use correct anchor for wire rope and pocket in
drum.
17. Do not use knots to secure or attach wire rope.
18. The Gearmatic designed wire rope anchors are not
intended to support the rated load. ALWAYS main-
tain a minimum of fi ve (5) wraps of wire rope on the
drum. It is recommended that the last fi ve (5) wraps
of wire rope be painted bright red to serve as a visual
reminder.
19. Never attempt to clean, oil or perform any mainte-
nance on a machine with the engine running, unless
instructed to do so in this manual.
20. Never operate hoist controls unless you are properly
positioned at the operators station and you are sure
personnel are clear of the work area.
21. Assure that personnel who are responsible for hand
signals are clearly visible and that the signals to be
used are thoroughly understood by everyone.
22. Ground personnel should stay in view of the opera-
tor and clear of the hoist drum. Do not allow ground
personnel near wire rope under tension. A safe dis-
tance of 1½ times the working length of the wire rope
should be maintained.
23. Install guarding to prevent personnel from getting
any part of body or clothing caught at a point where
the cable is wrapped onto the drum or drawn through
guide rollers or potential “pinch points”.
24. Install switches or valves that will shut off power to
the hoist, in locations where they can be reached
by anyone entangled in the wire rope before being
drawn into the hoist or any “pinch point”.
25. “Deadman” controls, which automatically shut off
power to the hoist whenever the operator leaves his
station or releases the hoist control lever, should be
installed whenever practical.
26. Never allow anyone to position any part of body un-
der a suspended load.
27. Avoid sudden “shock” loads or attempting to “jerk” a
load free. This type of operation may cause heavy
loads, in excess of rated capacity, which may result
in failure of wire rope, hoist or boom structure.
28. Whenever possible, install the hoist in a location that
is not immediately adjacent to a “normal” operator’s
station.
29. All hoist controls shall be located within easy reach of
the operator. The controls shall be installed in such
a location that the operator is removed from the elec-
trical path to ground if the load, rigging, or wire rope
come in contact with or within proximity to an electri-
cally energized conductor.