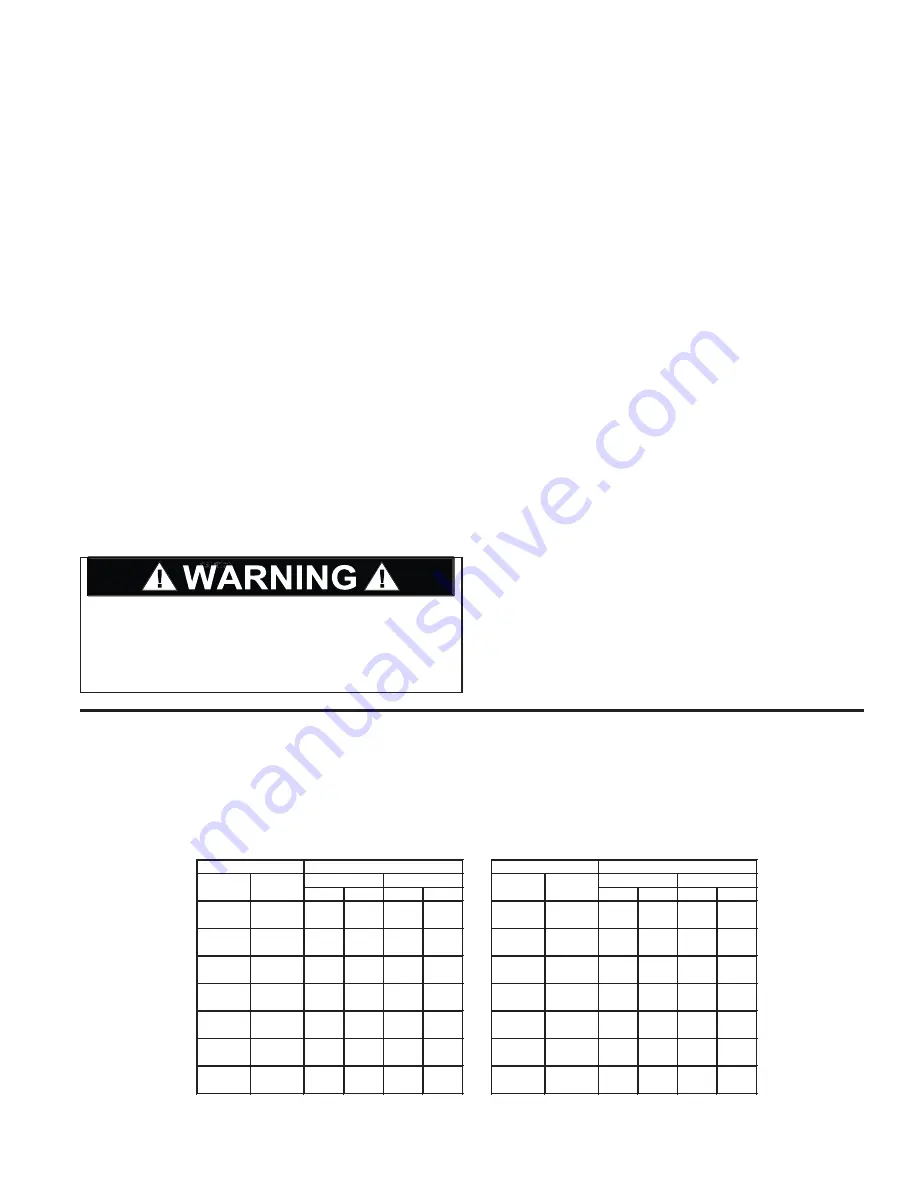
11
OIL SAMPLING AND ANALYSIS
Proper oil sampling and analysis of the sample, is a vital
part of a comprehensive preventive maintenance program.
Information obtained from the oil analysis is best utilized in
conjunction with a regular program of preventive mainte-
nance. The early warning of abnormal wear provided by
an analysis program allows the user to substitute preven-
tive maintenance for a far more costly and dangerous fail-
ure that may lead to loss of load control that could result in
property damage, personal injury or death. Early detection
of accelerated component wear allows the scheduling of
corrective maintenance and can reduce in-operation fail-
ures and costly down time.
Taking a Valid Oil Sample
Since the GH30B-FF hoist has an oil seal which separates
the free-fall end oil from the motor end oil, a sample from
each end must be analyzed at each maintenance interval.
Prepare the hoist by cleaning the drain area and drain ex-
tension tube in order to obtain an uncontaminated sample.
Operate the hoist in both directions for one to two minutes
and then take the oil sample from the drain port as soon as
possible. Do not take the sample from the fi rst oil out of the
drain port. Take a sample from the mid-stream fl ow of the
oil to obtain an accurate representation of the oil condition.
After taking an oil sample, refi ll hoist with recommended
lubricant.
Analysis
General Guide Lines
(After approximately 250 hours of operation)
Note:
The fi rst oil change usually contains more “wear
metals”. Following the initial break-in period, the wear
metal levels should stabilize at a lower number.
Iron Contaminates
100 to 400
ppm Normal
400 to 700
ppm Caution – Abnormal Sample (monitor
more frequently), tear-down inspection
may be required.
701 ppm & up
Unacceptable – Abnormal Sample (tear
down inspection required)
In all contaminate monitoring, equally important as the
level of contamination, is the change in the amount of con-
tamination compared to previous samples.
Moisture contamination will lead to the formation of acids
that damage all internal components. Silica found in the oil
typically indicates “dirt” and contaminated lubricant supply
or poor maintenance practices.
Hot oil may cause personal injury and/or burns to un-
protected skin. Make certain the oil has cooled to a safe
temperature (less than 110°F or 43°C) before taking an
oil sample, changing oil or servicing the hoist.
RECOMMENDED BOLT TORQUE
The general purpose torque shown in the chart applies to SAE Grade 5 & Grade 8 bolts, studs and standard steel full, thick and
high nuts.
Higher or lower torques for special applications will be specifi ed such as the use of spanner nuts, nuts on shaft ends, jam nuts and
where distortion of parts or gaskets is critical.
Lubricated torque values based on use of SAE 30 engine oil applied to threads and face of bolt or nut.
Dry
Lubed
Dry
Lubed
Dry
Lubed
Dry
Lubed
Torque (LB-FT)
Grade 5
Grade 8
1/4
20
28
5/16
3/8
18
24
16
24
7/16
1/2
9/16
5/8
8
6
12
9
17
13
24
18
45
35
70
50
23
31
50
35
80
110
80
150
110
110
55
75
150
115
210
160
14
20
13
20
12
18
11
18
265
200
Torque (LB-FT)
Grade 5
Grade 8
380
280
7/8
9
14
420
325
600
450
3/4
10
16
680
1 1/8
7
12
790
590
1290
970
1
8
14
640
7
12
1120
835
910
485
1460
1820
1360
1 3/8
6
12
1460
1095
2385
1790
1 1/4
3160
2370
RECOMMENDED FASTENER TORQUE
Bolt Dia.
Inches
Thds Per
Inch
Bolt Dia.
Inches
Thds Per
Inch
1 1/2
6
12
1940
LB-FT X 1.3558 = N-M X 0.7376 = LB-FT
LB-FT X 0.1383 = Kg-m X 7.233 = LB-FT