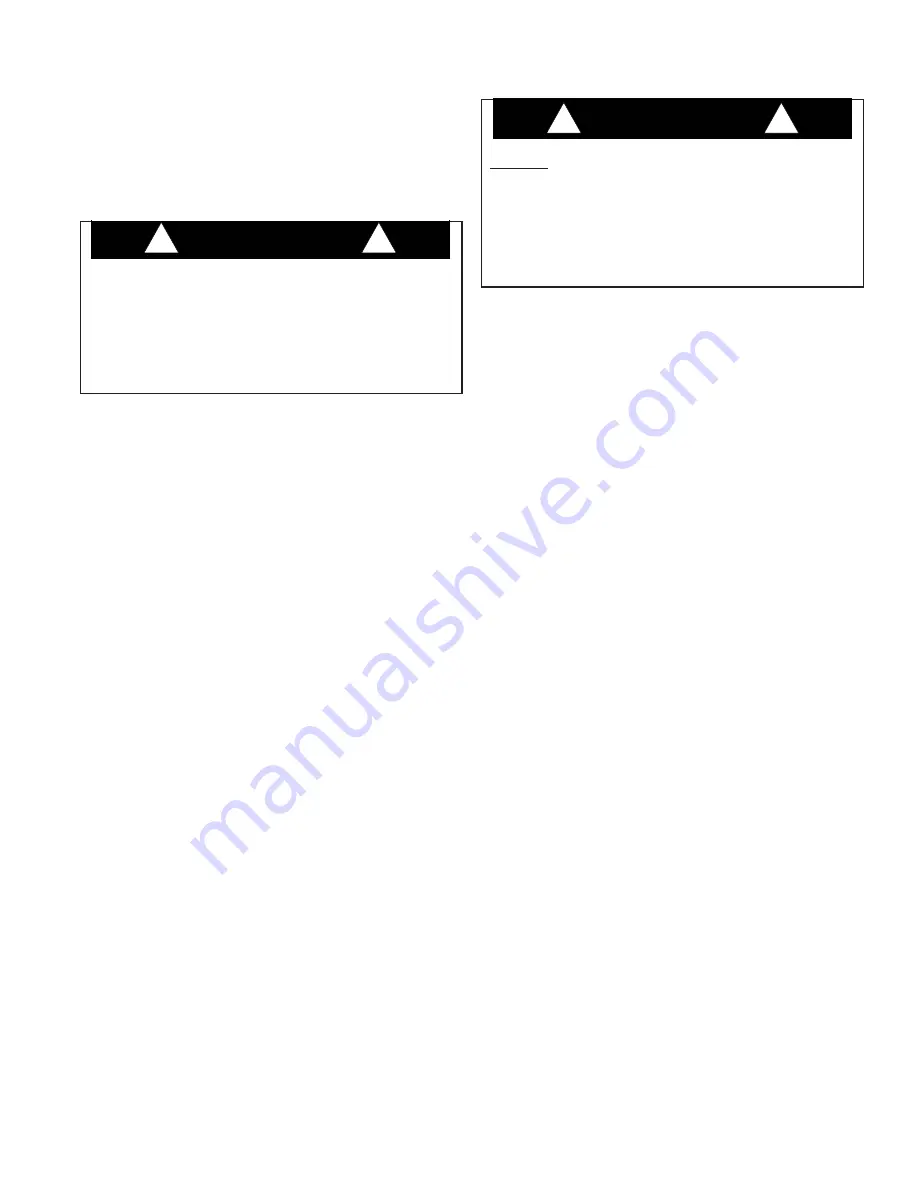
5
GENERAL INSTALLATION
1. The hoist must be mounted with the centerline of the
drum in a horizontal position.
2. When mounting the hoist, use SAE grade 8 (ISO class
10.9) capscrews or bolts and nuts using both mount-
ing holes in each end plate. Use narrow, hardened
washers under the bolt heads and nuts.
3. It is important that the hoist be mounted on a surface
that will not fl ex when the hoist is in use, since this
could bind the working parts of the hoist. Also, be sure
the hoist is mounted on a fl at surface. If necessary,
use shim stock to insure proper mounting. The mount-
ing surface must be fl at within 0.020 inches (.5 mm).
4. Hydraulic lines and components that operate the hoist
should be of suffi cient size to assure minimum back
pressure at the hoist motor ports. To insure adequate
static brake load holding ability, back pressure on the
hoist brake release port should not exceed 100 psi
(690 kPa).
5. Make certain that the hoist drum is centered behind
the fi rst sheave and the fl eet angle does not exceed
1½ degrees.
The hoist should also be mounted perpendicular to an
imaginary line from the center of the drum to the fi rst
sheave to ensure even spooling.
6. The hoist directional control valve must have a valve
without detents and with a spring centered spool such
that the valve returns to the centered position when-
ever the handle is released.
DO NOT
use a control valve with any detents or latch-
ing mechanism that would hold the control valve in an
actuated or running position when the operator releas-
es the control handle. Use of the wrong type of control
valve could lead to unintentional operation of the hoist,
which could result in property damage, personal injury
or death.
DO NOT
weld hoist to mounting surface. Welding may
not provide adequate structural support for winch loads.
This may cause loss of load control, which could result
in property damage, injury or death. Welding may also
damage bearings and seals, resulting in premature fail-
ure.
CAUTION
WARNING
!
!
CAUTION
WARNING
!
!