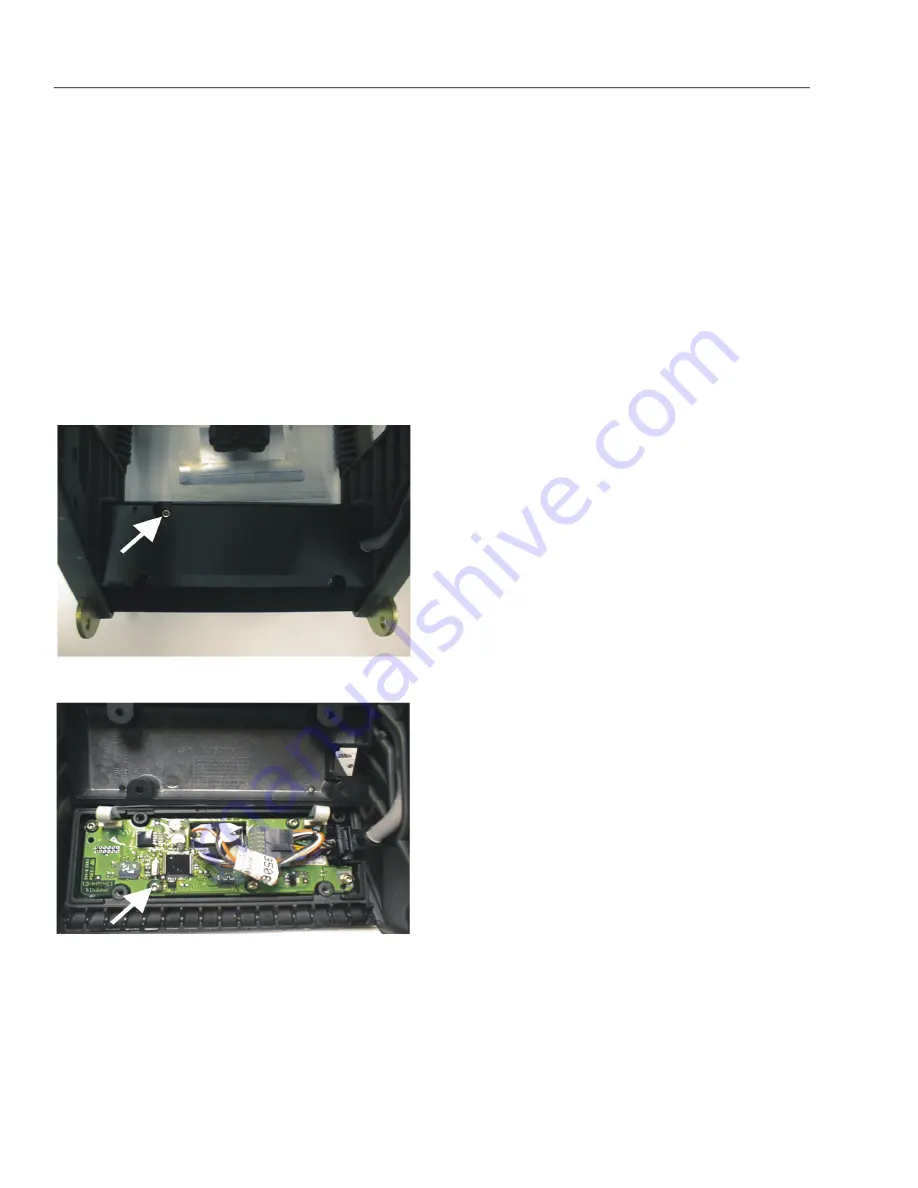
SECTION 3 - CHASSIS & SCISSOR ARMS
3-50
31215074
3.17 PLATFORM CONTROL STATION
Printed Circuit Board Replacement
1. Disconnect the platform control box and remove
from the machine.
2. Place the platform control box on a suitable work
bench.
3. Loosen and remove the long through bolts that
hold the two side control housings together.
NOTE:
You may have to only loosen the two power bolts
and remove the two closest the top in order to get to
the printed circuit board located in the top of the
control box where the drive/lift select switch is
located.
4. Loosen and remove the four bolts that hold the
bottom of the control box.
5. Disconnect the plug from the printed circuit
board.
6. Remove the bolts attaching the printed circuit
board to the control box.
7. Replace board and reassemble control box.
Go to
Discount-Equipment.com
to
order your
parts