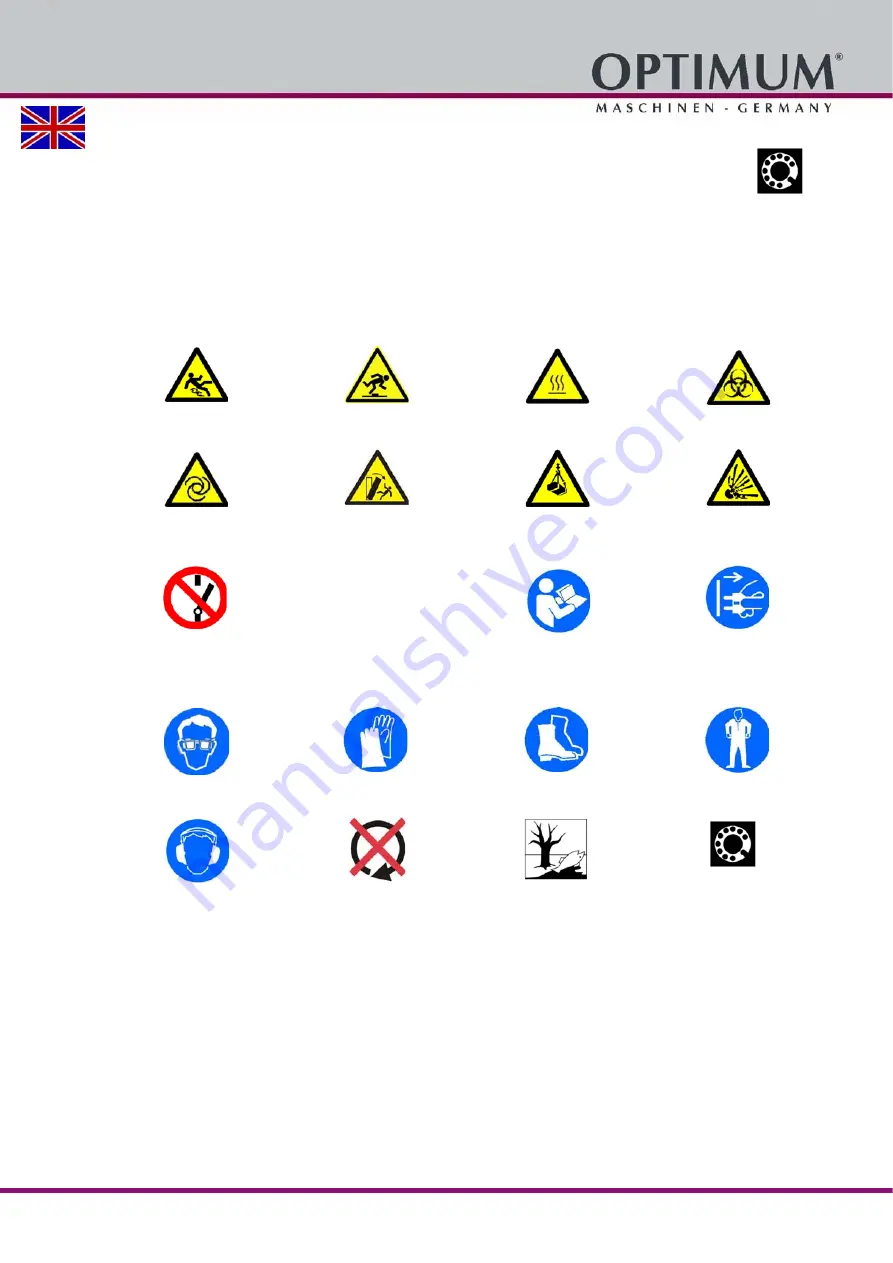
Version 1.2.8 - 2020-08-03
7
Translation of original operating manual
MT50
GB
MT
5
0_GB
_1.
fm
INFORMATION
If you are unable to solve a problem using these operating instructions, please contact us for
advice:
Optimum Maschinen Germany GmbH
Dr. Robert-Pfleger-Str. 26
D- 96103 Hallstadt
Email: [email protected]
1.2
Safety instructions (warning notes)
Warning danger of slipping!
Warning risk of stumbling!
Warning hot surface!
Warning biological hazard!
Warning of automatic start-
up!
Warning tilting danger!
Warning of suspended
loads!
Caution, danger of
explosive substances!
Activation forbidden!
Read the operating
instructions before
commissioning!
Disconnect the mains plug!
Use protective glasses!
Use protective gloves!
Use protective boots!
Use protective suit!
Use ear protection!
Only switch in standstill!
Protect the environment!
Contact address