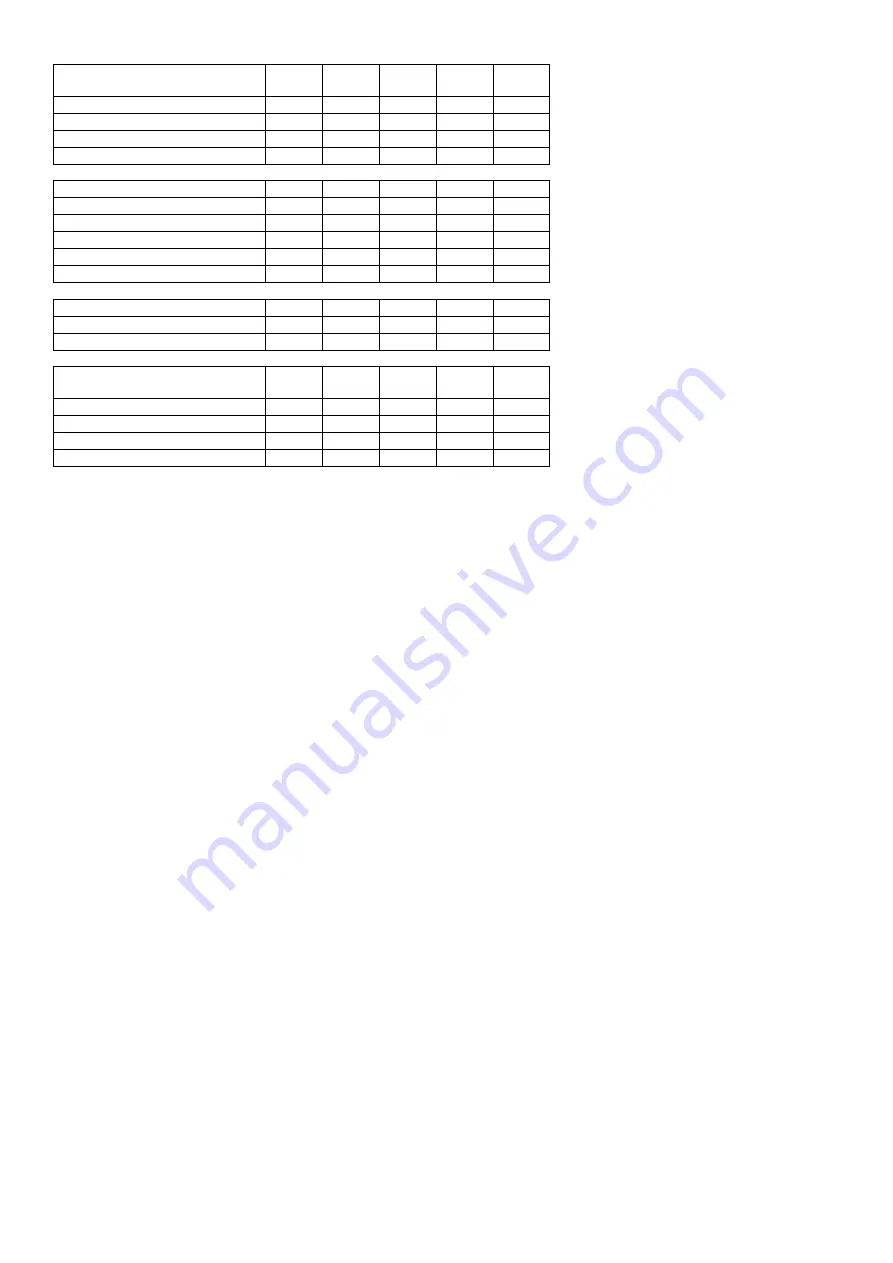
Biopel MINI - Installation and Operation Instructions
53
Installation menu, Compressor 1:
(Burner)
11kW
15kW
21kW
30kW
40kW
Cleaning period
1min
1min
1min
2min
2min
Opening time
2s
2s
2s
2s
2s
Cycle time
17s
17s
17s
25s
25s
Pause time
20h
20h
20h
20h
20h
Installation menu, Vacuum feeder:
11kW
15kW
21kW
30kW
40kW
Operating time
30min
30min
30min
30min
30min
Switch-on hour
9:00
9:00
9:00
9:00
9:00
Switch-on hour 2
15:00
15:00
15:00
15:00
15:00
Opening time
80s
80s
80s
80s
80s
Pause time
20s
20s
20s
20s
20s
Installation menu, Ash Remover:
11kW
15kW
21kW
30kW
40kW
Operating time
5min
5min
5min
10min
10min
Pause time
10h
10h
10h
10h
10h
Installation menu, Compressor 2 and 3:
(exchanger)
11kW
15kW
21kW
30kW
40kW
Cleaning period
1min
1min
1min
2min
2min
Opening time
3s
3s
3s
3s
3s
Cycle time
25s
25s
25s
25s
25s
Pause time
8h
8h
8h
6h
5h
These values can only be changed by a certified installer who is authorised to install and start up OPOP spol. s.r.o. boilers.
Information given in the tables serves for better orientation in the Service Menu items and simplifies the clarity of the set
values during the power selection in the First Boiler Start-up.
Changing these parameters has a significant effect on the boiler operation. If you need to reset the settings to the default
values (see table), you can perform the first boiler start-up again or use the Factory Settings function in the Main, Installation
and Service menus to reset to factory settings.