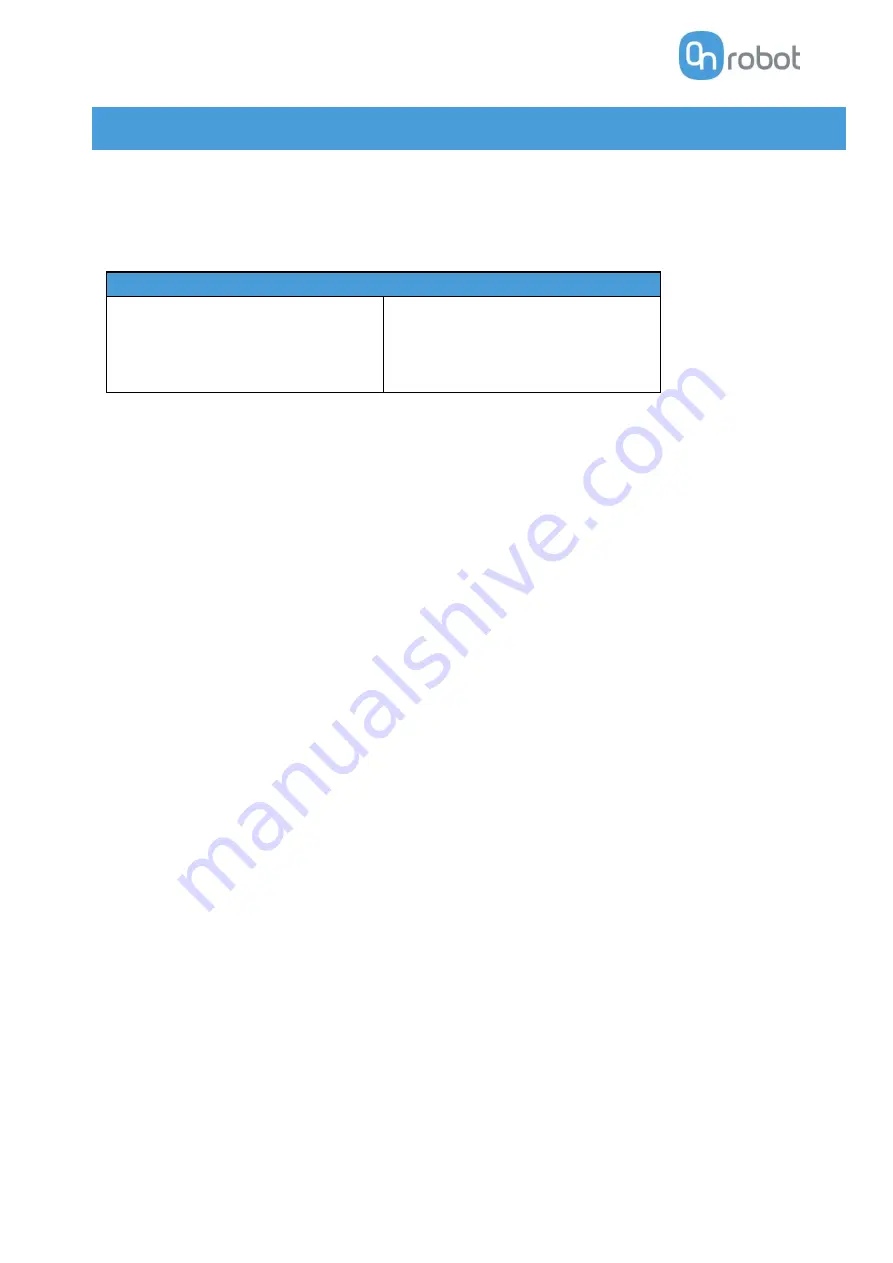
Operation mode(s)
10
3
Operation mode(s)
There are two alternative modes how the device(s) could be used:
Modes of Operation
OnRobot EtherNet/IP
required in the robot: EtherNet/IP
module
OnRobot WebLogic
required in the robot: digital I/O module
OnRobot EtherNet/IP
This mode uses the EtherNet/IP industrial network protocol to operate the grippers/sensor.
EtherNet/IP is a fieldbus that uses the standard Ethernet networking (simple UTP cable, standard network
switch can be used, etc.).
The Compute Box implements an EtherNet/IP Scanner (master device) and requires the robot controller
to implement an EtherNet/IP Adapter (slave device) to operate.
With configurable cycle time (e.g.: 8ms) the Computer Box can "read" and "write" to the robot so the
grippers/sensor can be controlled or monitored.
The communication is implemented via EtherNet/IP Assembly Instances that are created for each product
or product combination (e.g.: RG2+VG10). The instances are containing a set of words (16-bit data) that
can be used to control/monitor the grippers/sensor (e.g.: the 4th word of the Assembly Instance 104 is
the Actual Width for the RG2/6).
There are global functions provided (on the USB stick) to make it easy to access the product features.
OnRobot WebLogic
This mode allows simple Digital I/O communication to be used to operate the grippers/sensor.
For example the Compute Box could be easily programmed to:
•
when one of the robot digital outputs is set to HIGH, then the RG2 gripper opens to 77mm
•
or when the force values measured with the HEX-E QC reach 50N, the Compute Box sends a HIGH
digital output to the robot.
The Compute Box has 8 digital inputs and 8 digital outputs that can be freely configured for any "logic".
In this way the user can configure:
•
eight gripper/sensor controlling functionality (e.g.: set width to X, close, zero, set preload, etc.)
•
and eight gripper/sensor monitoring functionality (e.g.: is grip detected, is preload > 50N, etc.).
Furthermore, the "logic" can be complex, like:
•
is grip detected AND force >20 N
Summary of Contents for Gecko Gripper
Page 1: ...USER MANUAL FOR NACHI ROBOTS ORIGINAL INSTRUCTION EN v1 05...
Page 12: ...Operationmode s 12 Mode I OnRobot EtherNet IP...
Page 26: ...Installation 26...
Page 47: ...Operation 47...
Page 48: ...Operation 48 Mode II OnRobot WebLogic...
Page 64: ...Installation 64...
Page 115: ...Additional Software Options 115 O Tassemblyid 157 O Tdata size 64 bytes O Tparameters...
Page 123: ...Additional Software Options 123...
Page 139: ...Hardware Specification 139 RG2 GrippingSpeedGraph RG2 Work Range...
Page 142: ...Hardware Specification 142 RG6 GrippingSpeedGraph RG6 Work Range...
Page 162: ...Hardware Specification 162 9 2 Mechanical Drawings 9 2 1 Adapter plate s...
Page 163: ...Hardware Specification 163 Adapter I...
Page 164: ...Hardware Specification 164 Adapter J...
Page 170: ...Hardware Specification 170 Gecko All dimensionsare in mm and inches...
Page 171: ...Hardware Specification 171 RG2 FT All dimensionsare in mm and inches...
Page 172: ...Hardware Specification 172 RG2 All dimensionsare in mm and inches...
Page 173: ...Hardware Specification 173 RG6 All dimensionsare in mm and inches...
Page 174: ...Hardware Specification 174 VG10 All dimensionsare in mm and inches...
Page 175: ...Hardware Specification 175 All dimensionsare in mm and inches...
Page 176: ...Hardware Specification 176 VGC10 All dimensionsare in mm and inches...
Page 177: ...Hardware Specification 177 All dimensionsare in mm and inches...
Page 178: ...Hardware Specification 178 Quick Changer Tool side All dimensionsare in mm and inches...
Page 185: ...Certifications 185 12 Certifications...
Page 186: ...Certifications 186...
Page 187: ...Certifications 187...
Page 188: ...Certifications 188...
Page 189: ...Certifications 189...
Page 190: ...Certifications 190...