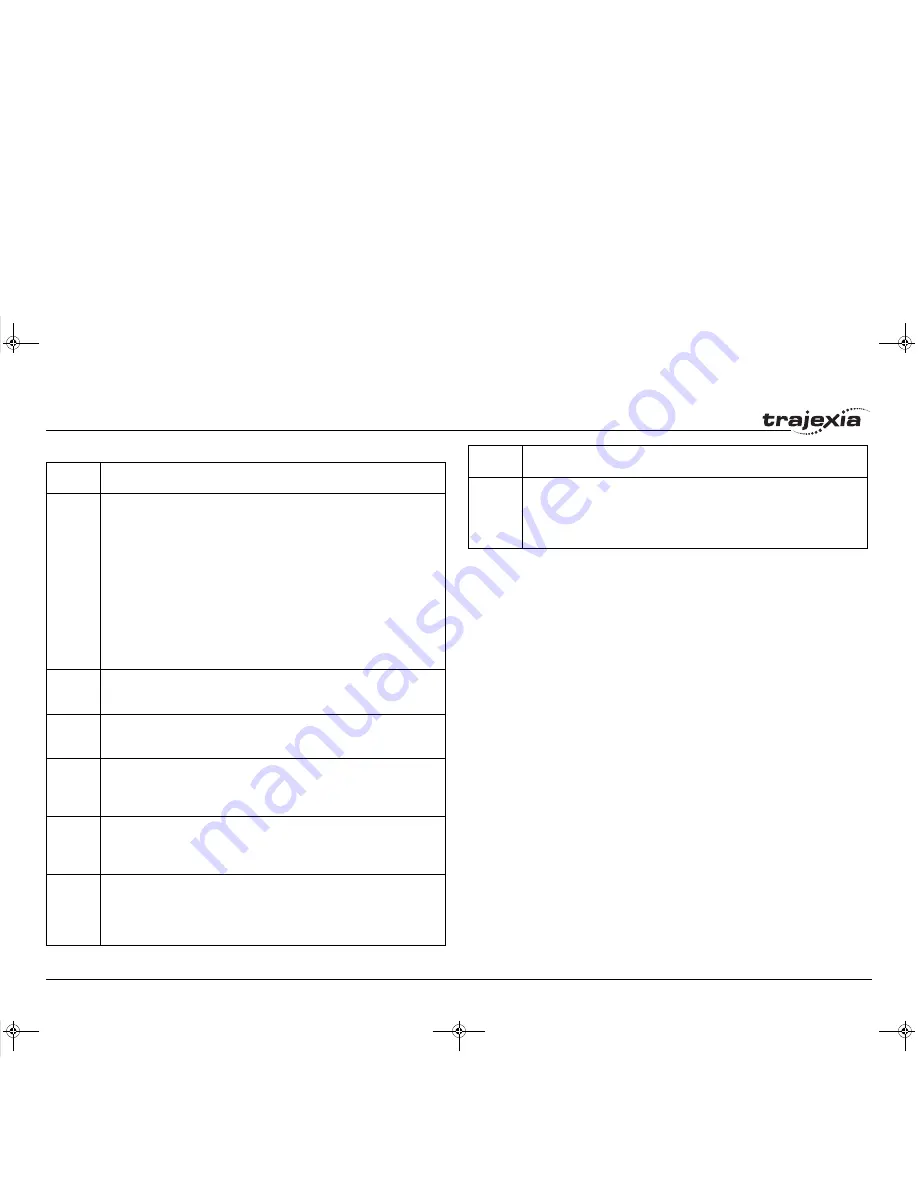
BASIC commands
PROGRAMMING MANUAL
63
Revi
si
on 3.0
/i
3.2.69 DATUM_IN
/i
sequence
value
Description
0
The
DATUM(0)
command will clear the motion error. The currently measured
position is set as the demand position (this is especially useful on stepper
axes with position verification). DATUM(0) also clears the Following Error that
exceeded the FE_LIMIT condition in the
AXISSTATUS
register for ALL axes.
It sets these bits in AXXISSTATUS to zero:
Bit 1 : Following Error Warning.
Bit 2 : Remote Driver Comms Error.
Bit 3 : Remote Driver Error.
Bit 8 : Following Error Limit Exceeded.
Bit 11 : Cancelling Move.
Note that the status can not be cleared if the cause of the problem is still
present.
1
The axis moves at creep speed forward until the Z marker is encountered.
The demand position is then reset to 0 and the measured position is corrected
to maintain the Following Error.
2
The axis moves at creep speed reverse until the Z marker is encountered.
The demand position is then reset to 0 and the measured position is corrected
to maintain the Following Error.
3
The axis moves at the demand speed forward until the datum switch is
reached. The axis then moves reverse at creep speed until the datum switch
is reset. The demand position is then reset to 0 and the measured position
corrected so as to maintain the Following Error.
4
The axis moves at the demand speed reverse until the datum switch is
reached. The axis then moves forward at creep speed until the datum switch
is reset. The demand position is then reset to 0 and the measured position
corrected so as to maintain the Following Error.
5
The axis moves at demand speed forward until the datum switch is reached.
The axis then reverses at creep speed until the datum switch is reset. The
axis continues at creep speed until the Z marker of the encoder is encoun-
tered. The demand position is then reset to 0 and the measured position cor-
rected so as to maintain the Following Error.
6
The axis moves at demand speed reverse until the datum switch is reached.
The axis then moves forward at creep speed until the datum switch is reset.
The axis continues at creep speed until the Z marker of the encoder is
encountered. The demand position is then reset to 0 and the measured posi-
tion corrected so as to maintain the Following Error.
Type
Axis parameter
Syntax
DATUM_IN
DAT_IN
Description
The
DATUM_IN
axis parameter contains the input number to be used as the
datum switch input for the
DATUM
command. The valid input range is given
by 0 to 31. Values 0 to 15 represent physically present inputs of TJ1-MC__ I/
O connector and are common for all axes. Values 16 to 27 represent software
inputs which can be freely used in programs and commands such as IN and
OP. These are also common for all axes. Values 28 to 31 are directly mapped
to driver inputs present on CN1 connector, and they are unique for each axis.
Which driver inputs are mapped to inputs 28 to 31 depends on Servo Driver
parameter Pn81E setting. Recommended setting is Pn81E = 0x4321, with the
following mapping:
Note: The origin input is active low, i.e., the origin switch is set when the input
is off. The feedhold, reverse jog, forward jog, forward and reverse limit inputs
are also active low. Active low inputs are used to enable fail-safe wiring.
Sigma II
•
input 28: CN1-40
•
input 29: CN1-41
•
input 30: CN1-42
•
input 31: CN1-43
Sigma III
•
input 28: CN1-13
•
input 29: CN1-7
•
input 30: CN1-8
•
input 31: CN1-9
sequence
value
Description
I52E-EN-03.book Seite 63 Freitag, 29. Juni 2007 11:55 11