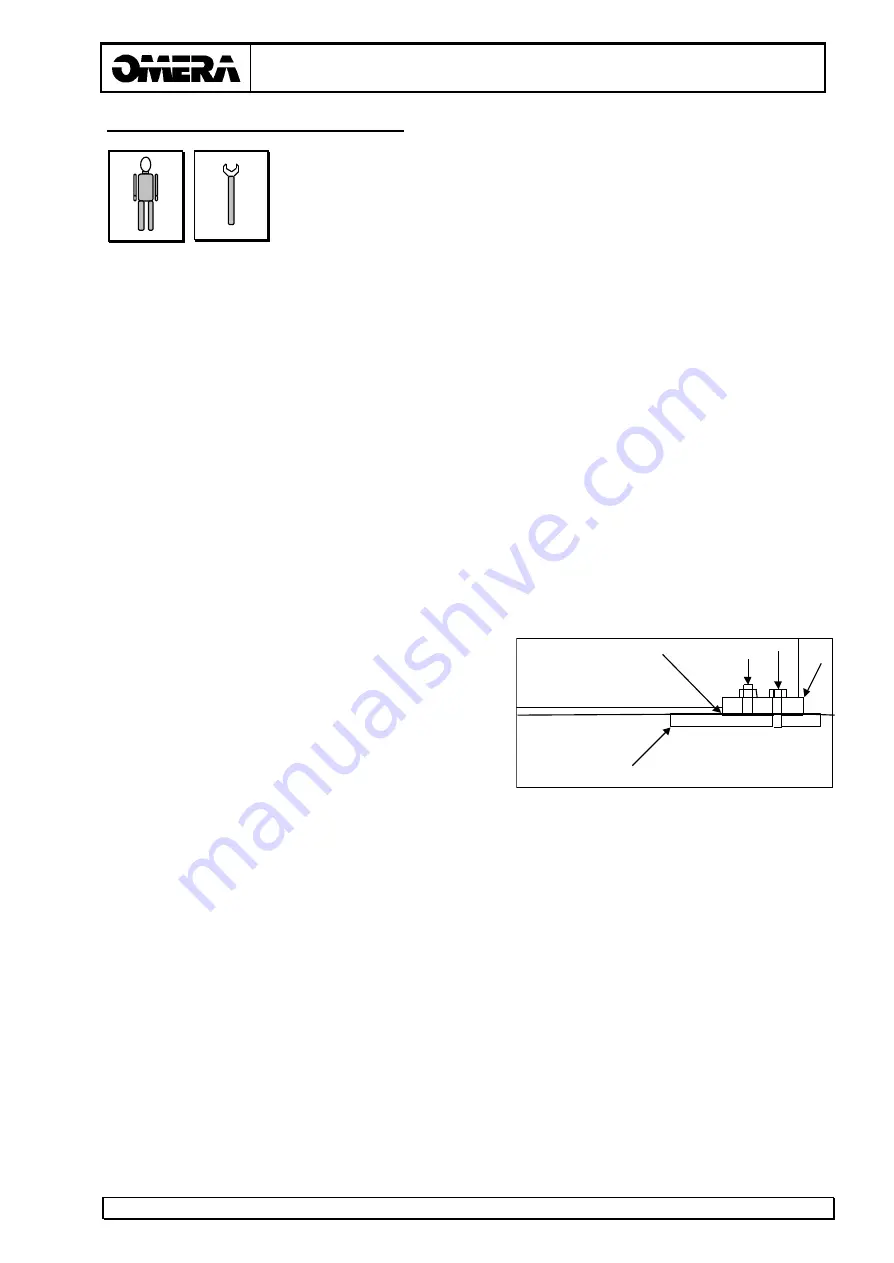
OIL-HYDRAULIC PRESSES WITH TWO UPRIGHTS
OPERATION AND MAINTENANCE MANUAL
14
5.
INSTALLATION CONDITIONS
For correct positioning of the machine, the instructions contained in the overall dimensions and foundation
drawing should have been followed. This drawing should have already been supplied to the customer but is also
included at the beginning of this manual.
Installation and commissioning are usually carried out by Omera technicians.
As far as possible, the machine should be installed away from possible sources of electromagnetic interference
(such as welding equipment) and a sufficient amount of space should be left around the machine for routine and
extraordinary maintenance.
The line which supplies electric power to the machine should not undergo variations in voltage which are outside
the range allowed by current regulations.
The area used for manual loading and unloading of the pieces is at the front, so sufficient space should be
allowed for machine use in accordance with safety regulations.
5.1
INSTALLATION OF PRESSES WITH MONOLITHIC STRUCTURE
To install the machine, proceed as follows:
?
Position the base (C) on the supporting plates (1) of the
foundations (P) making sure that the holes match the
anchoring bolts which are sunk into the foundation.
?
Use the appropriate grub screws (3) to level the base.
?
Fill any gaps remaining between the base feet (5) and the
anchor plates (1) with sheet metal shims (2).
?
Tighten the log bolt nuts (4) and make sure that the machine is level.
?
Attach the removable casings of the electrical connectors to the respective fixed casings; this operation is
aided by the presence of reference marks.
NOTE:
After the first 6 months of operation check that the machine is level.
1
2
3
4
C
P
5