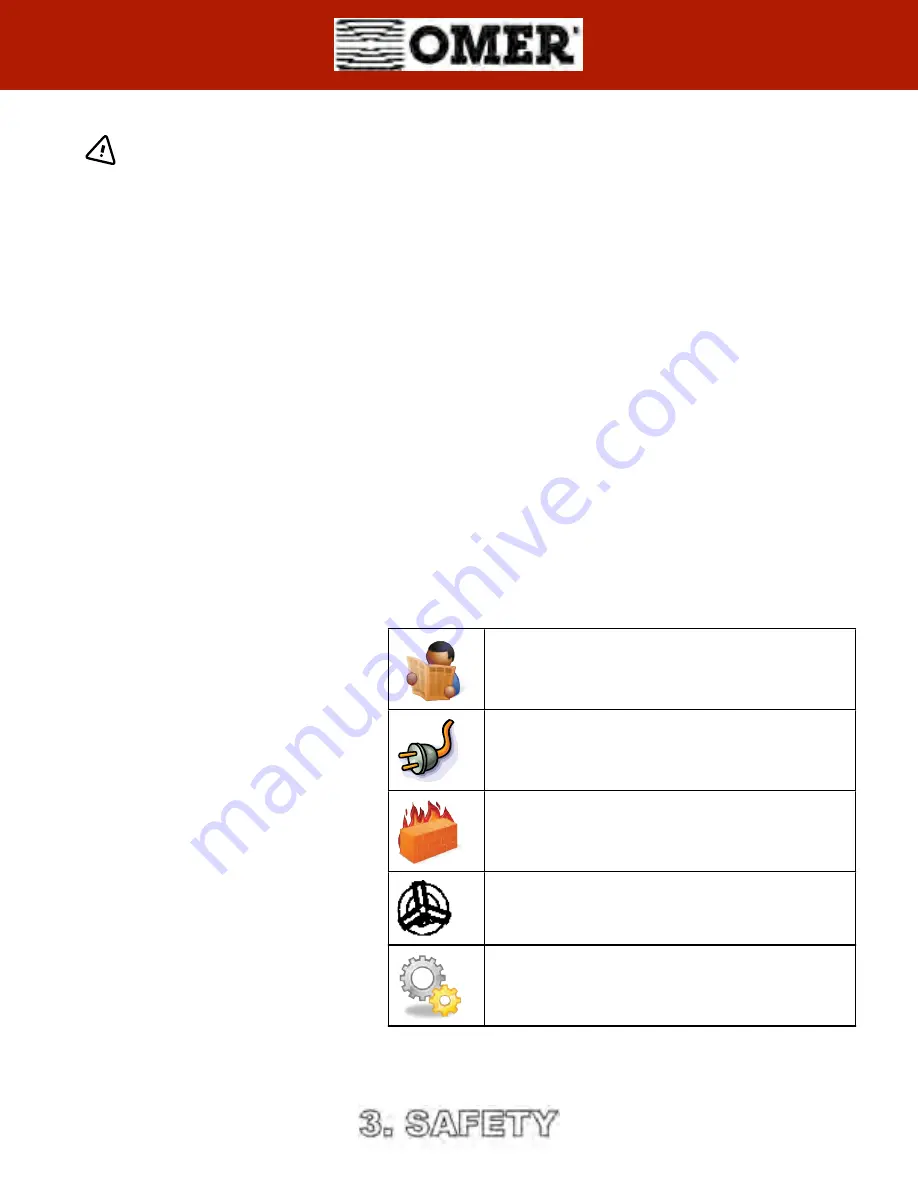
3.
SAFETY
Attention to:
- USER
- OPERATOR / SPECIALIZED TECHNICIAN
3.1.
Expected use
The function of the vehicle lift is to lift motorized vehicles, which have the distribution of the loading
according norms in force.
Only move the vehicle on the lift in the fully down position.
The accessories indicated in the relating chapter can be used.
3.2.
General safety regulations
For quick reference by operator, this manual must:
• be kept in a well known, easily accessible place
• be kept in good condition
Before proceeding with installation and use of the machine, the user must read
the manual carefully, especially the safety rules.
The machine should be used by authorized, trained personnel only.
The user (owner and / or employee) must make sure that the installer has provided:
• all accessories
• the spares provided with the lift
• this use and maintenance manual
Use as described in this manual only.
Always use the accessories
recommended by the manufacturer .
O.M.E.R. N.A. declines all responsibility
for non-compliance with the directions
given in this manual
The main safety rules are shown to the
right.
Read all instructions carefully
Put the main switch to the zero position when the
machines is not in use. Never pull the electric cable
to remove the plug from the socket
To reduce the risk of fires, avoid using the lift close to
open drums of inflammable liquid (such as gas /oil)
and/or in explosive environments.
Makes sure the work area is adequately ventilated
when using internal combustion engines
Avoid contact between parts of the body and/or
clothing and moving parts.
Summary of Contents for Kar 350
Page 7: ......
Page 8: ...2 4 Loading Conditions...
Page 16: ...LIFT...
Page 17: ...19...
Page 19: ...LABEL 6 LABEL 7 LABEL 8 LABEL 9 LABEL 10...
Page 20: ...LABEL 11 LABEL 12 LABEL 13...
Page 26: ...JOIN THE HOSES RESPECTING THE NUMBERING HOLE FOR THE HOSE...