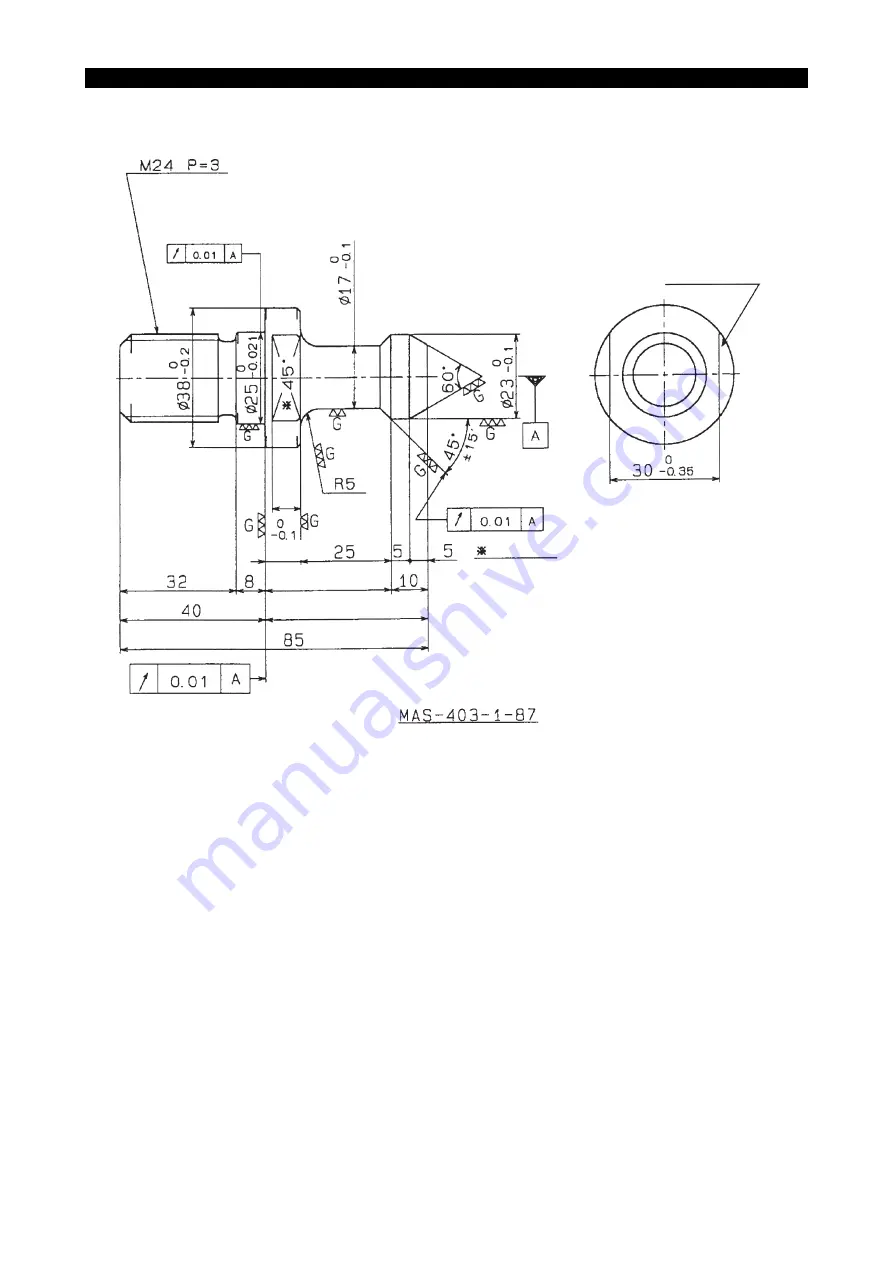
5699-E P-35
SECTION 3 OPERATION (OF CNC LATHE)
MAS1
LE11214R0100500190002
(
φ
1.50 )
0
0.008
(
φ
0.98 )
0
-0.008
(
φ
0.67 )
0
-0.004
(
φ
0.91 )
0
-0.004
(1.18 )
0
-0.004
Stamp "45
°
"
(1.26)
(1.57)
(0.31)
35 (1.38 )
8
(0.31)
0
-0.1
0
-0.004
10 (0.39 )
0
-0.004
45 (1.77 )
0
-0.1
0
-0.004
(0.39)
(0.20)
(0.20)
(0.98)
(3.35)
Stamp "5"
Material :
Heat treatment:
SNCM420
Carburizing (HRC 60 or harder)
(0.20)