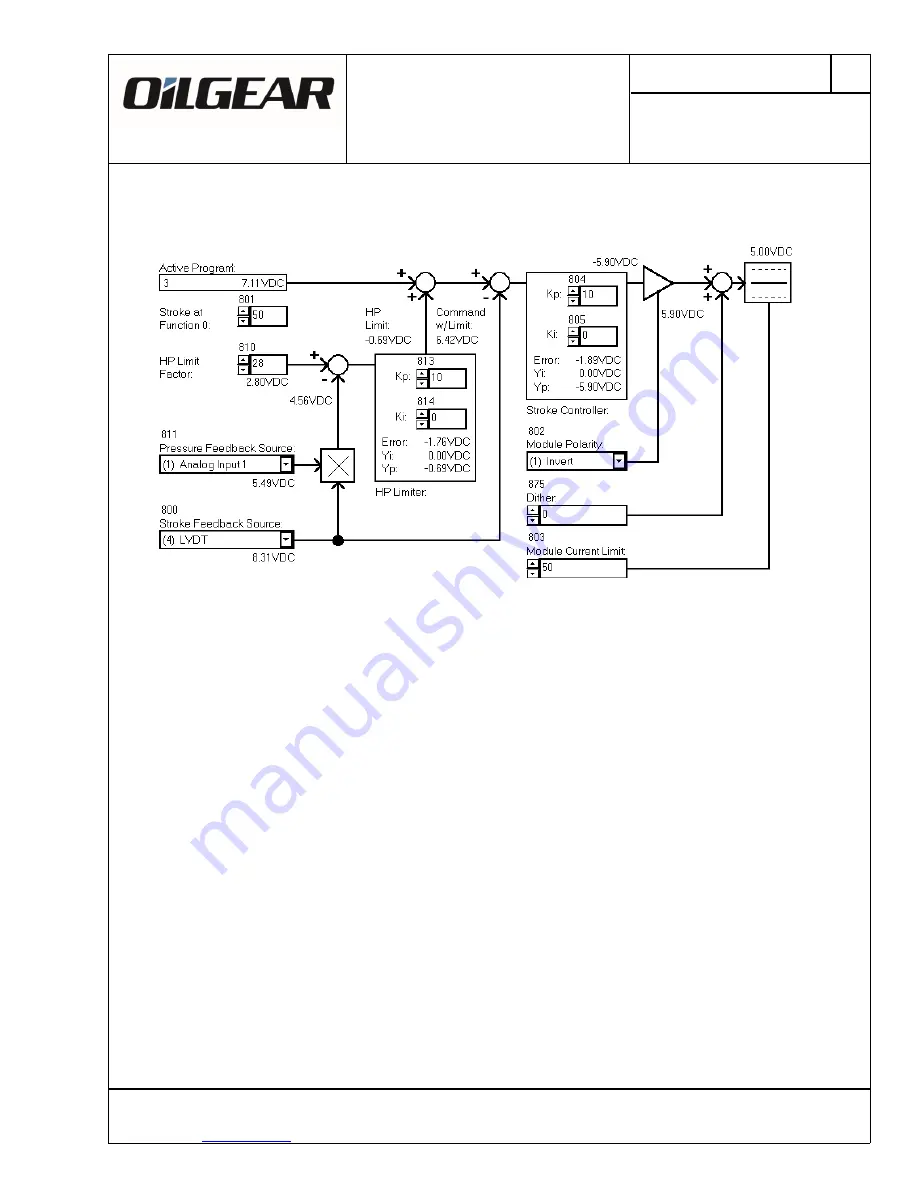
EPC
SERVO AMPLIFIER MODULE
Part Number L723888-3xx
ELECTRONIC
Telephone: (231) 929-1660
Oilgear
Fax:
(231) 929-7879
1424 International Dr
Issued May 31, 2018
Web Site:
www.oilgear.com
Traverse City, MI USA 4 9 6 8 6
Bulletin 836260F
34
4.3.3 Configuration Example
Figure 13: Pump Controller Configuration
Figure 13 shows the Pump Controller Module Form. The Diagnostic screen shows that Program
3 is active and passes the command of 7.11V to the Pump Controller. The Function Zero Stroke is
set to 50% (program item 801=50), so if no program was active a neutral stroke would be the
Pump Controller command signal.
The Pressure Feedback Source is Analog Input 1 (program item 811=1) and the Stroke Feedback
Source is LVDT (program item 800=4). The internal HP calculation based on these pressure and
stroke signals results in a value of 4.56V. The HP Limit Factor of 28% results in a value of 2.80V, so
the actual HP is greater than the allowed HP. The error signal is the difference of these calculated
numbers is 2.80V - 4.56V = -1.76V. The HP Limit is made up of the Yi and Yp contributions
computed from the HP Limiter PI controller.
The resulting Command with HP Limit is 7.11V - 0.69V = 6.42V. This command, along with the
Stroke Feedback signal is passed to the Stroke Controller, where the error signal is 6.42V - 8.31V =
- 1.89V . This error signal is used for the Stroke Controller PI calculations, and the output is equal to
the Yi and Yp contributions is 0.00V - 5.90V = -5.90V.
Module Polarity is set to Invert the module output (program item 802=1) so the -5.90V signal
becomes 5.90V. Finally, the current is limited to 50% of maximum, so the 5.90V signal decreases to
5.00V.