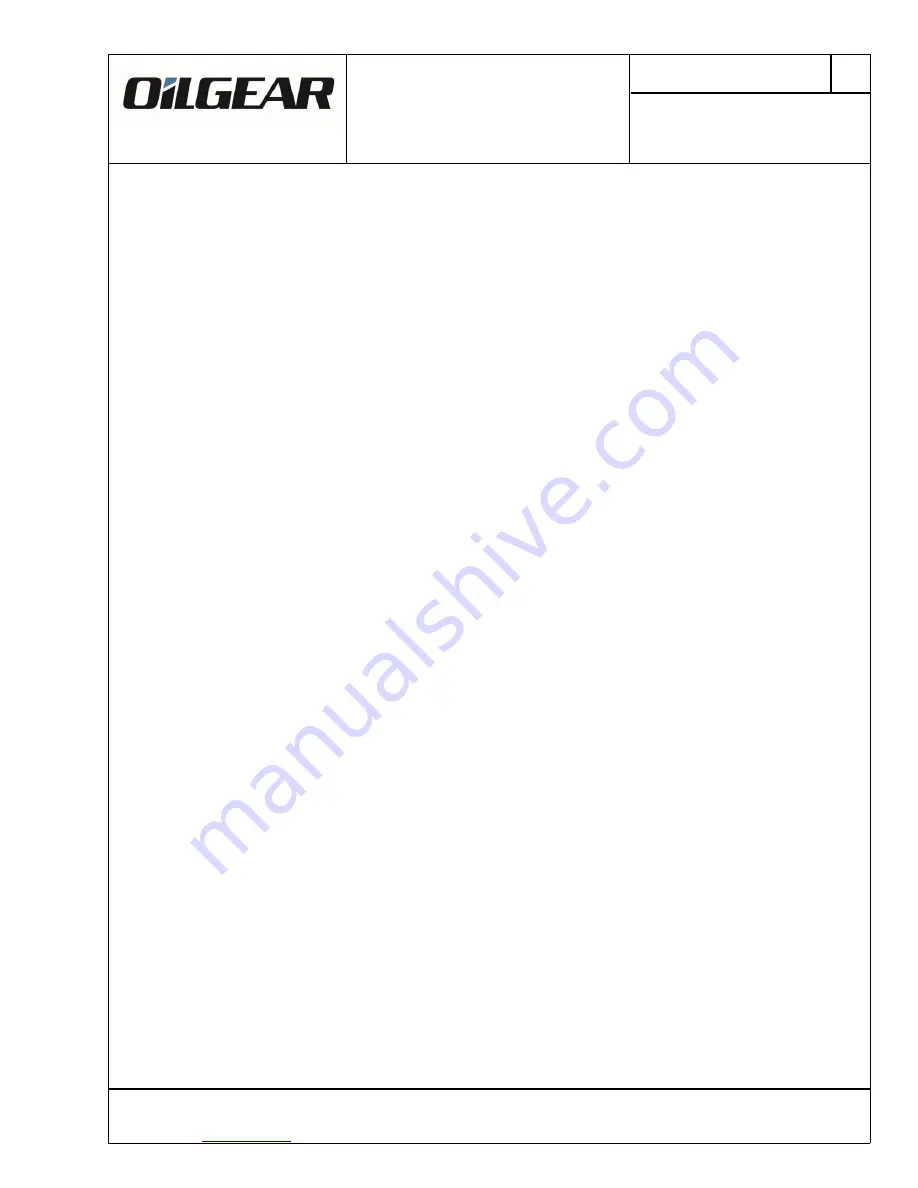
EPC
SERVO AMPLIFIER MODULE
Part Number L723888-3xx
ELECTRONIC
Telephone: (231) 929-1660
Oilgear
Fax:
(231) 929-7879
1424 International Dr
Issued May 31, 2018
Web Site:
www.oilgear.com
Traverse City, MI USA 4 9 6 8 6
Bulletin 836260F
31
4.3.2.1 Function Zero Stroke Command
Normally, the Active Program Block provides the command to the Pump Controller. For certain
applications, it might be desirable to have the ability to switch between two function programs,
and the EPC provides that feature by allowing two program blocks selectable by the digital input.
In some circumstances, a second program is not needed but some type of state is desired. A
prime example would be a stand-by mode in which a fixed stroke would be commanded. In this
circumstance, the user could place a pre-defined program in block 1 and select program 0 for
block 2 (please refer to Section 4.1.3 regarding Program Block Configuration (21x).
The Function Zero Stroke Command is configured by program item 801 or from the Pump
Controller Form. It is expressed as a value from 0 to 100%, where 0 equals full negative current,
100 equals full positive current, and 50 represents neutral or no current. A Function Zero Stroke
Command of 75, for instance, would provide a 50% stroke command to the valve.
4.3.2.2 Stroke Controller
The Stroke Controller portion of the Pump Controller is configured by selecting a Stroke
Feedback Source (program item 800) and setting values for KP (program item 804) and KI
(program item 805) for the Stroke PI Controller. These values can be optimal adjusted from
the Pump Controller Form.
Stroke Feedback Device
: The Stroke Feedback Device determines which signal the command to
the Stroke Controller is compared to. Valid entries are (0) Open Loop, (1) Analog Input 1, (2)
Analog Input 2, (3) Analog Input 3, (4) LVDT 1 (Analog Input 4), or (5) Ramp 1. If Open Loop
is chosen, the stroke controller is disabled and the command is passed directly through to the
output.
KP
and
KI
: KP and KI provide the proportional and integral constants, respectively, for the PI
control algorithm. Both terms are expressed as 0 to 100% of a maximum value. The PI control
loop can be made a P-only control loop by setting the KI term to 0. Likewise, the PI control loop
can be made an I-only control loop by setting the KP term to 0.
The command to the stroke controller is from either the Active Program or the Function Zero
Stroke Command (or by the HP-limited adjustment of this command, please refer to Section
4.3.2.3). An error signal is produced by comparison of this command to the stroke feedback
signal. The PI loop produces Yp and Yi, determined by the error signal and the KP and KI
constants, respectively. The stroke controller output is made by the summation of Yp and Yi.
The Stroke Controller is disabled if the Stroke Feedback Source (program item 800) is selected as
Open Loop.
The Pump controller relies on the stroke feedback device being configured correctly. Please
refer to Section 4.4.5 regarding the LVDT Adjustment Algorithm.