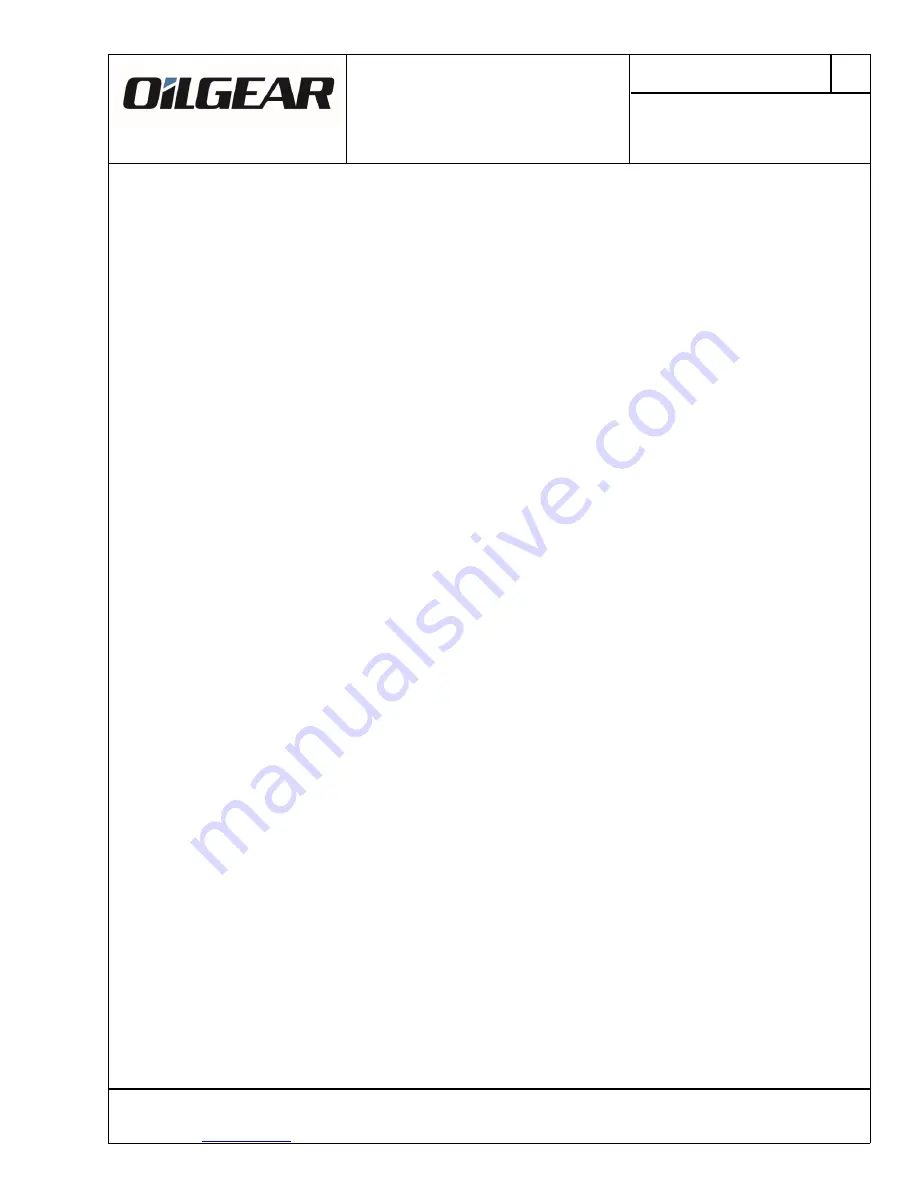
EPC
SERVO AMPLIFIER MODULE
Part Number L723888-3xx
ELECTRONIC
Telephone: (231) 929-1660
Oilgear
Fax:
(231) 929-7879
1424 International Dr
Issued May 31, 2018
Web Site:
www.oilgear.com
Traverse City, MI USA 4 9 6 8 6
Bulletin 836260F
12
4.1.5 USB Communication
The PC software interface must be configured properly to communicate to the EPC module. The
EPC should be connected via the USB-B connecter on the front of the device, and it carries an
internal USB-232 converter, but if necessary, download the appropriate driver from
http://www.ftdichip.com/drivers/VCP.htm. The COM port number will be assigned when the
driver installs (check your device manager for that COM port #) and baud rate is listed on the
General Configuration Form. See Figure 3.
4.1.6 Update Rate
The PC interface will update on-line information as quickly as possible. Often times this can be
improved by limiting the number of Windows™ applications. Typically, the EPC update rate will be
maximized in the 2 to 3 Hz range. See Figure 3.
4.2 Program Configuration
4.2.1 Overview
The EPC offers 12 pre-defined programs. The programs range from simple flow control to
advanced functionality. Six different types of programs exist, and the module provides two distinct
copies of each program.
Programs 1 and 2 provide Pressure Control programs. Programs 3 and 4 provide Flow with
Pressure Limit Control programs. Programs 5 and 6 provide Load Sense Control programs.
Programs 7 and 8 provide Simple Flow Control programs. Programs 9 and 10 provide Pressure
Control with Flow Preset programs. Finally, Programs 11 and 12 provide Advanced Control with
Feed-Forward.
Programs 3, 4, 9, and 10 have been modified since the manual 3 revisions ago (Bulletin 83260A) to
improve performance. This software enhancement is called Generation 2. It requires EPC software
versions 1.07 or later and PC Interface software version 1.55.0014 or later. See Appendix A for
Generation 1 information.
Programs 11 and 12 require EPC software versions 1.10 or later and PC Interface software
version 1.20 or later.
Under usual circumstances, the pre-defined programs are used as outer loop control. The output of
the pre-defined programs is normally passed through to the Pump Controller module (refer to
Section 4.3.1 for an overview of the Pump Controller).
4.2.2 PI Control Algorithms
Most programs use a PI (Proportional with Integral) control scheme. Although an advanced tutorial on
digital control systems is beyond the scope of this technical document some level of knowledge and
experience is necessary to successfully implement the control programs.
The basis of a PI controller is that an output signal is produced due to a difference between a
command and feedback term (the difference is usually referred to as
Error
). The output signal
for a PI control is made of a proportional error signal combined with an integral error signal.